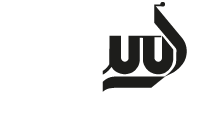
کربوره کردن (Carburizing) چیست؟ انواع، مزایا و کاربردها
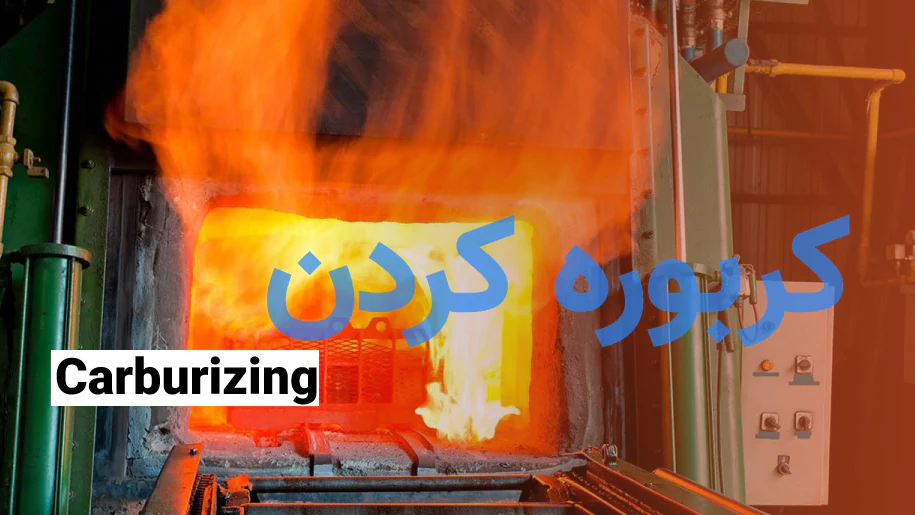
بسیاری از قطعات صنعتی، مانند چرخدندهها و شافتها، باید در شرایط بسیار سختی کار کنند. سطح آنها باید در برابر سایش و اصطکاک مداوم مقاوم باشد، اما کل قطعه نیز باید بتواند ضربهها و فشارهای ناگهانی را بدون شکستن تحمل کند. ایجاد این “شخصیت دوگانه” در یک قطعه فولادی، دقیقاً همان کاری است که فرآیند کربوره کردن (Carburizing) یا سمانتاسیون انجام میدهد.
در این راهنمای جامع، به زبان ساده بررسی میکنیم که کربوره کردن چیست، چه مزایای کلیدی برای صنعت دارد، انواع روشهای آن کدامند و در چه کاربردهایی مورد استفاده قرار میگیرد.
مزایای کلیدی کربوره کردن در صنعت
این فرآیند به دلیل مزایای متعدد، یکی از پرکاربردترین روشهای سختکاری سطحی است:
- افزایش مقاومت به سایش: لایه سخت سطحی (Case)، عمر قطعاتی که در تماس و اصطکاک مداوم هستند را به شکل چشمگیری افزایش میدهد.
- بهبود عمر خستگی: سطح سختشده از شروع ترکهای ریز ناشی از بارهای تکراری و متناوب جلوگیری کرده و دوام قطعه را در بلندمدت تضمین میکند.
- حفظ چقرمگی هسته: مغز نرم و انعطافپذیر قطعه، قابلیت جذب ضربه را حفظ کرده و از شکست ناگهانی و شکننده قطعه جلوگیری میکند.
- صرفهجویی اقتصادی: این فرآیند امکان استفاده از فولادهای کمکربن که ارزانتر هستند را فراهم میکند و در عین حال، خواصی مشابه فولادهای آلیاژی گرانقیمت در سطح ایجاد میکند.
انواع روشهای کربوره کردن (مقایسه کاربردی)
فرآیند کربوره کردن بر اساس محیطی که کربن را به فولاد میرساند، به چند روش اصلی تقسیم میشود. انتخاب هر روش به عواملی مانند دقت مورد نیاز، هزینه، و تیراژ تولید بستگی دارد.
۱. کربوره کردن گازی (Gas Carburizing)
این روش به دلیل کنترل دقیق و یکنواختی بالا، رایجترین و محبوبترین روش صنعتی است.
کاربردها: تولید انبوه قطعات دقیق و حساس مانند چرخدندههای خودرو، شافتها و بلبرینگها.
مکانیسم فرآیند: قطعات فولادی در یک کوره با اتمسفر کنترلشده قرار میگیرند که حاوی گازهای غنی از کربن مانند متان (CH₄) یا پروپان (C₃H₈) است. در دمای بالا (۸۵۰ تا ۹۵۰ درجه سانتیگراد)، این گازها تجزیه شده و کربن فعال به سطح فولاد نفوذ میکند.
مزایا:
کنترل دقیق: امکان کنترل دقیق بر عمق نفوذ و درصد کربن سطح وجود دارد.
یکنواختی بالا: لایه سخت شده در تمام سطوح قطعه، حتی در اشکال پیچیده، کاملاً یکنواخت است.
سرعت مناسب: فرآیند نسبت به روش جامد سریعتر است و برای تولید انبوه مناسب است.
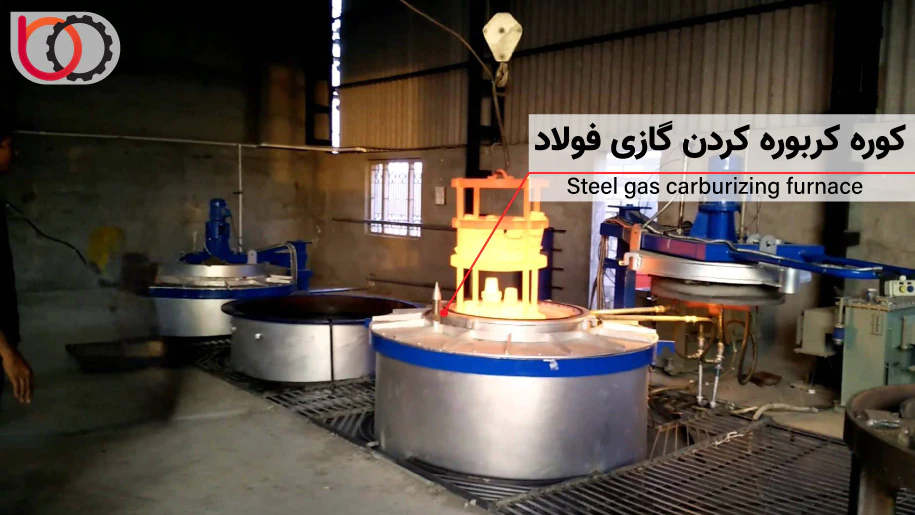
۲. کربوره کردن جامد (Pack Carburizing)
این روش، سنتیترین و کمهزینهترین تکنیک کربوره کردن است.
- کاربردها: قطعات بزرگ و غیرحساس که نیاز به لایه سخت عمیق دارند.
- مکانیسم فرآیند: قطعه درون یک جعبه فلزی به همراه مواد کربندار جامد (مانند پودر زغال و کربنات باریم) بستهبندی شده و حرارت داده میشود.
مزایا:
- سادگی و هزینه پایین: نیاز به تجهیزات پیچیده ندارد.
- ایجاد لایههای عمیق: برای ایجاد لایههای کربوره با عمق زیاد مناسب است.
معایب:
- کنترل ضعیف: کنترل دقیقی بر روی عمق و یکنواختی لایه وجود ندارد.
- زمانبر بودن: فرآیند بسیار کند است.
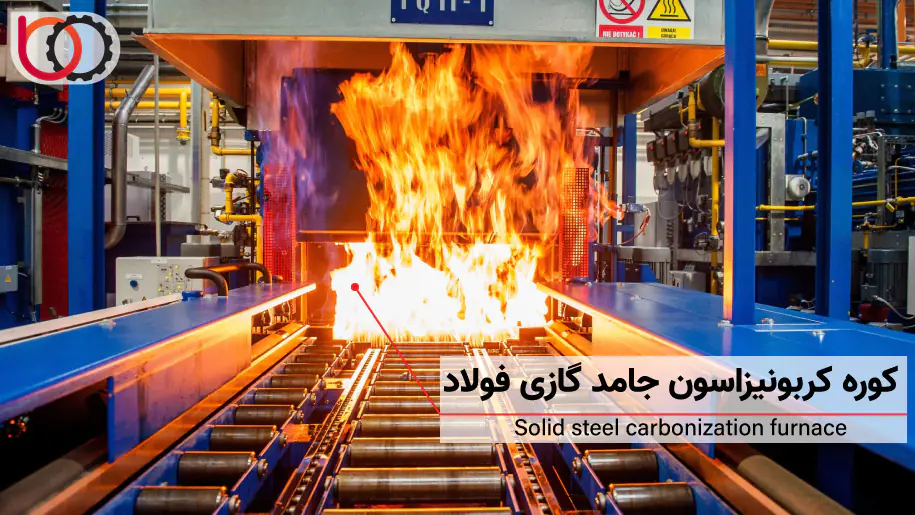
۳. کربوره کردن مایع (Liquid Carburizing)
این روش به دلیل سرعت بالا شناخته میشود.
- کاربردها: تولید قطعات کوچک و متوسط در تیراژ بالا که نیاز به فرآیند سریع دارند.
- مکانیسم فرآیند: قطعه در یک حمام نمک مذاب که حاوی ترکیبات کربندار (معمولاً سیانیدی) است، غوطهور میشود.
مزایا:
- سرعت بسیار بالا: سریعترین نرخ نفوذ کربن را در بین روشهای سنتی دارد.
- انتقال حرارت یکنواخت: باعث کاهش اعوجاج و تاب برداشتن قطعه میشود.
معایب:
- خطرات ایمنی و زیستمحیطی: استفاده از نمکهای سیانیدی بسیار سمی و خطرناک است.
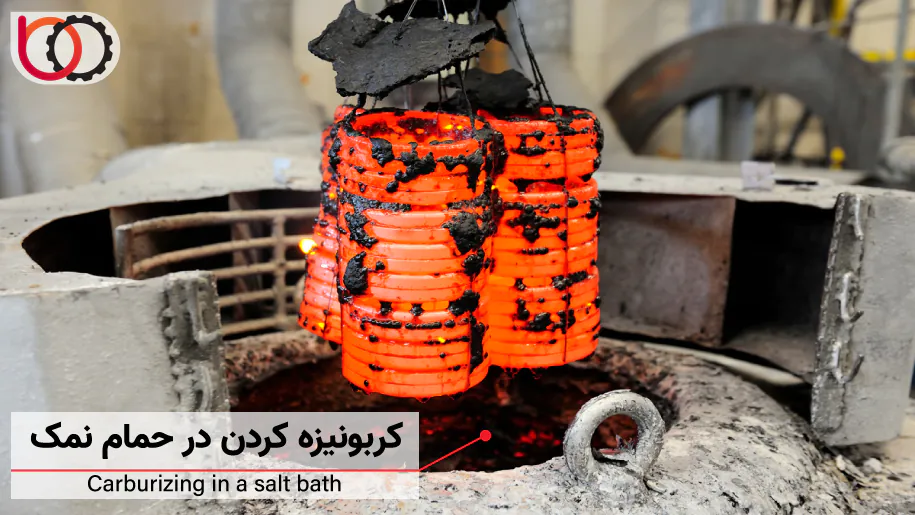
۴. کربوره کردن پلاسمایی (Plasma)
کربوره کردن پلاسمایی یکی از پیشرفتهترین و پیچیدهترین روشهای عملیات حرارتی برای سختسازی سطحی فولادهای کمکربن است که با استفاده از فناوری پلاسما و گازهای کربنی، امکان نفوذ دقیق و کنترلشدهی اتمهای کربن به سطح فولاد را فراهم میآورد. این فرآیند به دلیل بهرهگیری از میدانهای الکتریکی و پلاسمای یونیزهشده، مزایای قابلتوجهی در مقایسه با روشهای سنتی همچون کربوره کردن گازی و جامد دارد.
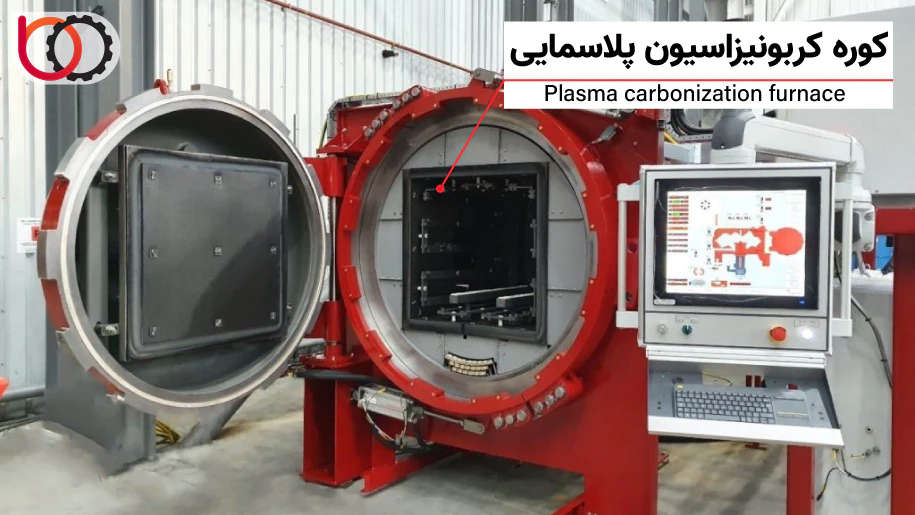
کربوره کردن خلاء
کربوره کردن خلاء یا (Vacuum Carburizing) یکی از پیشرفتهترین و تخصصیترین روشهای عملیات حرارتی سطحی است که با استفاده از فناوری خلاء و گازهای کربنی خاص مانند استیلن (C₂H₂) یا متان (CH₄) انجام میشود. این روش به دلیل نبود اکسیژن و سایر گازهای مزاحم در محیط واکنش، امکان کنترل بسیار دقیق فرآیند نفوذ کربن به سطح قطعات فولادی را فراهم میآورد و باعث افزایش کیفیت سطحی و یکنواختی لایه کربورهشده میشود.
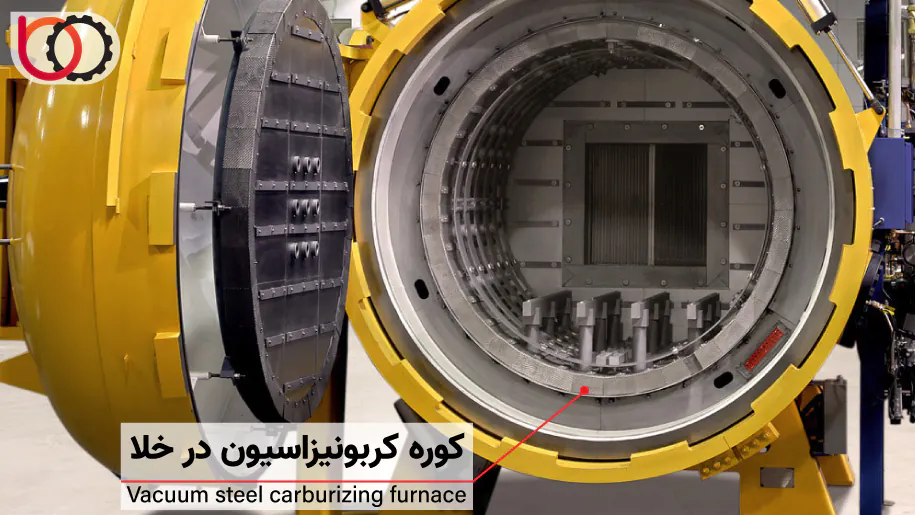
چه فولادهایی را میتوان کربوره کرد؟ (فولادهای سمانته)
فرآیند کربوره کردن به طور خاص برای فولادهای کمکربن (معمولاً با ۰.۱ تا ۰.۳ درصد کربن) طراحی شده است. دلیل این امر این است که این فولادها به دلیل کربن پایین، مغز نرم و چقرمهای دارند اما قابلیت سختکاری مستقیم را ندارند. فرآیند کربوره کردن، کربن لازم برای سخت شدن را فقط به لایه سطحی اضافه میکند.
مقاله پیشنهادی: فولاد سمانته چیست؟ کاربردها و انواع
ملاحظات طراحی و عملیات حرارتی تکمیلی
برای دستیابی به یک قطعه نهایی با کیفیت و بدون نقص، علاوه بر خود فرآیند کربوره کردن، باید به نکات طراحی و مراحل حرارتی پس از آن نیز توجه ویژه داشت:
- پرهیز از گوشههای تیز: در طراحی قطعه، باید از گوشههای تیز پرهیز کرد و آنها را با شعاع مناسب (گرد) طراحی نمود. گوشههای تیز محل تمرکز تنش هستند و ریسک ترکخوردگی در مرحله سرد کردن را به شدت بالا میبرند.
- یکنواختی ضخامت: تا حد امکان، ضخامت قطعه باید یکنواخت باشد. تغییرات ناگهانی در ضخامت باعث سرد شدن غیریکنواخت و در نتیجه، تاب برداشتن یا اعوجاج قطعه میشود.
- کوئنچ کردن (Quenching): پس از کربوره کردن، قطعه باید به سرعت (معمولاً در روغن) سرد شود تا لایه سطحی آن سخت گردد. این مرحله سختی مورد نیاز را ایجاد میکند اما قطعه را شکننده میسازد.
- برگشت دادن (Tempering): برای رفع این شکنندگی و افزایش چقرمگی، قطعه مجدداً در دمای پایین حرارت داده میشود. این مرحله تنشهای داخلی را آزاد کرده و قطعه را برای تحمل ضربه آماده میکند.
بهترین و متداولترین گروه از این فولادها، فولادهای سمانتاسیون یا سمانته (Case-Hardening Steels) نام دارند که به طور ویژه برای این فرآیند مهندسی شدهاند. گریدهایی مانند فولاد 1.7131 (16MnCr5) نمونههای بارزی از این خانواده هستند که پس از کربوره شدن، به خواص مکانیکی فوقالعادهای دست پیدا میکنند.
مبانی علمی فرآیند (برای مطالعه پیشرفته)
برای علاقهمندان به درک عمیقتر متالورژی، فرآیند کربوره کردن بر پایه اصول فیزیکی و شیمیایی دقیقی استوار است. در ادامه به بررسی این مبانی میپردازیم.
اصول ترمودینامیک و نفوذ اتمهای کربن
فرایند کربوره کردن بر پایه اصول ترمودینامیکی انتقال اتمهای کربن به درون ساختار متالورژیکی فولادهای کمکربن (مانند: فولاد سمانته) در دماهای بالا استوار است. این فرآیند در دمای بالای 850 درجه سانتیگراد (معمولاً بین 850 تا 950 درجه سانتیگراد) انجام میشود که در آن، فولاد وارد فاز آستنیتی (FCC) میشود. فاز آستنیت به دلیل داشتن فضای بینابینی بیشتر در ساختار کریستالی خود، حلالیت بالایی برای کربن دارد. این حلالیت بالا، قابلیت نفوذ سریعتر و عمیقتر اتمهای کربن به ساختار فولاد را فراهم میکند.
در محیطهای غنی از کربن، مانند گازهای حاوی مونوکسید کربن (CO) یا هیدروکربنها (CH₄)، اتمهای کربن تحت تأثیر تفاوت انرژی شیمیایی و پتانسیل شیمیایی بین سطح فولاد و محیط اطراف به سمت سطح قطعه حرکت میکنند. این تفاوت انرژی، منجر به نفوذ اتمهای کربن به سطح فولاد و سپس حرکت آنها به لایههای زیرین میشود. میزان نفوذ اتمهای کربن تابع شرایط ترمودینامیکی از جمله دما، فشار و غلظت کربن در محیط است.
افزایش دما باعث افزایش انرژی جنبشی اتمهای کربن و کاهش موانع انرژی برای نفوذ به ساختار کریستالی فولاد میشود. با افزایش زمان و دما، غلظت کربن در سطح فولاد بیشتر میشود و این افزایش غلظت به مرور به لایههای زیرین نفوذ میکند. این فرآیند نفوذ عمیقتر کربن به فولاد به ایجاد لایهای سخت و مقاوم به سایش در سطح قطعه منجر میشود، در حالی که مغز فولاد همچنان نرم و انعطافپذیر باقی میماند.
قانون فیک و سینتیک نفوذ
نفوذ اتمهای کربن به داخل شبکه کریستالی فولاد بر اساس قوانین نفوذ فیک (Fick’s Laws of Diffusion) تعریف میشود. این قوانین به بررسی حرکت و توزیع اتمهای کربن در طول زمان و فضای سهبعدی شبکه فولاد میپردازند.
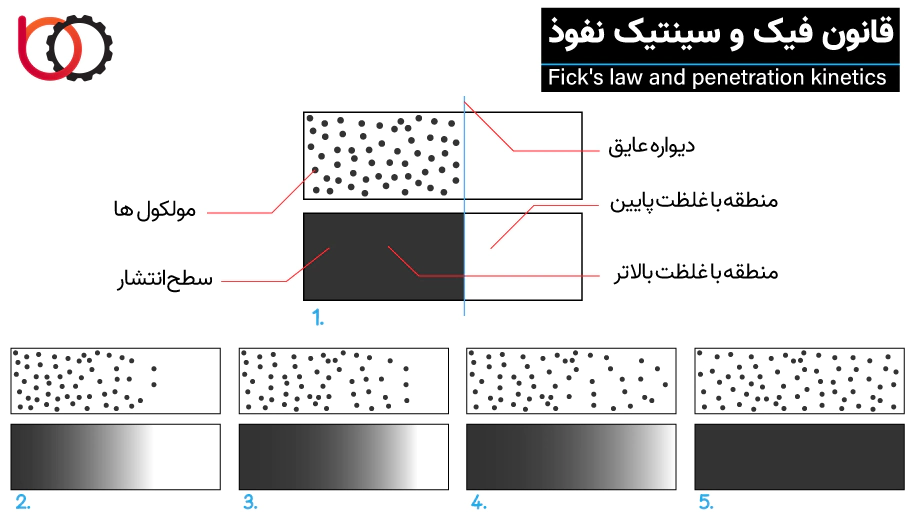
قانون اول فیک چیست؟
قانون اول فیک رابطهای بین شار نفوذ ((J)) و گرادیان غلظت ماده در طول یک مسیر مشخص ((x)) برقرار میکند:
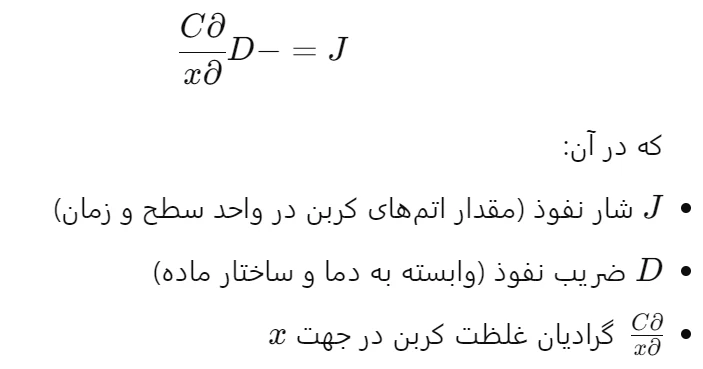
این قانون نشان میدهد که نفوذ اتمهای کربن به سمت نواحی با غلظت پایینتر انجام میگیرد و ضریب نفوذ ((D)) مستقیماً به دما وابسته است. هرچه دما بیشتر باشد، ضریب نفوذ بالاتر میرود و اتمهای کربن سریعتر حرکت میکنند. بهعلاوه، افزایش دما باعث کاهش انرژی فعالسازی برای نفوذ شده و فرآیند نفوذ را تسریع میکند.
قانون دوم فیک چیست؟
قانون دوم فیک توزیع غلظت ماده در طول زمان را در فضای سهبعدی توصیف میکند. معادله این قانون به شرح زیر است:
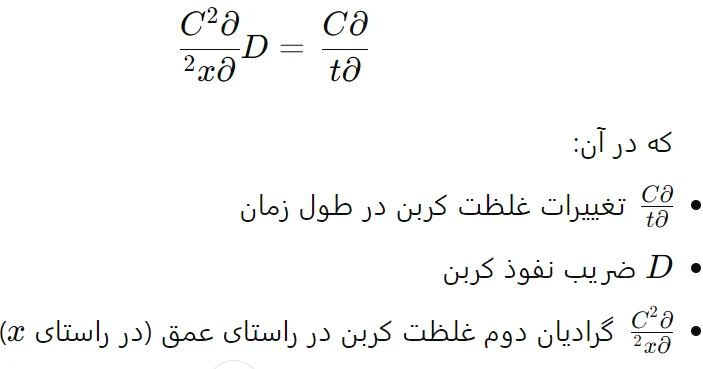
این معادله بیان میکند که تغییرات غلظت کربن در طول زمان چگونه به گرادیان دوم غلظت و ضریب نفوذ وابسته است. در فرآیند کربوره کردن، با گذر زمان، اتمهای کربن به لایههای زیرین فولاد نفوذ میکنند و این فرآیند به طور نمایی با کاهش سرعت نفوذ در عمقهای بیشتر همراه است. به عبارت دیگر، هرچه زمان بیشتری صرف شود، کربن به لایههای عمیقتر میرسد، اما با سرعت کمتری نسبت به لایههای سطحی.
سینتیک نفوذ
سینتیک نفوذ اتمهای کربن به فولاد تابعی از دما و زمان است. ضریب نفوذ (D) تابعی نمایی از دما است و بر اساس معادله زیر عمل میکند:
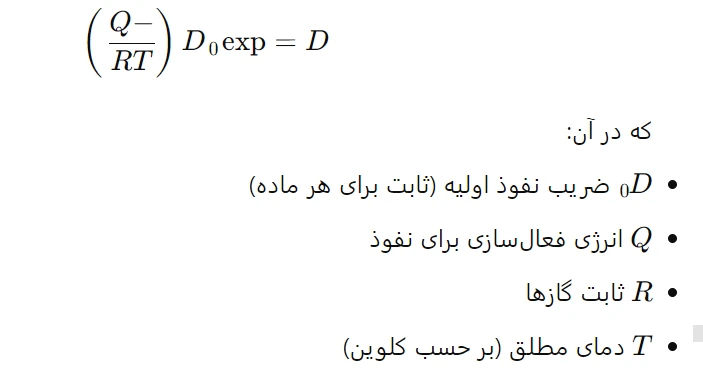
افزایش دما باعث افزایش ضریب نفوذ (D) و کاهش انرژی فعالسازی مورد نیاز برای نفوذ اتمهای کربن میشود. به این ترتیب، در دماهای بالاتر، فرآیند نفوذ سریعتر انجام شده و اتمهای کربن به سرعت بیشتری به عمقهای مختلف فولاد نفوذ میکنند. با این حال، زمان نیز نقش مهمی در توزیع غلظت کربن در طول عمق فولاد دارد؛ هرچه زمان فرآیند طولانیتر باشد، اتمهای کربن فرصت بیشتری برای نفوذ به لایههای زیرین پیدا میکنند.
کنترل دقیق پارامترهای دما، زمان، و غلظت کربن در محیط فرآیند کربوره کردن به مهندسان متالورژی این امکان را میدهد که عمق نفوذ کربن و خواص مکانیکی نهایی قطعه را با دقت بالایی کنترل کنند. این امر به تولید قطعاتی با سطح بسیار سخت و مقاوم به سایش همراه با مغزی نرم و مقاوم به شوکهای مکانیکی منجر میشود.
تاثیر عناصر آلیاژی بر فرآیند کربوره کردن
عناصر آلیاژی مانند کروم، نیکل، مولیبدن و دیگر عناصر در فولاد، تأثیرات مهمی بر فرآیند کربوره کردن و ویژگیهای نهایی قطعه پس از عملیات حرارتی دارند. این عناصر میتوانند بر عمق نفوذ کربن، سرعت کربوره کردن و سختی سطحی فولاد پس از کربوره کردن اثرگذار باشند. در ادامه تأثیر هر یک از این عناصر را بررسی میکنیم:
1. کروم (Chromium)
- تأثیر بر عمق نفوذ کربن: کروم در فولاد تأثیر معکوسی بر نفوذ کربن دارد. وجود کروم باعث کاهش سرعت نفوذ کربن به سطح فولاد میشود. دلیل این امر این است که کروم با کربن ترکیب شده و کاربیدهای کروم (Cr₃C₂ یا Cr₇C₃) تشکیل میدهد که این کاربیدها به عنوان مانعی در برابر نفوذ کربن عمل میکنند.
- تأثیر بر خواص نهایی: در عین حال، کروم باعث افزایش سختی سطحی و مقاومت به سایش میشود و همچنین مقاومت به اکسیداسیون و خوردگی سطح را افزایش میدهد. فولادهای آلیاژی با کروم در فرآیند کربوره کردن معمولاً به زمان طولانیتری برای رسیدن به عمق نفوذ مورد نظر نیاز دارند.
2. نیکل (Nickel)
- تأثیر بر عمق نفوذ کربن: نیکل برخلاف کروم، تأثیر چندانی بر کاهش نفوذ کربن ندارد. نیکل بهطور مستقیم مانع نفوذ کربن نمیشود و حضور آن باعث کاهش سرعت کربوره کردن نمیگردد.
- تأثیر بر خواص نهایی: نیکل با بهبود چقرمگی و استحکام فولاد پس از عملیات کربوره کردن، به حفظ توازن میان سختی سطحی و مقاومت به ضربه در هسته قطعه کمک میکند. همچنین نیکل باعث بهبود پایداری ابعادی فولاد پس از عملیات حرارتی میشود.
3. مولیبدن (Molybdenum)
- تأثیر بر عمق نفوذ کربن: مولیبدن مانند کروم میتواند باعث کاهش سرعت نفوذ کربن شود. این عنصر نیز کاربیدهای مقاومی را تشکیل میدهد (مانند کاربیدهای مولیبدن، Mo₂C) که نفوذ کربن را محدود میکند.
- تأثیر بر خواص نهایی: مولیبدن به بهبود مقاومت فولاد در برابر خزش و حرارت کمک میکند. همچنین باعث افزایش سختی سطحی و مقاومت به سایش میشود. مولیبدن در کنار کروم، فولاد را در برابر ترکخوردگی در شرایط بارگذاری سنگین و دمای بالا مقاومتر میکند.
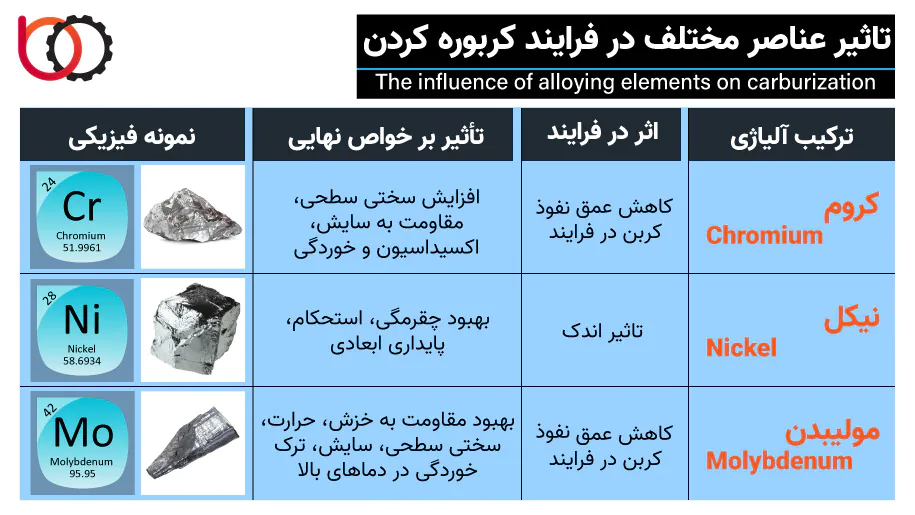
4. منگنز (Manganese)
- تأثیر بر عمق نفوذ کربن: منگنز به افزایش سرعت نفوذ کربن کمک میکند و برخلاف کروم و مولیبدن، باعث افزایش سرعت کربوره کردن میشود. دلیل این امر این است که منگنز تمایل کمتری به تشکیل کاربیدهای پایدار با کربن دارد و نفوذ کربن را تسهیل میکند.
- تأثیر بر خواص نهایی: منگنز با بهبود سختیپذیری فولاد، به افزایش سختی سطحی کمک میکند و همچنین مقاومت در برابر سایش و خواص مکانیکی کلی را بهبود میبخشد.
5. سیلیسیم (Silicon)
- تأثیر بر عمق نفوذ کربن: سیلیسیم به کاهش سرعت نفوذ کربن کمک میکند، زیرا تمایل به تشکیل کاربیدهای سیلیسی وجود دارد که میتوانند تا حدودی مانع نفوذ کربن به سطح شوند.
- تأثیر بر خواص نهایی: سیلیسیم معمولاً بهعنوان یک عنصر تقویتکننده استحکام در فولاد عمل میکند و باعث افزایش مقاومت به سایش و سختی میشود. اما حضور بیش از حد آن میتواند شکنندگی را افزایش دهد.
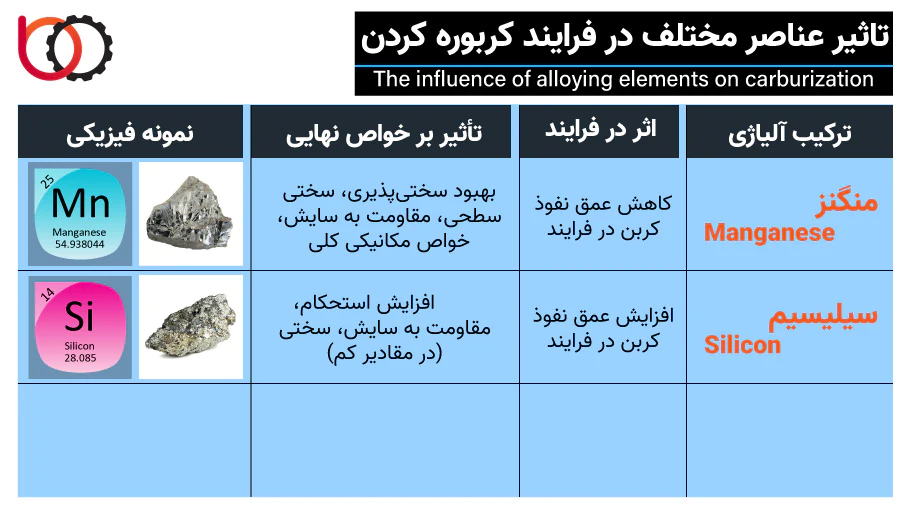
عملیات حرارتی پس از کربوره کردن( تمپرینگ پس از کوئنچ)
عملیات حرارتی پس از کربوره کردن نقش بسیار مهمی در دستیابی به خواص مکانیکی نهایی قطعه دارد. پس از انجام فرآیند کربوره کردن، سطح فولاد سخت میشود، اما برای بهبود خواص مکانیکی مانند چقرمگی و کاهش تنشهای داخلی، عملیاتهای تکمیلی همچون کوئنچ (سرد کردن سریع) و تمپرینگ (بازپخت) انجام میشوند. برخی از فرآیندهای حرارتی پس از کربوره کردن عبارتند از:
1. کوئنچ (Quenching)
پس از کربوره کردن، قطعه باید بهسرعت سرد شود تا ساختار مارتنزیتی در سطح ایجاد شود که منجر به افزایش سختی میگردد. کوئنچ کردن معمولاً در محیطهای مختلفی مانند:
- آب (برای فولادهای با آلیاژ کم و کربن بالا)
- روغن (برای فولادهای با آلیاژ متوسط و فولادهای کم کربن)
- نمکهای مذاب یا گازها (برای شرایط خاص)
در کوئنچ، سرد کردن سریع باعث میشود که اتمهای کربن در سطح فولاد در محلول جامد باقی بمانند و ساختار مارتنزیت که سخت و شکننده است، تشکیل شود. این فرآیند باعث افزایش سختی سطحی میشود، اما همزمان تنشهای داخلی و شکنندگی را نیز افزایش میدهد.
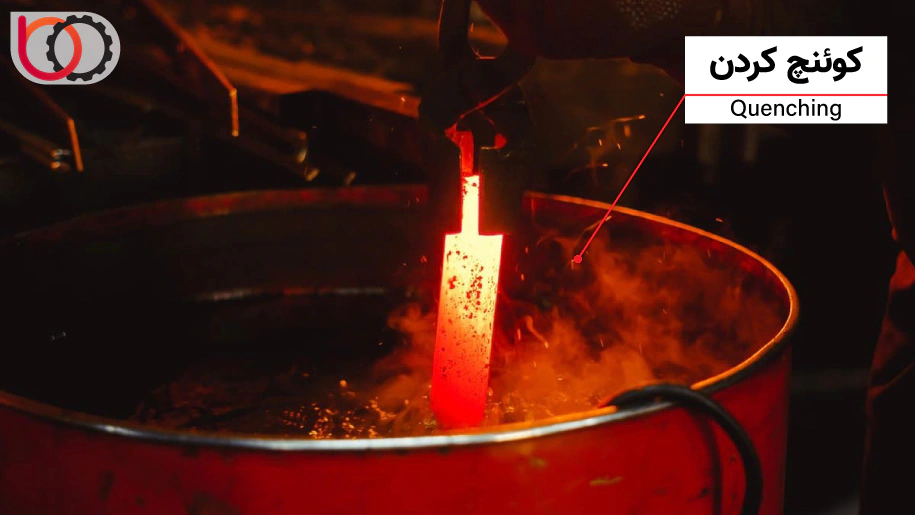
2. تمپرینگ (Tempering)
پس از کوئنچ، قطعه فولادی بسیار سخت و شکننده است و نیاز به عملیات تمپرینگ دارد تا این شکنندگی کاهش یابد و چقرمگی افزایش پیدا کند. تمپرینگ یک فرآیند حرارتی است که در آن قطعه تا دمایی پایینتر از دمای تبدیل مارتنزیت به آستنیت (معمولاً بین 150 تا 650 درجه سانتیگراد) دوباره گرم میشود. تمپرینگ باعث بهبود خواص فولاد به روشهای زیر میشود:
- کاهش تنشهای داخلی: کوئنچ کردن باعث ایجاد تنشهای داخلی در قطعه میشود که این تنشها میتوانند منجر به ترکخوردگی یا شکست قطعه در زمان سرویس شوند. با انجام تمپرینگ، این تنشها کاهش پیدا میکنند و ساختار فولاد به پایداری بیشتری میرسد.
- افزایش چقرمگی: با افزایش دمای تمپرینگ، ساختار مارتنزیتی به ساختارهای پایدارتر و نرمتری مانند بینیت یا فریت تبدیل میشود. این تغییر باعث افزایش چقرمگی و کاهش شکنندگی قطعه میشود، بدون این که بهطور قابل توجهی سختی سطحی کاهش یابد.
- تنظیم سختی نهایی: دمای تمپرینگ قابل تنظیم است و میتوان بسته به نیازهای مکانیکی و سختی مورد نظر، سختی نهایی را کنترل کرد. معمولاً با افزایش دمای تمپرینگ، سختی کاهش و چقرمگی افزایش مییابد.
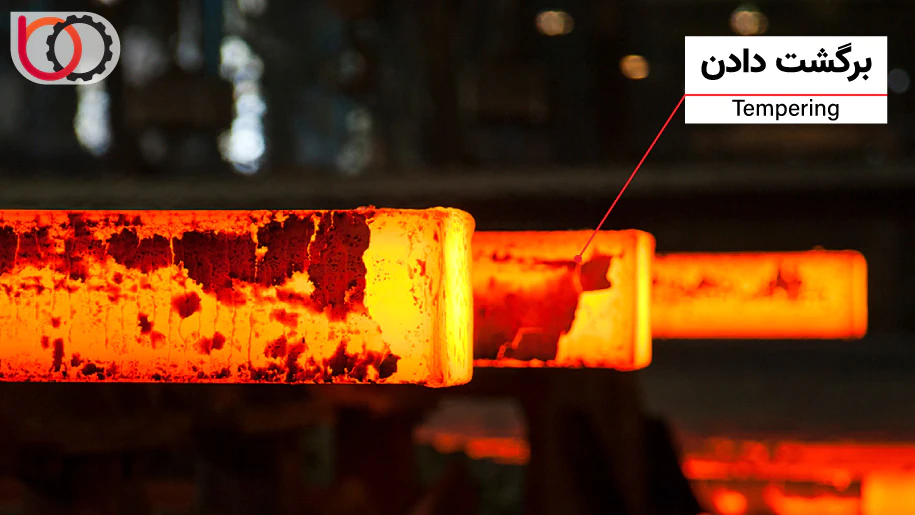
مراحل عملیات حرارتی پس از کربوره کردن
- آستنیته کردن (Austenitizing): در این مرحله، قطعه به دمایی گرم میشود که ساختار آستنیت در سطح و هسته قطعه ایجاد شود. این مرحله معمولاً قبل از کوئنچ انجام میشود.
- کوئنچ: پس از آستنیته کردن، قطعه بهسرعت در محیط سردکننده (آب، روغن یا گاز) سرد میشود تا ساختار مارتنزیتی در سطح قطعه تشکیل شود. این مرحله باعث افزایش سختی سطحی و مقاومت به سایش میشود.
- تمپرینگ: پس از کوئنچ، قطعه دوباره گرم میشود (معمولاً در دماهای پایینتر از 650 درجه سانتیگراد). تمپرینگ به کاهش تنشهای داخلی، افزایش چقرمگی و تنظیم سختی کمک میکند.
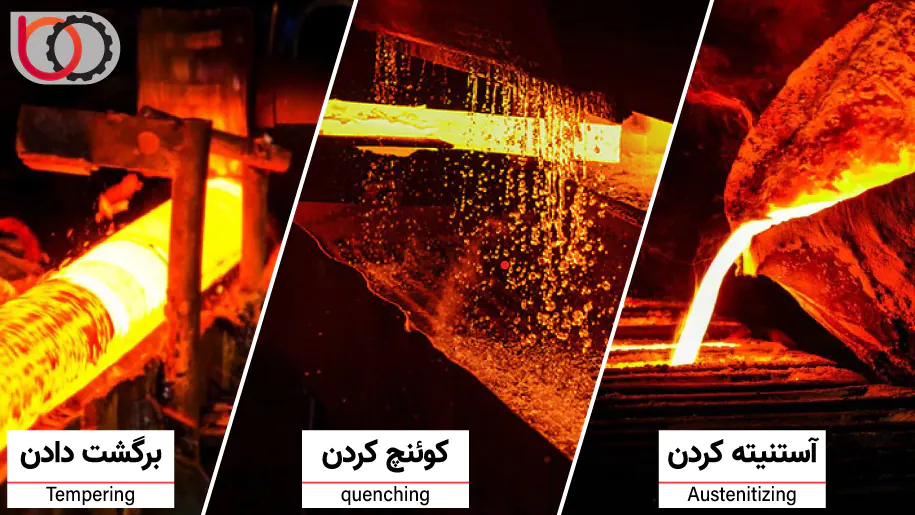
اثر دمای تمپرینگ
- دمای پایین (150-250 درجه سانتیگراد): در این دما، تمپرینگ منجر به کاهش تنشهای داخلی میشود بدون اینکه تأثیر قابل توجهی بر سختی بگذارد. قطعاتی که نیاز به حفظ بالاترین سختی دارند، در این دما تمپر میشوند.
- دمای متوسط (250-450 درجه سانتیگراد): در این دما، سختی به میزان کمی کاهش مییابد، اما چقرمگی و مقاومت به ضربه بهطور چشمگیری افزایش پیدا میکند.
- دمای بالا (450-650 درجه سانتیگراد): تمپرینگ در این دما منجر به کاهش بیشتر سختی و افزایش قابل توجه چقرمگی میشود. این فرآیند برای قطعاتی مناسب است که نیاز به تحمل بارهای سنگین دارند و در معرض ضربه هستند.
نکاتی درباره طراحی قطعات برای کربوره کردن
در طراحی قطعاتی که قرار است فرآیند کربوره کردن و عملیات حرارتی مانند کوئنچ و تمپرینگ بر روی آنها اعمال شود، باید ملاحظات خاصی در نظر گرفته شود تا از مشکلاتی مانند تغییر شکل و ترکخوردگی جلوگیری شود. این نکات به طراحان و مهندسان کمک میکند تا قطعات با کیفیت بهتری تولید کنند و همچنین مشکلاتی که ممکن است در حین عملیات حرارتی پیش بیاید را به حداقل برسانند. در ادامه به برخی از این نکات مهم عبارتند از:
1. انتخاب مناسب مواد
- استفاده از فولادهایی با ترکیب آلیاژی مناسب که قابلیت کربوره کردن دارند، بسیار مهم است. فولادهایی که دارای عناصر آلیاژی مانند کروم، نیکل و مولیبدن هستند، هم به بهبود خواص نهایی کمک میکنند و هم مقاومت در برابر ترکخوردگی و تغییر شکل را افزایش میدهند.
- در هنگام انتخاب مواد، باید به خواص مکانیکی هسته (Core) و سطح (Case) توجه شود. طراحی باید به گونهای باشد که فولاد در حین عملیات حرارتی به ترکیب مناسبی از سختی سطحی و چقرمگی هسته دست یابد.
2. پرهیز از تغییرات ناگهانی ضخامت
- قطعاتی که ضخامتهای متفاوتی دارند یا تغییرات ناگهانی در مقاطع مختلف آنها وجود دارد، در هنگام کوئنچ و سرد کردن سریع، بیشتر مستعد تغییر شکل و ایجاد تنشهای داخلی هستند.
- بهتر است طراحی قطعات به گونهای باشد که تغییرات ضخامت بهصورت تدریجی انجام شود و از تغییرات ناگهانی در مقاطع مختلف جلوگیری شود. این کار باعث میشود که قطعه بهصورت یکنواختتر در طول عملیات حرارتی سرد شود و از ایجاد تنشهای غیرضروری جلوگیری شود.
3. طراحی گوشههای گرد (Radiused Corners)
- وجود لبههای تیز و زاویههای حاد در طراحی میتواند منجر به تمرکز تنشهای حرارتی در هنگام کوئنچ شود که این موضوع احتمال ترکخوردگی را افزایش میدهد.
- بهتر است گوشهها و لبههای قطعات بهصورت گرد طراحی شوند تا تنشها بهصورت یکنواختتری در سراسر قطعه توزیع شوند. گوشههای گرد به کاهش ترکخوردگی و بهبود مقاومت قطعه در برابر شکست کمک میکنند.
4. پیشبینی تغییر شکل در طراحی
- برخی قطعات ممکن است در حین عملیات حرارتی بهویژه کوئنچ دچار تغییر شکل شوند. بنابراین، در طراحی اولیه باید تلرانسهای ابعادی به گونهای در نظر گرفته شوند که پس از تغییر شکلهای احتمالی، قطعه همچنان در محدودهی ابعادی مجاز باقی بماند.
- برای کاهش تغییر شکل، ممکن است نیاز باشد از پشتیبانیهای مکانیکی یا قابهای نگهدارنده در طول عملیات حرارتی استفاده شود تا قطعه در موقعیت مناسب نگه داشته شود و تغییر شکلها به حداقل برسد.
5. طراحی سوراخها و منافذ (Holes and Openings)
- قطعاتی که دارای سوراخها یا منافذ داخلی هستند، میتوانند در حین کوئنچ دچار تغییر شکل یا حتی ترکخوردگی شوند، بهویژه اگر سوراخها در مقاطع حساس قرار گرفته باشند.
- توصیه میشود که سوراخها به گونهای طراحی شوند که تنشهای حرارتی در حین کوئنچ به حداقل برسند. همچنین، استفاده از قطرهای استاندارد و جلوگیری از تغییرات ناگهانی در قطر سوراخها میتواند کمککننده باشد.
6. توجه به محدودیتهای ابعادی در کربوره کردن پلاسمایی
- در روشهای مدرنی مانند کربوره کردن پلاسمایی، ممکن است محدودیتهای ابعادی یا پیچیدگیهای بیشتری در طراحی قطعه وجود داشته باشد. به عنوان مثال، قطعاتی که دارای شکلهای بسیار پیچیده یا ابعاد بزرگ هستند ممکن است به یکنواختی در نفوذ کربن نرسند.
7. استفاده از پیشگرم کردن
- در برخی موارد، ممکن است پیشگرم کردن قطعه قبل از کوئنچ یا تمپرینگ کمک کند تا قطعه بهصورت یکنواختتری گرم و سرد شود. این روش میتواند از ایجاد تغییر شکل و ترکخوردگی در حین سرد شدن سریع جلوگیری کند.
- پیشگرم کردن بهویژه برای قطعات بزرگ یا با اشکال پیچیده که دچار تغییرات دمایی شدید میشوند، مفید است.
8. کنترل نرخ سرد شدن (Cooling Rate)
- انتخاب مناسب محیط کوئنچ (آب، روغن، هوا، یا گاز) و کنترل نرخ سرد شدن میتواند به جلوگیری از ترکخوردگی و تغییر شکل کمک کند. استفاده از محیطهای کوئنچ ملایمتر (مانند روغن یا گاز) برای قطعات حساس توصیه میشود.
- در قطعات بزرگ یا پیچیده، بهتر است از کوئنچهای تدریجی استفاده شود تا تنشهای حرارتی به حداقل برسد.
9. پیشبینی عملیات ماشینکاری پس از عملیات حرارتی
- ممکن است برخی از قطعات پس از عملیات کربوره کردن و عملیات حرارتی نیاز به ماشینکاری مجدد داشته باشند تا به تلرانسهای دقیقتری برسند. بنابراین در طراحی باید این موارد پیشبینی شده و ضخامتهای اضافی برای ماشینکاری در نظر گرفته شوند.
10. کنترل عمق نفوذ کربن
- در طراحی قطعاتی که کربوره کردن بر روی آنها انجام میشود، باید به عمق نفوذ کربن توجه شود. برای قطعاتی که نیاز به سختی سطحی دارند اما هسته باید نرم بماند، کنترل عمق نفوذ کربن بسیار مهم است تا از ترکخوردگی هسته جلوگیری شود.
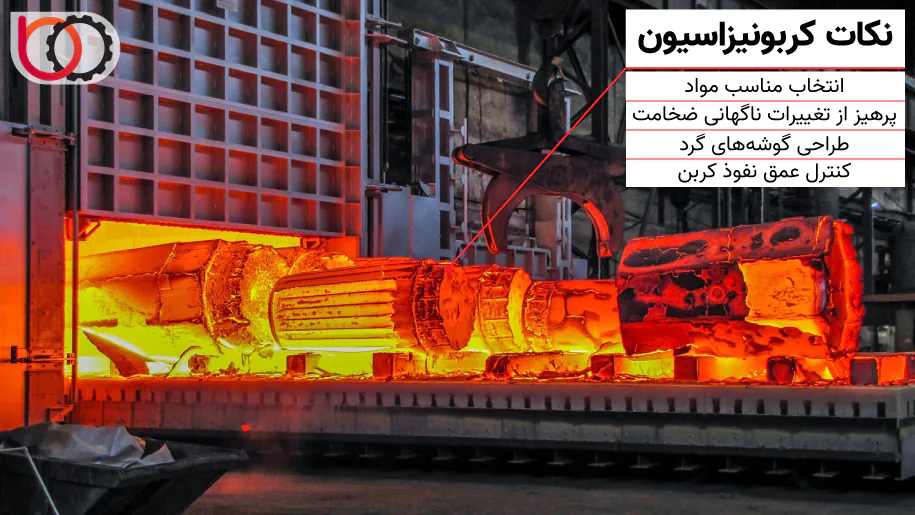