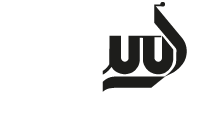
فولاد سمانته چیست؟ راهنمای کامل کاربردها، گریدها و خواص
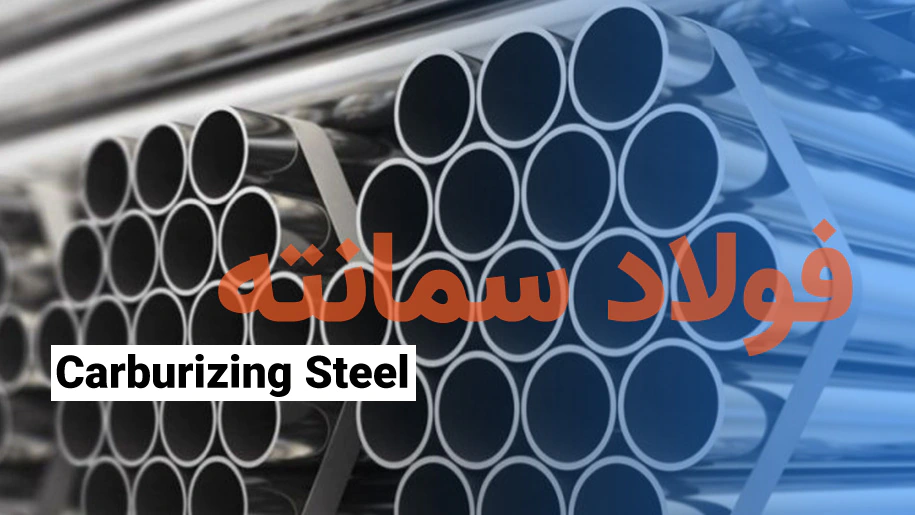
در صنعت، قطعاتی مانند چرخدندهها، شافتها و یاتاقانها مدام تحت فشار، سایش و ضربه قرار دارند. انتخاب فولاد اشتباه برای این قطعات میتواند منجر به شکست زودهنگام، توقف خط تولید و هزینههای سنگین شود. فولاد سمانته (Carburizing Steel) راهحلی هوشمندانه و مهندسی برای این چالش است. این فولاد با داشتن سطحی بسیار سخت و مغزی نرم و چقرمه، ترکیبی ایدهآل از مقاومت در برابر سایش و تحمل ضربه را فراهم میکند. در این راهنمای کامل، به زبان ساده بررسی میکنیم که فولاد سمانته چیست، چه کاربردهایی دارد، و چرا گریدهایی مانند 1.7131 تا این حد پرطرفدار هستند.
- مشخصات و خواص کلیدی فولاد سمانته
- کاربردهای اصلی فولاد سمانته
- کاربرد فولاد سمانته در ساخت چرخدنده
- نقش فولاد سمانته در افزایش عمر شافتها و محورها
- کاربرد فولاد سمانته در قطعات کلیدی موتور
- چرا فولاد سمانته در ساخت یاتاقانها کاربرد دارد؟
- ساخت ابزارآلات و گیرههای دقیق با فولاد سمانته
- نقش حیاتی فولاد سمانته در قطعات حساس هوافضا
- افزایش دوام قطعات نوار نقاله با فولاد سمانته
- استاندارد و گریدهای فولاد سمانته (سمانتاسیون)
- انواع، استانداردها و گریدهای معروف فولاد سمانتاسیون
- فرآیند تولید و عملیات حرارتی فولاد سمانته
مشخصات و خواص کلیدی فولاد سمانته
ارزش و کارایی فولاد سمانته، مستقیماً از ترکیب خاص خواص فیزیکی و مکانیکی آن ناشی میشود. ویژگی اصلی این فولاد، قابلیت آن در داشتن دو خصوصیت کاملاً متفاوت در یک قطعه واحد است: سطحی با سختی بسیار بالا برای مقاومت در برابر سایش، و مغزی نرم و انعطافپذیر (چقرمه) که میتواند ضربه و بارهای دینامیکی را تحمل کند.
آشنایی دقیق با این مشخصات، برای مهندسان و صنعتگران جهت انتخاب بهینه و استفاده صحیح از این فولاد ضروری است. در ادامه، به ترتیب به بررسی ترکیب شیمیایی، خواص مکانیکی (مانند سختی و استحکام)، ویژگیهای حرارتی و همچنین رفتار آن در برابر جوشکاری و ماشینکاری خواهیم پرداخت.
ترکیب شیمیایی فولاد سمانته
فولادهای سمانته معمولاً محتوای کربن کمی دارند (بین ۰.۱ تا ۰.۳ درصد). این مقدار کم کربن باعث میشود که هسته فولاد نرم و چقرمه بماند، در حالی که سطح آن پس از عملیات کربوره سخت میشود. برای بهبود خواص مکانیکی، این فولادها ممکن است حاوی عناصری مانند:
- کربن (C): ۰.۱ تا ۰.۳ درصد
- منگنز (Mn): ۰.۵ تا ۰.۹ درصد
- کروم (Cr): ۰.۵ تا ۲ درصد
- نیکل (Ni): ۰.۵ تا ۲ درصد
- مولیبدن (Mo): ۰.۱۵ تا ۰.۳ درصد
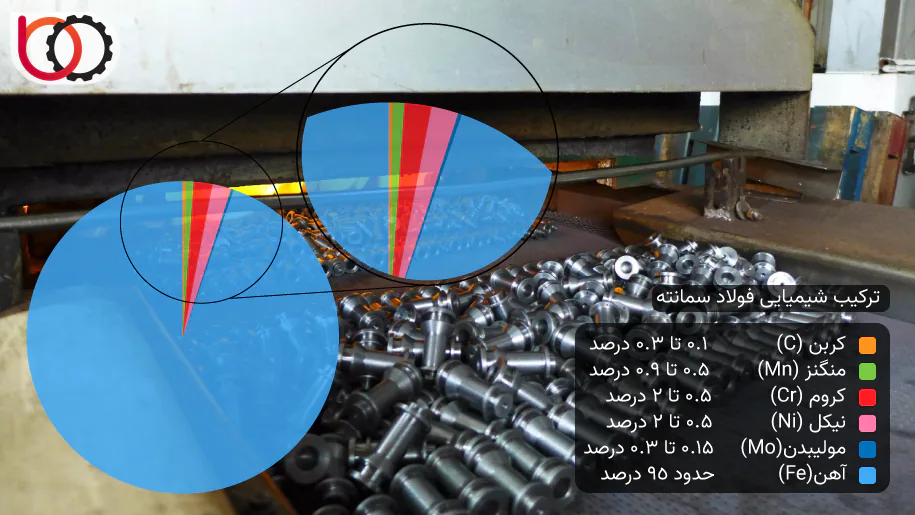
خواص مکانیکی فولاد سمانتاسیون
- سختی سطحی: پس از کربوره و کوئنچ، سختی سطح فولاد میتواند به حدود ۵۸ تا ۶۲ راکول C (HRC) برسد. این سختی سطحی بسیار بالا است و باعث افزایش مقاومت به سایش و خوردگی در سطح قطعه میشود.
- سختی هسته: هسته فولاد که تحت تأثیر کربندهی قرار نگرفته، معمولاً دارای سختی بین ۲۵ تا ۳۵ HRC است. این ترکیب از یک سطح سخت و یک هسته نرم باعث میشود قطعاتی که از فولاد سمانته ساخته شدهاند، مقاومت خوبی در برابر خستگی و ضربه داشته باشند.
- استحکام کششی: استحکام کششی نهایی فولاد سمانته پس از عملیات حرارتی بین ۸۰۰ تا ۱۰۰۰ مگاپاسکال است. این مقدار استحکام باعث میشود فولاد بتواند بارهای سنگین را بدون تغییر شکل دائمی تحمل کند.
- مدول الاستیسیته: حدود ۲۰۰ گیگاپاسکال، مشابه سایر فولادهای کمکربن.
- چقرمگی: به دلیل هسته نرم، فولاد سمانته چقرمگی خوبی دارد که آن را مناسب برای کاربردهای تحت بارگذاری دینامیکی میکند.
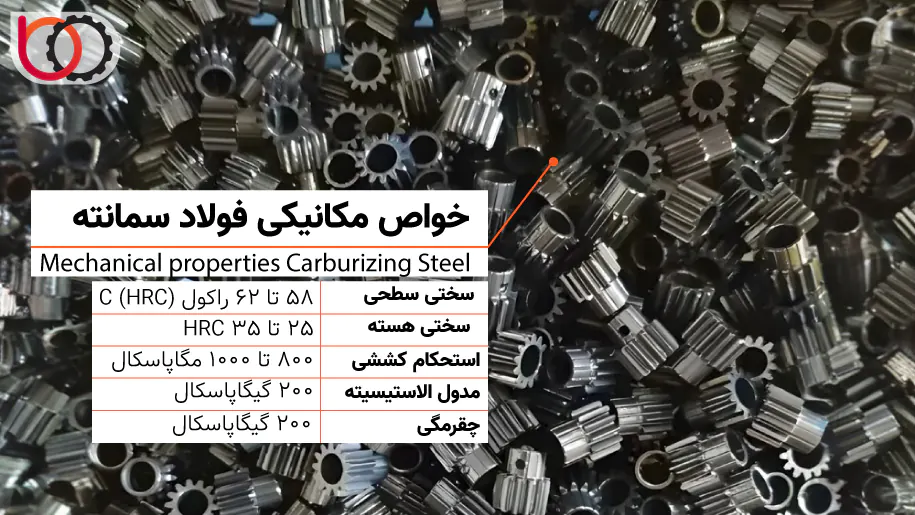
خواص حرارتی فولاد سمانته
- ضریب انبساط حرارتی: در حدود ۱۱ تا ۱۳ میکرومتر در متر بر درجه سانتیگراد.
- هدایت حرارتی: حدود ۴۰ تا ۵۰ وات بر متر کلوین.
نقطه ذوب و جوش فولاد سمانته چقدر است؟
نقطه ذوب فولاد سمانته مشابه سایر فولادهای کربنی است و در محدوده ۱۴۵۰ تا ۱۵۲۰ درجه سانتیگراد قرار دارد.
نقطه جوش آن نیز در حدود ۳۰۰۰ تا ۳۲۰۰ درجه سانتیگراد است، اما در عمل به ندرت نیاز به جوش آوردن فولادهای سمانته وجود دارد.
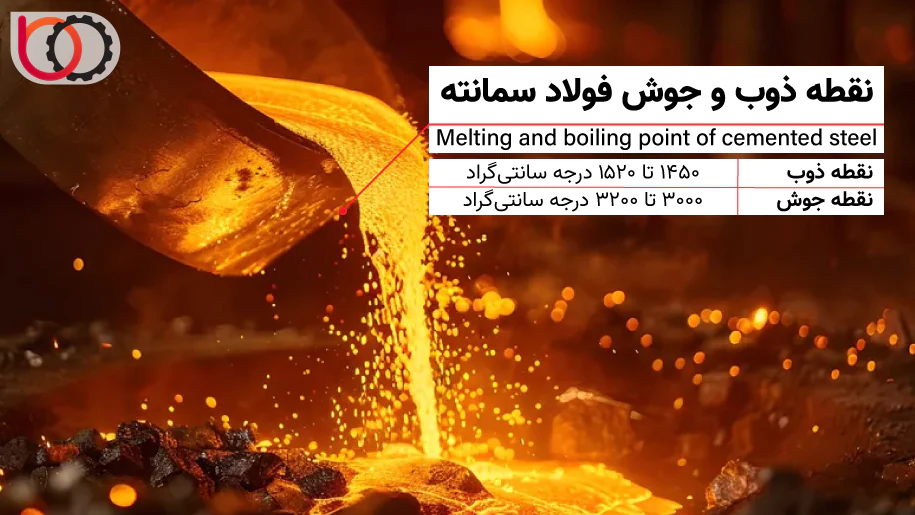
میزان جوشپذیری فولاد سمانته
فولاد سمانته به دلیل وجود عناصر آلیاژی و عملیات حرارتی پیشین، ممکن است جوشپذیری پایینی داشته باشد. جوشکاری این فولاد معمولاً نیاز به پیشگرم کردن و کنترل دقیق دمای جوش دارد تا از ترکخوردگی و نقص در جوش جلوگیری شود.
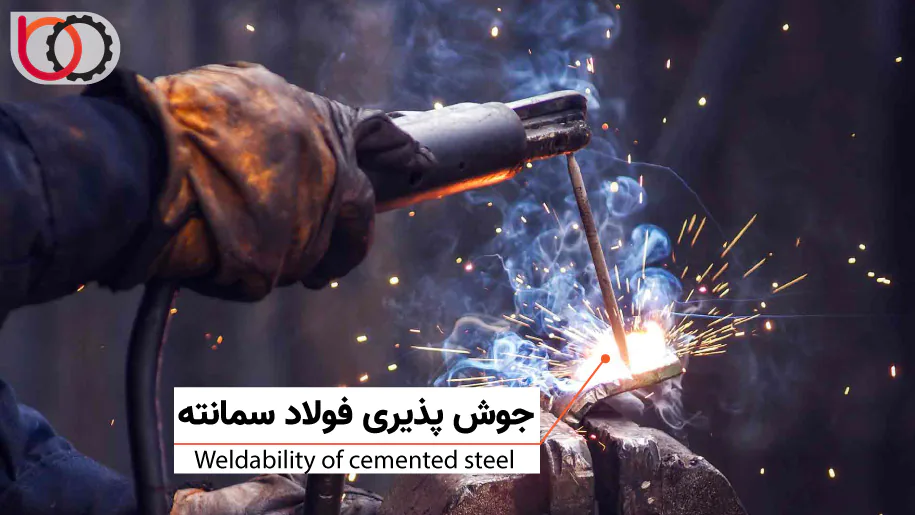
فولاد سمانته چه زمانی قابل ماشینکاری است؟
قبل از عملیات کربوره، فولاد سمانته بهخوبی قابل ماشینکاری است. اما پس از کربوره و کوئنچ، به دلیل سختی بالای سطح، ماشینکاری آن بسیار دشوار میشود و نیاز به ابزارهای سختتر مانند کاربید تنگستن دارد.
میزان مقاومت به خوردگی فولاد سمانتاسیون
فولاد سمانتاسیون مقاومت به خوردگی ذاتی بالایی ندارد و معمولاً برای کاربردهایی که در معرض رطوبت یا مواد شیمیایی قرار دارند، به پوششهای محافظ یا آبکاری نیاز دارد.
محدودیتهای استفاده از فولاد سمانتاسیون
فولاد سمانته به دلیل سختی سطح بالا و هسته نرم، ممکن است تحت شرایط تنش بسیار زیاد یا ضربههای ناگهانی دچار ترکخوردگی سطحی شود.
همچنین فولاد سمانته نیاز به عملیات حرارتی دقیق دارد و هرگونه اشتباه در کنترل دما و زمان کربوره کردن میتواند منجر به نقص در خواص مکانیکی شود.
کاربردهای اصلی فولاد سمانته
در ادامه، به بررسی ملموسترین و مهمترین کاربردهای این فولاد در صنایع مختلف، از خودروسازی و ماشینآلات سنگین گرفته تا تجهیزات تخصصی صنعتی، میپردازیم.
اکنون که با خواص فنی فولاد سمانته آشنا شدیم، بهتر میتوانیم درک کنیم که چرا این فولاد در صنایع کلیدی تا این حد پرکاربرد است. در واقع، هر قطعهای که نیاز دارد در سطح خارجی خود با سایش و فرسودگی مقابله کند و همزمان در برابر ضربهها و فشارهای دینامیکی از درون مقاوم باشد، یک کاندیدای اصلی برای ساخته شدن از فولاد سمانته است.
کاربرد فولاد سمانته در ساخت چرخدنده
چرخدندهها، به ویژه در گیربکسهای صنعتی و خودروها، به طور مداوم تحت دو نوع تنش شدید قرار دارند: سایش دائمی در محل تماس دندهها و ضربههای ناگهانی ناشی از تغییر گشتاور. فولاد سمانته به دلیل ساختار دوگانهاش، راهحلی ایدهآل برای این شرایط است. لایه سطحی بسیار سخت آن (Case-Hardened) مقاومت فوقالعادهای در برابر سایش و خوردگی ایجاد میکند و عمر قطعه را به شکل چشمگیری افزایش میدهد. همزمان، مغز نرم و چقرمه آن، انرژی ناشی از ضربهها را جذب کرده و از شکستن شکننده دندهها جلوگیری میکند.
نقش فولاد سمانته در افزایش عمر شافتها و محورها
شافتها و محورها به طور مداوم تحت بارهای خمشی و پیچشی پیچیدهای قرار دارند که آنها را مستعد خستگی (Fatigue) میکند. سطح یک شافت، نقطهی شروع ترکهای ناشی از خستگی است و همچنین در محل تماس با یاتاقانها دچار سایش میشود. استفاده از فولاد سمانته این مشکلات را به طور همزمان حل میکند. سطح سخت و صیقلی شافت، مقاومت به سایش و خستگی را به شدت افزایش میدهد، در حالی که هستهی چقرمهی آن، استحکام لازم برای تحمل گشتاور و نیروهای خمشی را بدون شکستن فراهم میکند. این ترکیب، عمر کاری شافت را تضمین کرده و قابلیت اطمینان آن را در سیستمهای دوار بالا میبرد.
کاربرد فولاد سمانته در قطعات کلیدی موتور
قطعاتی مانند میللنگ، میلبادامک و پین پیستون در موتور، در یکی از سختترین شرایط کاری ممکن فعالیت میکنند: ترکیبی از سرعت بالا، بارهای ضربهای شدید ناشی از احتراق، و سایش مداوم. فولاد سمانته برای این قطعات حیاتی، عملکردی بینظیر ارائه میدهد. سطح بسیار سخت میللنگ و پینها، مقاومت عالی در برابر سایش در یاتاقانها و محلهای تماس فراهم میکند. در عین حال، مغز چقرمه و مقاوم این قطعات، انرژی ضربات انفجار در سیلندر را جذب کرده و از شکست ناگهانی آنها تحت تنشهای پیچشی و خمشی شدید جلوگیری میکند.
چرا فولاد سمانته در ساخت یاتاقانها کاربرد دارد؟
اجزای غلتشی یاتاقانها، مانند رولرها و ساچمهها (Balls and Rollers)، تحت فشارهای تماسی بسیار بالا و سایش مداوم هستند. هرگونه تغییر شکل یا فرسایش در سطح این اجزا میتواند منجر به از کار افتادن کل یاتاقان شود. فولاد سمانته به دلیل سختی سطحی بسیار بالا، مقاومت فوقالعادهای در برابر این نوع سایش و تغییر شکل پلاستیک (Plastic Deformation) از خود نشان میدهد. سطح سخت و کاملاً صیقلی، حرکت روان و بدون اصطکاک را تضمین میکند، در حالی که مغز چقرمه، ضربات و بارهای شعاعی و محوری را تحمل کرده و از ترک خوردن این اجزای حیاتی جلوگیری میکند.
ساخت ابزارآلات و گیرههای دقیق با فولاد سمانته
فکهای گیرههای صنعتی و سه نظام دستگاههای تراش، همواره با قطعات کار سختشده در تماس هستند و باید بدون تغییر شکل یا سایش، آنها را محکم در جای خود نگه دارند. فولاد سمانته برای این نوع ابزارها ایدهآل است، زیرا سطح سختشدهی آن، لبههای تیز و سطوح گیرنده را در برابر فرسودگی و لهیدگی محافظت میکند و دقت ابزار را در بلندمدت حفظ مینماید. در عین حال، مغز چقرمهی این قطعات، نیروی عظیم فشاری ناشی از بستن گیره را تحمل کرده و از ترک خوردن بدنه اصلی ابزار جلوگیری به عمل میآورد.
نقش حیاتی فولاد سمانته در قطعات حساس هوافضا
در صنعت هوافضا، قابلیت اطمینان و مقاومت در برابر شکست (Failure) حرف اول را میزند. اگرچه در این صنعت از مواد سبکی مانند آلومینیوم و کامپوزیتها استفاده فراوانی میشود، اما برای قطعاتی که تحت تنشهای مکانیکی و خستگی فوقالعاده شدید قرار دارند، هیچ جایگزینی برای فولادهای آلیاژی با استحکام بالا وجود ندارد. فولاد سمانته در ساخت اجزای حیاتی مانند قطعات ارابه فرود (Landing Gear)، اتصالات بال و پایههای موتور به کار میرود. سطح بسیار سخت این قطعات، مقاومت بینظیری در برابر خستگی و سایش ایجاد میکند و مغز چقرمهی آن، ضامن عدم شکست قطعه در برابر بارهای ناگهانی و ضربات شدید، مانند هنگام فرود هواپیما، است.
افزایش دوام قطعات نوار نقاله با فولاد سمانته
سیستمهای نوار نقاله، به ویژه در صنایع معدنی و ساختمانی، دائماً با مواد ساینده و بارهای سنگین در تماس هستند. قطعاتی مانند رولیکها، چرخزنجیرها و پینهای زنجیر کانوایر، به شدت در معرض فرسایش قرار دارند. فولاد سمانته با فراهم کردن یک سطح سخت، لایهای محافظ در برابر سایش ناشی از حمل موادی مانند شن، ماسه و سنگ معدن ایجاد میکند. این ویژگی، نیاز به تعویض قطعات را کاهش داده و هزینههای نگهداری را به شکل چشمگیری پایین میآورد، در حالی که مغز مقاوم آن، استحکام لازم برای تحمل وزن بالای مواد و جلوگیری از شکستگی را تامین میکند.
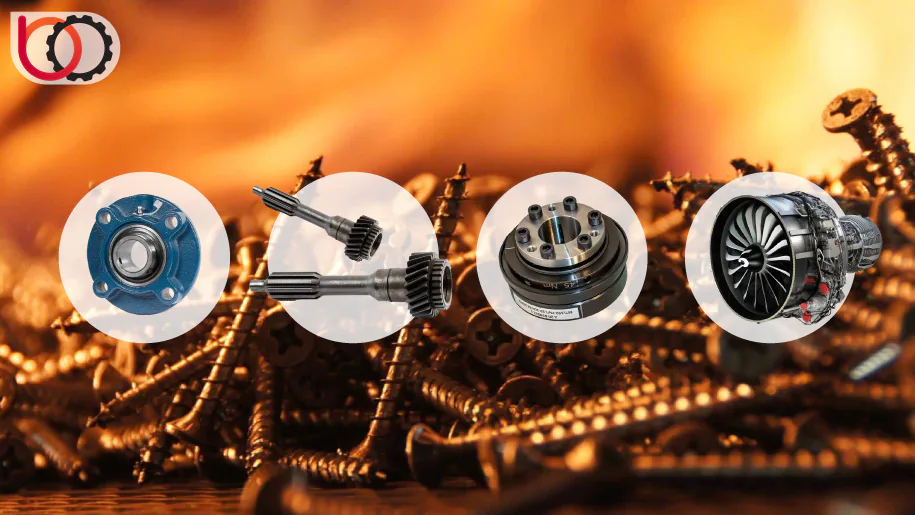
استاندارد و گریدهای فولاد سمانته (سمانتاسیون)
انواع، استانداردها و گریدهای معروف فولاد سمانتاسیون
انتخاب فولاد سمانته مناسب برای یک کاربرد صنعتی، نیازمند آشنایی با استانداردها و گریدهای مختلف آن است. این استانداردها که توسط سازمانهای بینالمللی مانند DIN (آلمان)، AISI (آمریکا) و EN (اروپا) تعریف میشوند، ترکیبات شیمیایی و خواص مکانیکی هر فولاد را تضمین میکنند. هر گرید، مانند یک شناسنامه، ویژگیهای منحصر به فردی دارد که آن را برای کاربرد خاصی مناسب میسازد. در ادامه، به بررسی تخصصی پرکاربردترین گرید یعنی 1.7131 و سپس سایر گریدهای مهم میپردازیم.
بررسی تخصصی گرید 1.7131 (16MnCr5)
فولاد 1.7131 که با نام 16MnCr5 نیز شناخته میشود، بدون شک یکی از پرکاربردترین و همهکارهترین فولادهای سمانته در صنایع مختلف است. شهرت این گرید به دلیل توازن عالی بین سختیپذیری سطحی و چقرمگی مغز، و همچنین قابلیت ماشینکاری خوب در حالت آنیل شده است.
ویژگیهای کلیدی:
- سختیپذیری عالی: پس از عملیات سمانتاسیون، به سختی سطحی بالایی (حدود 62 راکول C) دست مییابد.
- مقاومت به سایش بالا: برای قطعاتی که در تماس مداوم هستند، ایدهآل است.
- چقرمگی مغز مناسب: توانایی خوبی در تحمل بارهای ضربهای و دینامیکی دارد.
کاربردهای متداول: به دلیل همین ویژگیها، این گرید انتخاب اول برای ساخت انواع چرخدندههای صنعتی و خودرو، میلبادامک، پینهای پیستون و شافتهای تحت تنش متوسط است.
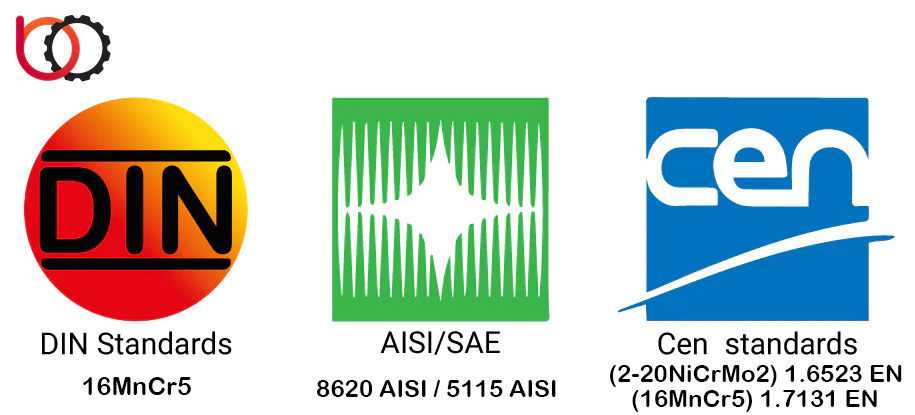
سایر گریدهای پرکاربرد
علاوه بر گرید 1.7131، گریدهای دیگری نیز بر اساس نیازهای خاصتر در صنعت مورد استفاده قرار میگیرند که برخی از مهمترین آنها عبارتند از:
- فولاد 20MnCr5 (گرید 1.7147): این گرید مقاومت به ضربه بهتری نسبت به 16MnCr5 دارد و در ساخت قطعات سنگینتر و بزرگتر که نیاز به چقرمگی هسته بالاتری دارند، استفاده میشود.
- فولاد AISI 8620: یکی از محبوبترین گریدهای سمانته در استاندارد آمریکایی است که ترکیبی از نیکل، کروم و مولیبدن دارد. این گرید به دلیل قابلیت اطمینان بالا و خواص متعادل، به طور گسترده در صنعت خودروسازی آمریکا استفاده میشود.
- فولاد EN 1.6523 (20NiCrMo2-2): به دلیل حضور نیکل و مولیبدن، دارای چقرمگی و استحکام هسته فوقالعادهای است و برای قطعات بسیار بزرگ و تحت تنشهای شدید مانند چرخدندههای توربینهای بادی و قطعات هوافضا کاربرد دارد.
فرآیند تولید و عملیات حرارتی فولاد سمانته
خواص دوگانه و برجسته فولاد سمانته، به صورت ذاتی در شمش اولیه وجود ندارد؛ بلکه حاصل یک فرآیند مهندسی دقیق و چندمرحلهای به نام عملیات حرارتی است. هدف از این فرآیند، ایجاد یک تغییر شیمیایی در سطح فولاد (افزایش درصد کربن) و سپس کنترل ساختار کریستالی آن از طریق سرد کردن و حرارتدهی مجدد است.
مهمترین و پایهایترین مرحله در این فرآیند، عملیات کربوره کردن (Carburizing) است که در آن، سطح فولاد با کربن غنی میشود. پس از آن، مراحل تکمیلی مانند کوئنچ (Quenching) و تمپر (Tempering) برای رسیدن به سختی نهایی در سطح و چقرمگی مطلوب در مغز قطعه، اجرا میشوند.
عملیات کربوره کردن (Carburizing) چیست؟
کربوره کردن یا سمانتاسیون، قلب فرآیند ساخت فولاد سمانته است. این عملیات حرارتی-شیمیایی با یک هدف اصلی انجام میشود: افزایش درصد کربن در لایههای سطحی قطعه فولادی، در حالی که ترکیب شیمیایی مغز آن دستنخورده باقی بماند. برای این کار، قطعه در دمای بالا (معمولاً بین ۸۷۰ تا ۹۳۰ درجه سانتیگراد) و در یک محیط سرشار از کربن (مانند گازهای کربندار یا پودر زغال) قرار میگیرد. در این شرایط، اتمهای کربن به آرامی به سطح فلز نفوذ کرده و یک لایه سخت و مقاوم به سایش به نام «Case» ایجاد میکنند. عمق این لایه که به عواملی مانند زمان و دما بستگی دارد، معمولاً بین ۰.۵ تا ۲ میلیمتر است.
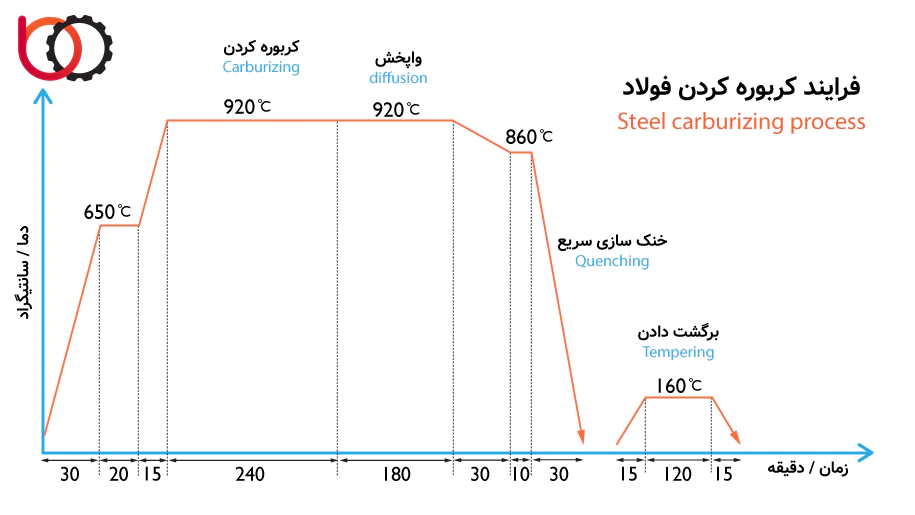
انواع روشهای کربوره کردن
کربوره کردن بسته به تجهیزات و دقت مورد نیاز، به روشهای مختلفی انجام میشود:
- کربوره کردن گازی (Gas Carburizing): رایجترین و دقیقترین روش صنعتی است.
- کربوره کردن جامد (Pack Carburizing): روشی سنتیتر با قرار دادن قطعه در پودر زغال.
- کربوره کردن مایع (Liquid Carburizing): با غوطهور کردن قطعه در حمام نمک مذاب.
- روشهای مدرن: روشهای دقیقتری مانند خلاء و پلاسما برای کاربردهای حساس وجود دارد.
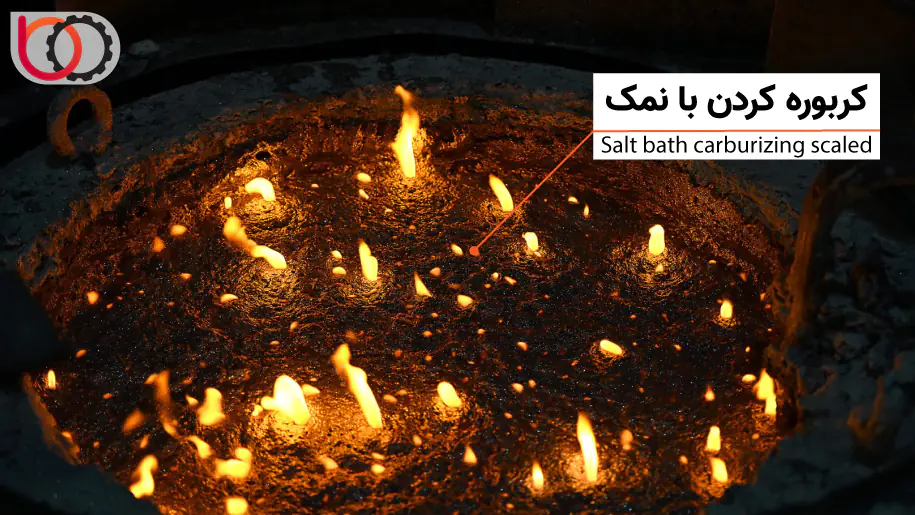
مراحل تکمیلی پس از کربوره کردن
۱. کوئنچ کردن (Quenching): بلافاصله پس از کربوره کردن، قطعه به سرعت در روغن سرد میشود تا لایه سطحی آن سخت شود.
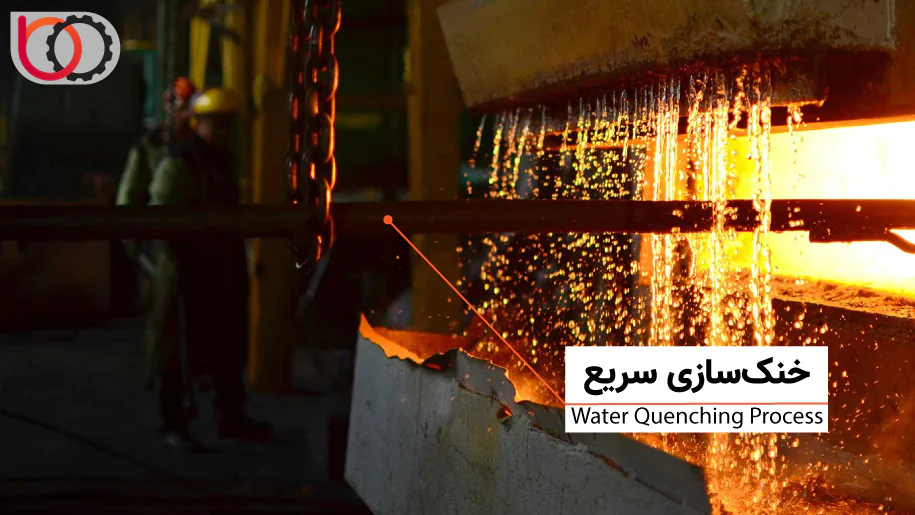
۲. برگشت دادن (Tempering): سپس قطعه دوباره در دمای پایین حرارت میبیند تا شکنندگی آن از بین برود و چقرمگی آن افزایش یابد.
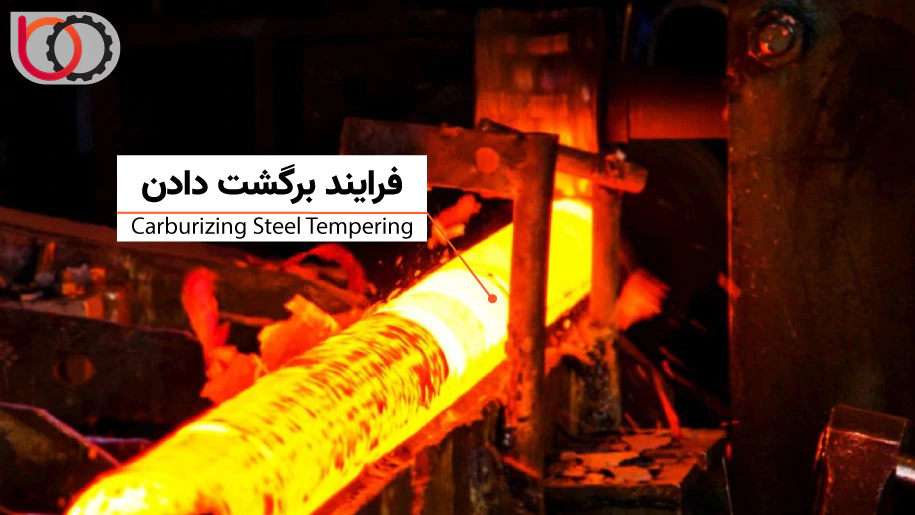
آزمایشهای سختیسنجی فولاد سمانته
برای سنجش سختی فولاد سمانته بهعنوان یکی از مراحل اصلی کنترل کیفیت این فولاد، آزمایشهای سختیسنجی با دقت و جزئیات بسیار زیادی انجام میشوند. فولاد سمانته به دلیل عملیات کربوره کردن، دارای لایه سطحی بسیار سخت و مغزی نرمتر است. این ویژگی باعث میشود که سختیسنجی این فولاد نیازمند تکنیکهای دقیق و متناسب با ساختار لایهای آن باشد. در ادامه، آزمونهای تخصصی و روشهای خاصی که برای فولاد سمانته بهکار میروند، عبارتند از:
1. آزمون سختی سطحی راکول (Rockwell Superficial Hardness Test)
- روش آزمون: آزمون سختی سطحی راکول برای فولاد سمانته با استفاده از مقیاسهای A و C انجام میشود. از یک فروکننده الماسی به شکل مخروطی استفاده میشود که تحت باری کمتر از آزمون راکول معمولی بر سطح فولاد فشار وارد میکند.
- اهمیت برای فولاد سمانته: این آزمون به دلیل حساسیت بالای خود به تغییرات کوچک در سختی سطحی، برای سنجش سختی لایه کربوره شده بسیار مناسب است. با توجه به اینکه ضخامت لایه کربوره شده معمولاً در حد میلیمتر است، این آزمون میتواند جزئیات سختی سطح را با دقت بالا اندازهگیری کند.
- معیارهای سختی: برای فولادهای سمانتهشده، معمولاً سختی سطحی باید در محدوده 55 تا 62 HRC باشد که بستگی به شرایط عملیات حرارتی و عمق کربوره کردن دارد.
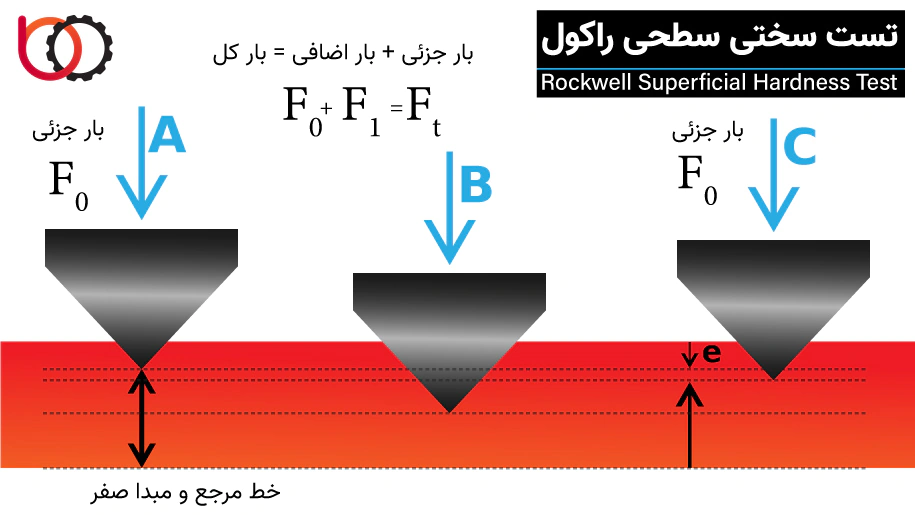
2. آزمون سختی پروفیل سطحی و عمقی ویکرز (Vickers Depth Profiling Hardness Test)
- روش آزمون: در این آزمون از فروکننده هرمیشکل الماسی استفاده میشود که به صورت تدریجی نیرویی مشخص را به سطح فولاد وارد میکند. سپس از روی ابعاد اثر فرو رفتگی ایجاد شده، سختی محاسبه میشود. اما در آزمون پروفیل سطحی و عمقی، سختی در نقاط مختلف عمق لایه کربوره شده به دقت بررسی میشود.
- اهمیت برای فولاد سمانته: با توجه به اینکه فولاد سمانته دارای سختی متغیری از سطح تا عمق لایه کربوره شده است، این آزمون میتواند پروفیل تغییرات سختی را در لایه سطحی به دقت نشان دهد. این پروفیل نشاندهنده کیفیت عملیات کربوره کردن و همچنین میزان نفوذ کربن در سطح فولاد است.
- عمق سختیسنجی: معمولاً عمق لایه کربوره شده برای فولاد سمانته بین 0.5 تا 2 میلیمتر است. در آزمون پروفیل ویکرز، نقاط سختیسنجی در فواصل بسیار کوچک از سطح به عمق اندازهگیری میشوند تا تغییرات دقیق سختی مشخص شود.
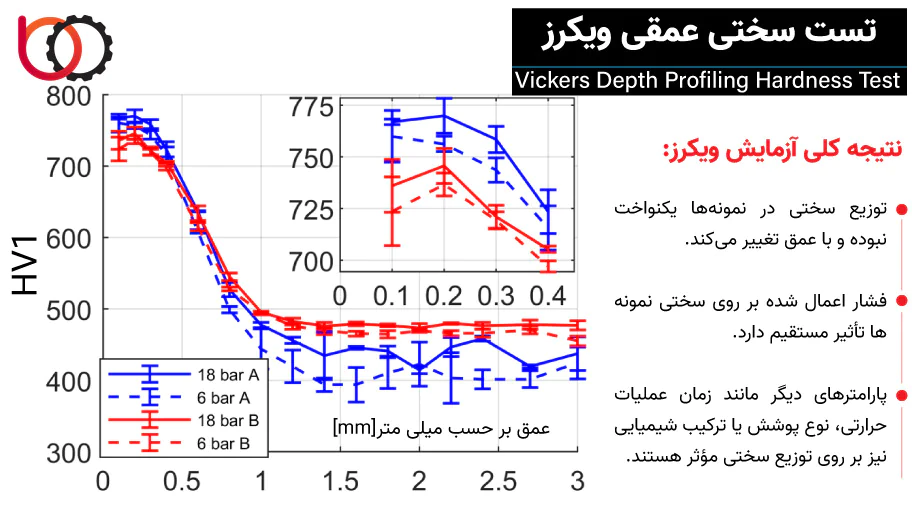
3. آزمون سختی میکرو ویکرز (Micro-Vickers Hardness Test)
- روش آزمون: این آزمون با استفاده از فروکننده الماسی بسیار کوچک و نیرویی کمتر از آزمون ویکرز معمولی انجام میشود. این آزمون برای سنجش سختی لایههای سطحی بسیار نازک و تغییرات جزئی در ساختار کریستالی سطح فولاد سمانته کاربرد دارد.
- اهمیت برای فولاد سمانته: فولاد سمانته دارای تغییرات ریزساختاری قابل توجهی در لایههای نازک سطحی است که توسط آزمونهای معمول قابل شناسایی نیست. آزمون میکرو ویکرز میتواند به دقت سختی را در لایههای مختلف نازک سطحی و عمق کمتر از 1 میلیمتر مشخص کند، که برای کنترل کیفیت فولاد سمانته حیاتی است.
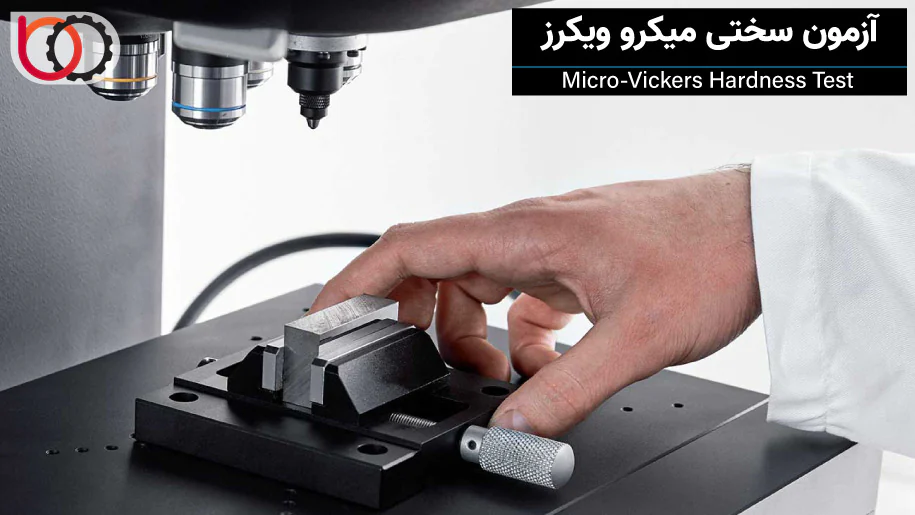
4. آزمون سختی کنوپ (Knoop Hardness Test)
- روش آزمون: آزمون کنوپ شبیه به آزمون ویکرز است، با این تفاوت که از فروکنندهای با شکل غیرمتقارن استفاده میکند. این آزمون بهطور ویژه برای اندازهگیری سختی لایههای نازک و مناطق ریزساختاری بهکار میرود.
- اهمیت برای فولاد سمانته: به دلیل ساختار لایهای فولاد سمانته، آزمون کنوپ میتواند سختی در لایههای نزدیک به سطح و ریزساختارهای کوچکی که در اثر کربوره کردن ایجاد شدهاند را با دقت بیشتری اندازهگیری کند.
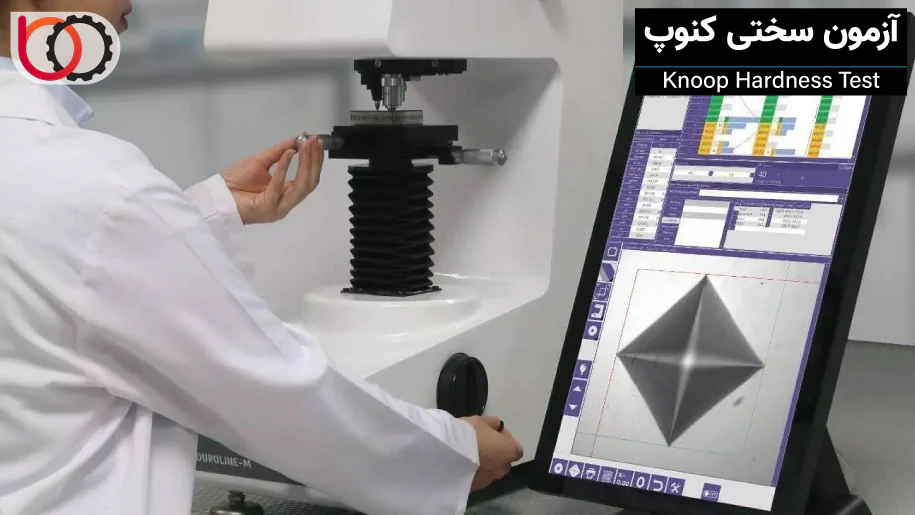
5. آزمون عمق سختی کربوره شده (Case Depth Hardness Test)
- روش آزمون: در این آزمون، سختی در مقاطع مختلف عمق لایه کربوره شده اندازهگیری میشود تا مشخص شود که آیا عملیات کربوره کردن به درستی تا عمق مورد نظر نفوذ کرده است یا خیر. معمولاً این آزمون با ترکیب روشهای ویکرز و راکول انجام میشود.
- اهمیت برای فولاد سمانته: این آزمون بهطور خاص برای فولادهای سمانتهشده طراحی شده و میتواند تضمین کند که لایه کربوره شده به اندازه کافی عمیق و سخت است. همچنین این آزمون نشاندهنده کیفیت و یکنواختی عملیات حرارتی است.
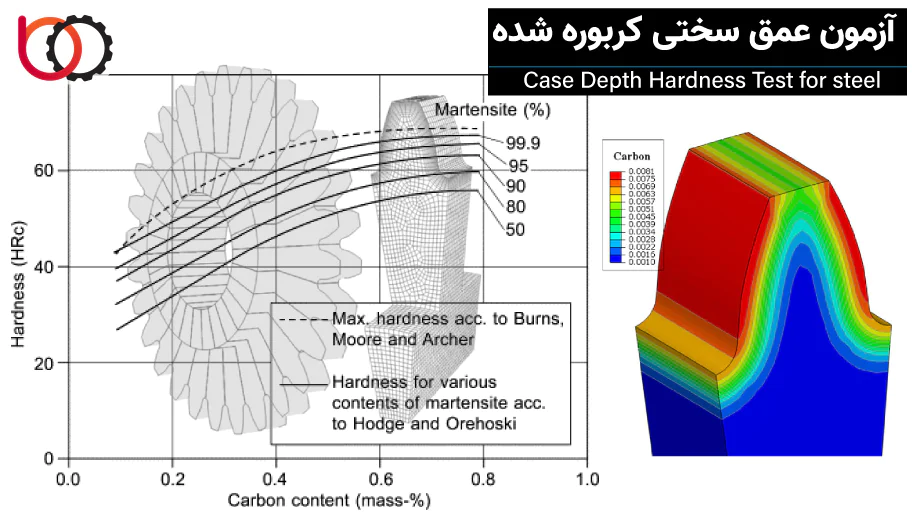
6. سختیسنجی با استفاده از تجهیزات پرتابل (Portable Hardness Testing)
- روش آزمون: این نوع سختیسنجی با دستگاههای پرتابل انجام میشود که امکان سختیسنجی در شرایط عملیاتی و روی قطعات بزرگ را فراهم میکند. دستگاههایی مانند Leeb و UCI (Ultrasonic Contact Impedance) برای این منظور بهکار میروند.
- اهمیت برای فولاد سمانته: این تجهیزات برای کنترل کیفیت سریع قطعات تولید شده از فولاد سمانته در خطوط تولید و در محل کاربردهای صنعتی بسیار مناسب هستند. اگرچه دقت این آزمونها معمولاً کمتر از آزمونهای آزمایشگاهی است، اما میتواند برای بررسیهای اولیه و میدانی بهکار رود.
آزمونهای غیر مخرب (NDT) فولاد سمانته
آزمونهای غیرمخرب (NDT) برای فولاد سمانته به دلیل ویژگیهای خاص این فولاد که حاصل فرآیند کربوره کردن است، به شیوههای پیشرفته و دقیقتری انجام میشود. فولاد سمانته دارای لایه سطحی بسیار سخت و مغزی نرمتر است که این لایه سطحی نه تنها باید عاری از ترک و نقص باشد، بلکه یکپارچگی آن برای کاربردهای مهندسی با بارگذاری شدید بسیار حائز اهمیت است. در ادامه، به بررسی تخصصیتر آزمونهای غیرمخرب که بهطور خاص برای ارزیابی لایه کربوره شده و یکپارچگی ساختاری فولاد سمانته استفاده میشوند، میپردازیم:
1. آزمون نفوذ مایعات (Liquid Penetrant Testing – LPT) برای لایههای کربورهشده
- روش و جزئیات: در این روش از مایعات نافذ با فرمولاسیون خاصی استفاده میشود که به دلیل دقت بیشتر برای شناسایی ترکهای سطحی ریز در لایه کربوره شده فولاد سمانته به کار میرود. ترکهای سطحی ممکن است به دلیل تنشهای حرارتی و عملیات حرارتی غیردقیق در حین فرآیند کربوره کردن به وجود آمده باشند.
- اهمیت خاص در فولاد سمانته: ترکهای سطحی در لایه کربورهشده ممکن است منجر به ایجاد تمرکز تنش و کاهش عمر خستگی قطعه شود. در فولاد سمانته، تشخیص دقیق این ترکها در لایه سطحی بسیار حیاتی است، چرا که این لایه مسئول اصلی تحمل بارهای سطحی و مقاومت به سایش است.
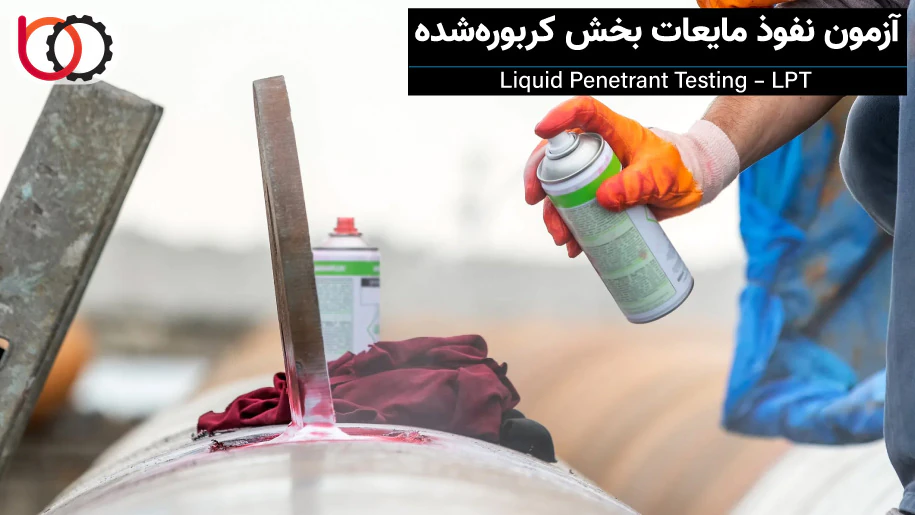
2. آزمون ذرات مغناطیسی (Magnetic Particle Testing – MPT) در لایههای کربوره شده
- روش و جزئیات: در فولاد سمانته که سطح آن سخت و مغناطیسی است، آزمون ذرات مغناطیسی به شکل پیشرفتهای انجام میشود. ایجاد میدان مغناطیسی دقیق به همراه استفاده از ذرات مغناطیسی ریز، عیوب سطحی و زیر سطحی کوچک در لایه کربوره شده را شناسایی میکند.
- نکات تخصصی: فولاد سمانته به دلیل عملیات کربوره کردن ممکن است دچار ترکهای میکروسکوپی یا ناپیوستگیهای سطحی شود که با روشهای متداول قابل شناسایی نیستند. آزمون MPT میتواند با دقت بالایی ترکها و ناپیوستگیهای زیر سطحی نزدیک به سطح را که در اثر کربوره کردن ایجاد شدهاند، شناسایی کند.
- کاربرد تخصصی: این آزمون بهویژه در قطعاتی که پس از کربوره کردن در شرایط بارگذاری خستگی قرار میگیرند، بسیار اهمیت دارد. تشخیص این عیوب برای جلوگیری از شکست خستگی ضروری است.
3. آزمون التراسونیک (Ultrasonic Testing – UT) با فرکانس بالا برای فولاد سمانته
- روش و جزئیات: برای بررسی ساختار داخلی فولاد سمانته از امواج التراسونیک با فرکانسهای بالا استفاده میشود تا حتی کوچکترین تغییرات در ساختار کریستالی و ناپیوستگیهای داخلی تشخیص داده شوند. این روش قابلیت شناسایی عیوب داخلی و حتی ترکهای زیر سطحی کوچک را فراهم میکند.
- نکات تخصصی: به دلیل وجود تنشهای حرارتی در فرآیند کربوره کردن، عیوبی مانند ترکهای ریز داخلی ممکن است در فولاد سمانته ایجاد شوند. استفاده از امواج التراسونیک با فرکانس بالا به همراه آنالیز دقیق بازتابهای امواج، امکان تشخیص ترکهای زیر سطحی و حتی نقصهای درونی را فراهم میکند.
- کاربرد تخصصی: این روش برای ارزیابی کیفیت عملیات کربوره کردن و اطمینان از عدم وجود ترکهای داخلی یا ناپیوستگیهای ریز که ممکن است باعث کاهش عمر خستگی و شکستهای ناگهانی شوند، بسیار کاربرد دارد.
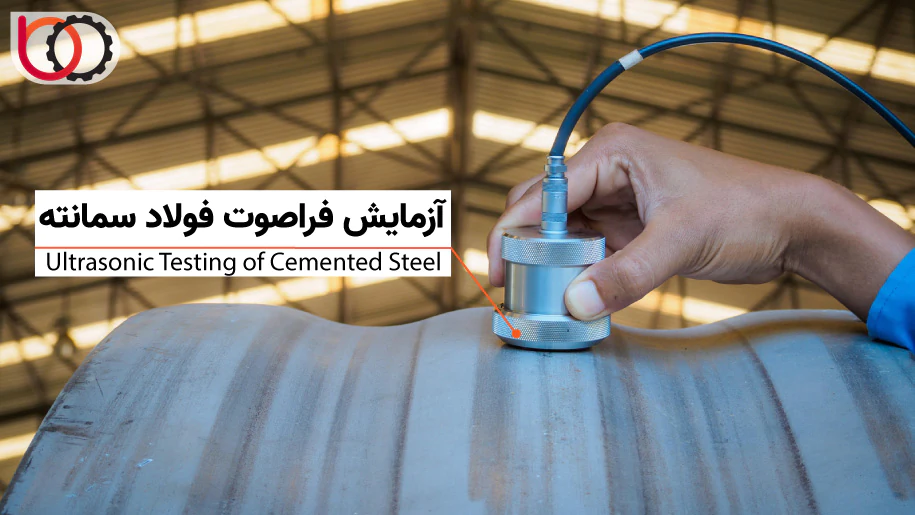
4. آزمون جریان گردابی (Eddy Current Testing – ECT) پیشرفته
- روش و جزئیات: در این روش از کویلهای جریان گردابی با تنظیمات حساس و چند کاناله استفاده میشود تا لایه کربورهشده و تغییرات سختی سطحی فولاد سمانته بهطور دقیق شناسایی شود. این روش امکان بررسی پروفیل سختی سطحی فولاد سمانته را فراهم میکند.
- نکات تخصصی: فولاد سمانته به دلیل ساختار لایهای خود، پروفیل سختی غیر یکنواختی دارد که باید به دقت بررسی شود. آزمون جریان گردابی پیشرفته با تنظیمات دقیق قادر به تشخیص تغییرات جزئی در خواص سطحی و عمق لایه کربورهشده است. همچنین این روش میتواند ترکها و عیوب سطحی نزدیک به سطح را شناسایی کند.
- کاربرد تخصصی: این آزمون بهویژه برای کنترل کیفیت فولاد سمانته پس از عملیات حرارتی و کربوره کردن بسیار مفید است و میتواند به شناسایی عیوب ریز و تغییرات غیر طبیعی در لایه کربوره شده کمک کند.
5. آزمون پرتونگاری (Radiographic Testing – RT) با وضوح بالا
- روش و جزئیات: پرتونگاری با استفاده از پرتوهای ایکس با وضوح بالا برای شناسایی نقصهای داخلی در فولاد سمانته انجام میشود. به دلیل عملیات حرارتی و تغییرات ساختاری در فرآیند کربوره کردن، فولاد سمانته ممکن است دارای نقصهای داخلی باشد که تنها با این روش قابل شناسایی است.
- نکات تخصصی: در فولاد سمانته، پرتونگاری ایکس میتواند با دقت بالا عیوب داخلی نظیر ترکهای ناشی از تنشهای حرارتی، حفرههای گازی و ناپیوستگیهای داخلی را شناسایی کند. این روش به دلیل توانایی در نمایش دقیق عیوب داخلی در فولادهای با ساختار پیچیده، کاربرد ویژهای در کنترل کیفیت این نوع فولاد دارد.
- کاربرد تخصصی: پرتونگاری بهویژه برای بررسی قطعات پیچیدهای که در معرض بارگذاری بالا هستند و عدم وجود عیوب داخلی در آنها بسیار حیاتی است، اهمیت دارد.
6. آزمون نشت شار مغناطیسی (Magnetic Flux Leakage – MFL) برای شناسایی ناپیوستگیهای زیر سطحی
- روش و جزئیات: این روش با استفاده از میدان مغناطیسی و تشخیص نشت شار در نقاطی که دارای ناپیوستگیهای زیر سطحی هستند، عیوبی مانند ترکهای ریز و حفرههای داخلی را شناسایی میکند.
- نکات تخصصی: در فولاد سمانته که تغییرات مغناطیسی و مکانیکی در لایههای مختلف رخ میدهد، این آزمون میتواند ناپیوستگیهای ریز در لایههای کربورهشده را با دقت بالا شناسایی کند. نشت شار مغناطیسی در نقاطی که تغییرات ساختاری و مکانیکی غیر یکنواخت وجود دارند، تشخیص داده شده و آنالیز میشود.
- کاربرد تخصصی: این آزمون برای ارزیابی قطعاتی که نیاز به تحمل بارهای مکانیکی سنگین دارند و عدم وجود ترکهای ریز و عیوب زیر سطحی برای آنها حیاتی است، استفاده میشود.