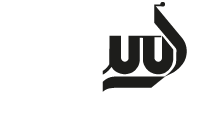
ولکانیزاسیون
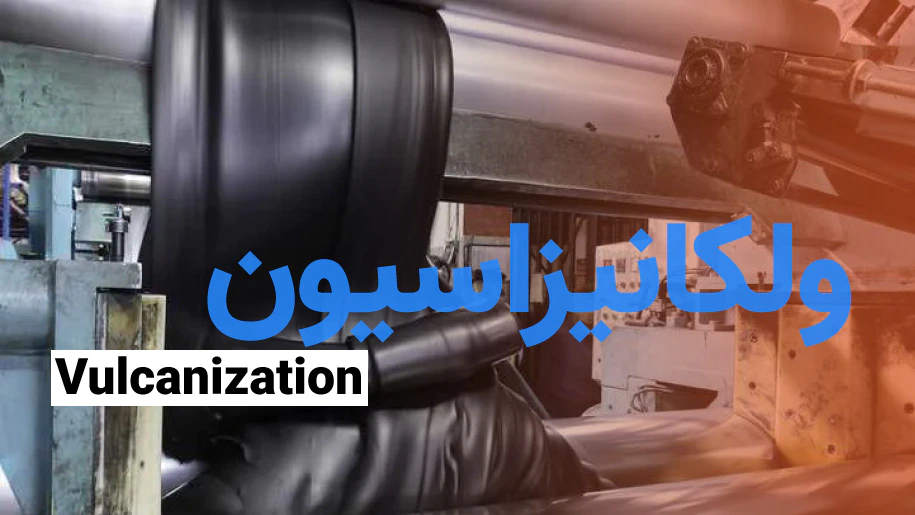
امروزه در صنعت برای رسیدن به نتایج مطلوب و بهینهسازی ویژگیهای مواد، از فرآیندهای مختلفی استفاده میشود. در صنعت پلیمرها و لاستیکها، یکی از این فرآیندهای کلیدی، ولکانیزاسیون است. این فرآیند شیمیایی به تولیدکنندگان امکان میدهد تا با افزایش استحکام، انعطافپذیری و مقاومت در برابر عوامل محیطی، محصولات بهتری تولید کنند. ولکانیزاسیون نقش بسزایی در بهبود کیفیت لاستیکها و پلیمرها دارد و در کاربردهای متنوعی از جمله صنعت خودرو، پزشکی و ساختمان استفاده میشود.
ولکانیزاسیون یا پخت کردن چیست؟
ولکانیزاسیون یا به اصطلاح پخت کردن، فرآیند شیمیایی است که طی آن لاستیک طبیعی یا مصنوعی از طریق افزودن گوگرد و حرارتدهی به آن، به ساختاری سهبعدی تبدیل میشود. این فرآیند باعث تشکیل پیوندهای عرضی (cross-links) بین زنجیرههای پلیمری میشود که به تقویت خواص مکانیکی لاستیک، مانند استحکام کششی، سختی، و مقاومت در برابر سایش و حرارت منجر میگردد. همچنین، ولکانیزاسیون موجب کاهش خاصیت چسبندگی و افزایش پایداری در برابر تخریب اکسیداتیو و محیطی میشود. بهعلاوه، این فرآیند زمان استفاده و عمر مفید محصولات لاستیکی را بهطور قابل توجهی افزایش میدهد. بههمیندلیل، ولکانیزاسیون در تولید انواع محصولات لاستیکی، از جمله نوارهای لاستیکی، تایر و قطعات خودرو، کاربردهای گستردهای دارد و نقش کلیدی در صنعت لاستیکسازی ایفا میکند.
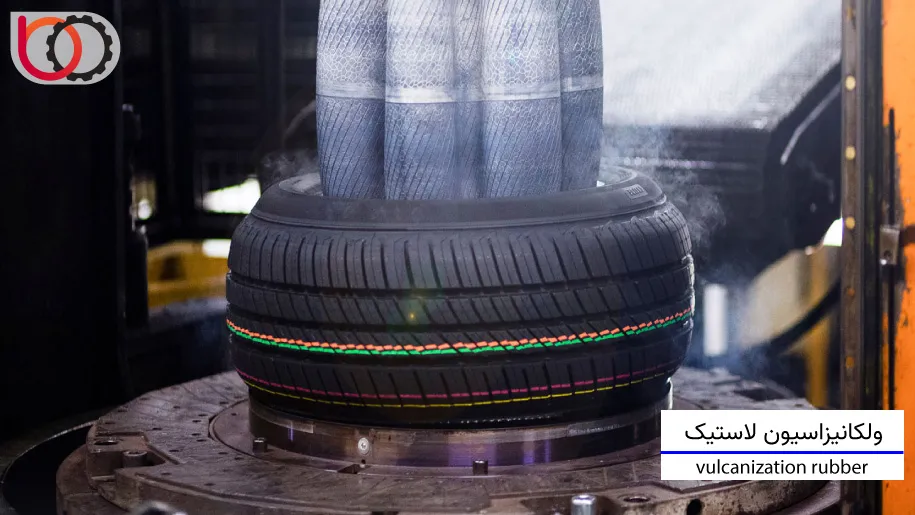
تاریخچه ولکانیزاسیون
تاریخچه ولکانیزاسیون به اوایل قرن نوزدهم و زمانی که چارلز گودیر (Charles Goodyear) این فرآیند را کشف کرد، برمیگردد. در سال 1839، گودیر بهطور تصادفی متوجه شد که ترکیب لاستیک طبیعی با گوگرد و حرارت دادن آن، لاستیک را از یک ماده چسبناک و ناپایدار به یک ماده محکم، انعطافپذیر و مقاوم تبدیل میکند. این کشف، انقلابی در صنعت لاستیک ایجاد کرد و زمینهساز تولید انبوه محصولات لاستیکی شد.
پیش از این کشف، لاستیک طبیعی به دلیل خواص ناپایدارش، در سرما سخت و در گرما چسبناک میشد. با فرآیند ولکانیزاسیون، لاستیک به مادهای با دوام، مقاوم در برابر حرارت و انعطافپذیر تبدیل شد که قابلیت استفاده در صنایع مختلف را فراهم کرد. همچنین این فناوری باعث تحول بزرگی در صنایع مختلف شد و نقش اساسی در توسعه حملونقل و تولیدات صنعتی ایفا کرد.
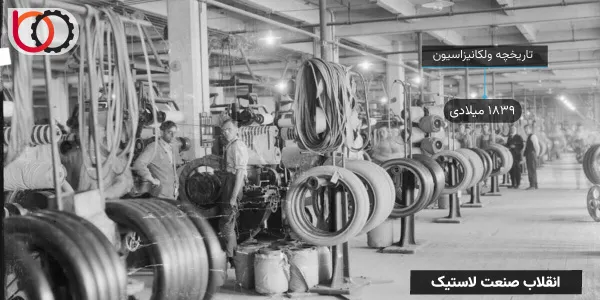
انواع ولکانیزاسیون یا پخت
ولکانیزاسیون را میتوان به انواع مختلفی دستهبندی کرد که هر یک بسته به شرایط عملیاتی و خواص نهایی مورد نیاز از الاستومرها، از مکانیزمهای متفاوتی برای ایجاد پیوندهای عرضی بهره میگیرند:
ولکانیزاسیون با گوگرد
این فرآیند معمولترین و پرکاربردترین روش ولکانیزاسیون است. در این روش، گوگرد بهعنوان عامل پخت در حضور شتابدهندهها و فعالکنندهها به کار میرود. پیوندهای عرضی دیسولفیدی یا پلیسولفیدی بین زنجیرههای پلیمری تشکیل میشود که باعث بهبود خواص مکانیکی مانند انعطافپذیری و مقاومت سایشی لاستیک میگردد. این روش عمدتاً برای لاستیکهای طبیعی (NR) و برخی لاستیکهای مصنوعی مثل استایرن-بوتادین (SBR) بهکار میرود.
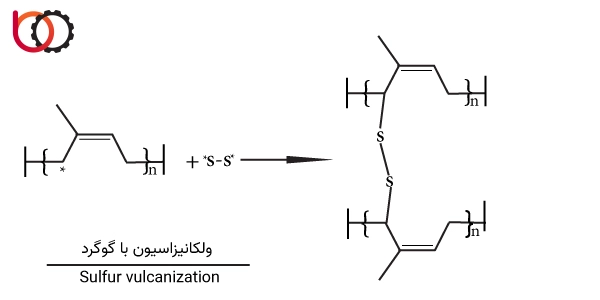
ولکانیزاسیون پراکسیدی
در این فرآیند، از پراکسیدهای آلی بهعنوان عامل پخت استفاده میشود. مکانیزم این روش، ایجاد پیوندهای کربن-کربن در ساختار زنجیرههای پلیمری است. لاستیکهای حاصل از این روش معمولاً مقاومت حرارتی و پایداری شیمیایی بالاتری نسبت به ولکانیزاسیون گوگردی دارند. این روش برای الاستومرهایی چون EPDM و سیلیکونها (VMQ) مناسب است.
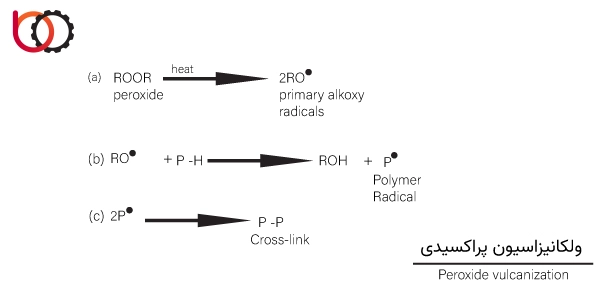
ولکانیزاسیون با اشعه
در این روش، از تابشهای یونیزان نظیر الکترونهای پرانرژی یا پرتوهای گاما برای ایجاد پیوندهای عرضی استفاده میشود. ولکانیزاسیون اشعه بدون نیاز به مواد شیمیایی انجام میشود و مزیتهای آن شامل کنترل دقیقتر فرآیند و کاهش انتشار ترکیبات فرار است. این روش برای کاربردهای تخصصی مثل صنایع الکترونیک یا پزشکی که نیاز به استرلیزاسیون است، بهکار میرود.
ولکانیزاسیون با رزین
در این نوع فرآیند از رزینهای فنولیک برای ایجاد پیوندهای عرضی استفاده میشود. این روش بهخصوص در تولید لاستیکهای سخت و مقاوم به دماهای بالا و محیطهای خورنده کاربرد دارد. لاستیکهای ولکانیزه شده با رزین در صنایعی چون خودروسازی و تولید محصولات صنعتی استفاده میشوند.
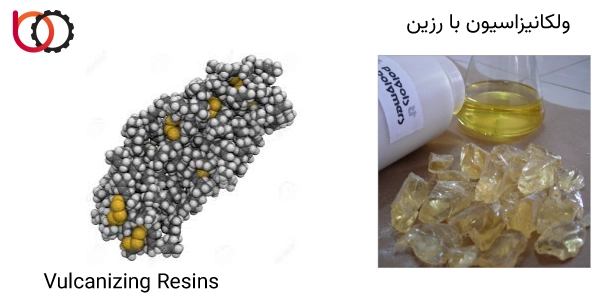
ولکانیزاسیون پلیسولفیدی
در این فرآیند، از پلیسولفیدها به عنوان عامل پخت استفاده میشود. این نوع ولکانیزاسیون مقاومت بسیار بالایی در برابر مواد شیمیایی و نفوذ آب به لاستیک میدهد و معمولاً در تولید محصولات آببندی، مانند درزگیرهای ساختمانی و هواپیما، کاربرد دارد.
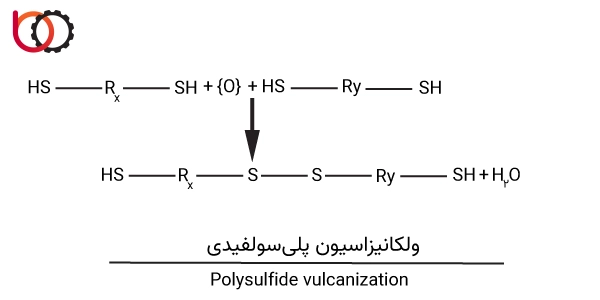
ارتباط ولکانیزاسیون با آپارات تسمه نقاله لاستیکی در فرآیند آپارات گرم
در فرآیند آپارات گرم، ولکانیزاسیون نقشی کلیدی در اتصال و ترمیم تسمه نقالههای لاستیکی دارد. این فرآیند شامل اعمال فشار و گرما به لاستیک است که به کمک دستگاه آپارات گرم لاستیک انجام میشود. ولکانیزاسیون باعث بهبود خواص مکانیکی و شیمیایی لاستیک شده و پیوندهای مولکولی قویتری را ایجاد میکند. در نتیجه، تسمه نقاله لاستیکی پس از آپارات گرم مقاومت بیشتری در برابر سایش، کشش و شرایط سخت محیطی پیدا میکند، که در صنایع سنگین مانند معدن و حملونقل مواد اهمیت ویژهای دارد.
در ولکانیزاسیون چه موادی مورد استفاده قرار میگیرد؟
در فرآیند ولکانیزاسیون، انتخاب دقیق مواد اولیه بهمنظور دستیابی به خواص مکانیکی، حرارتی و شیمیایی مطلوب در لاستیکها و الاستومرها، امری ضروری است. این مواد به طور ویژه طراحی شدهاند تا ساختار پلیمری را تقویت کرده و عملکرد نهایی محصول را در کاربردهای صنعتی و تخصصی بهبود بخشند.
- لاستیک طبیعی و مصنوعی:
لاستیک طبیعی از صمغ درخت Hevea brasiliensis بهدست میآید، درحالیکه لاستیک مصنوعی از پلیمرهای سنتزی مانند بوتادین یا استایرن-بوتادین تولید میشود. - گوگرد:
ماده کلیدی در فرآیند ولکانیزاسیون است که با پیوند عرضی بین زنجیرههای پلیمر، ساختار لاستیک را تقویت میکند و باعث افزایش استحکام و پایداری حرارتی آن میشود. - شتابدهندهها:
برای افزایش سرعت واکنش ولکانیزاسیون استفاده میشوند. این ترکیبات، مانند سولفنامیدها یا تیازولها، زمان فرآیند را کاهش میدهند و کارایی پخت را افزایش میدهند. - فعالکنندهها:
موادی مانند اکسید روی (ZnO) و اسید استئاریک که به تسهیل فرآیند پخت و افزایش سرعت واکنش کمک میکنند. - پرکنندهها:
برای بهبود خواص مکانیکی، مانند استحکام کششی و مقاومت سایشی، از موادی مانند دوده (Carbon Black) و سیلیکاتها استفاده میشود. این مواد همچنین به بهبود چسبندگی و دوام لاستیک کمک میکنند. - نرمکنندهها:
این ترکیبات مانند روغنهای معدنی و فسفاتها، انعطافپذیری لاستیک را افزایش داده و فرآیند پردازش را آسانتر میکنند. - آنتیاکسیدانها و آنتیاوزونانتها:
برای محافظت از لاستیک در برابر تخریب ناشی از تماس با اکسیژن و اوزون، این مواد اضافه میشوند. آنها از فرایندهای اکسیداسیونی که منجر به کاهش عمر لاستیک میشوند، جلوگیری میکنند.
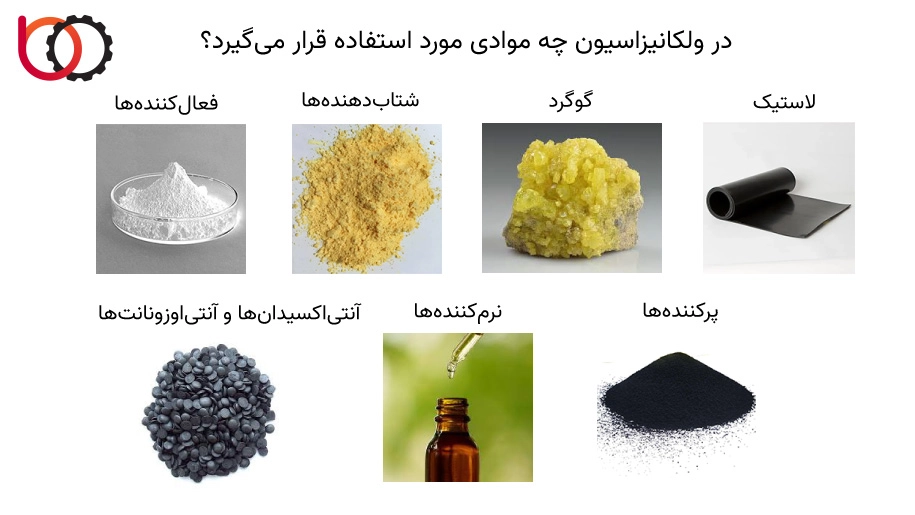
آموزش و بررسی گام به گام فرایند ولکانیزاسیون
فرآیند ولکانیزاسیون در صنعت لاستیک و پلیمرها به عنوان یکی از مراحل کلیدی در تولید برخی مواد شناخته میشود. این فرآیند نهتنها تأثیر عمیقی بر خواص مکانیکی و شیمیایی محصولات نهایی دارد، بلکه میتواند به بهبود عملکرد آنها در شرایط مختلف نیز کمک کند. در ادامه، گام به گام به بررسی جزئیات این فرآیند و مراحل مختلف آن خواهیم پرداخت تا درک بهتری از نقش ولکانیزاسیون در توسعه و تولید لاستیکها و دیگر پلیمرها به دست آوریم.
مراحل و مکانیزم ولکانیزاسیون
- افزودن گوگرد و تسریعکنندهها: در ابتدا، گوگرد به لاستیک طبیعی یا مصنوعی افزوده میشود. این افزودنیها معمولاً شامل تسریعکنندههای شیمیایی مانند دینیتروتولوئن و دیمتیل دیسولفید هستند که فرآیند واکنش را تسریع میکنند.
- حرارتدهی: مخلوط لاستیک و گوگرد در دماهای کنترلشده (معمولاً بین 140 تا 180 درجه سانتیگراد) حرارت داده میشود. این حرارت موجب افزایش انرژی حرارتی مولکولها شده و سبب شکسته شدن پیوندهای موجود در زنجیرههای پلیمری میگردد.
- تشکیل پیوندهای عرضی: با شروع واکنش ولکانیزاسیون، پیوندهای عرضی از طریق واکنش گوگرد با زنجیرههای پلیمری شکل میگیرد. این پیوندها ساختار لاستیک را به یک شبکه سهبعدی تبدیل میکند که به آن ویژگیهای خاصی از جمله استحکام، انعطافپذیری و مقاومت در برابر سایش و حرارت میدهد.
- خنکسازی و قالبدهی: پس از ولکانیزاسیون، لاستیک به سرعت خنک شده و به شکل نهایی خود قالبگیری میشود. این مرحله به ایجاد شکل نهایی و خصوصیات فیزیکی مطلوب کمک میکند.
اثرات ولکانیزاسیون بر خواص لاستیک
- افزایش استحکام: ولکانیزاسیون موجب افزایش مقاومت مکانیکی لاستیک میشود که در نتیجه عملکرد بهتری در شرایط تنش بالا دارد.
- انعطافپذیری و کشش: شبکهای شدن ساختار لاستیک، انعطافپذیری آن را حفظ کرده و امکان کشش و فرمدهی به آن را فراهم میآورد.
- مقاومت در برابر سایش: لاستیکهای ولکانیزه به دلیل ساختار متراکمتر و پیوندهای قویتر، در برابر سایش و پارگی مقاومتر هستند.
- پایداری حرارتی و شیمیایی: ولکانیزاسیون باعث افزایش پایداری لاستیک در دماهای بالا و در برابر مواد شیمیایی میشود، که این ویژگی به کاربردهای صنعتی مانند تسمه نوار نقالهها کمک میکند.
مهمترین پلیمرها و الاستومرهای تحت فرآیند ولکانیزاسیون
مواد مختلفی تحت فرآیند ولکانیزاسیون قرار میگیرند تا خواص فیزیکی و مکانیکی آنها بهبود یابد. در این فرآیند، موادی همچون لاستیک طبیعی، پلیکلروپرن، سیلیکون و بسیاری از الاستومرهای دیگر با استفاده از عوامل پخت مانند گوگرد یا پراکسیدها اصلاح میشوند.
در ادامه به معرفی و بررسی برخی از مهمترین موادی که ولکانیزه میشوند میپردازیم تا ویژگیها و کاربردهای این مواد در صنایع مختلف را بهتر درک کنیم.
ولکانیزاسیون لاستیک طبیعی
لاستیک طبیعی، یک پلیمر زیستی بر پایه پلیایزوپرن، از طریق فرآیند ولکانیزاسیون به شدت اصلاح میشود. این فرآیند با استفاده از گوگرد به عنوان عامل پخت، پیوندهای عرضی (Cross-links) را بین زنجیرههای پلیمری ایجاد میکند که بهبود قابلتوجهی در خواص مکانیکی مانند استحکام کششی، انعطافپذیری و مقاومت در برابر سایش به همراه دارد. لاستیک طبیعی ولکانیزه شده به دلیل خواص مکانیکی بالا و مقاومت شیمیایی مناسب، در صنایع خودروسازی (بهویژه در تایرها)، تسمهها و قطعات مکانیکی استفاده میشود.
ولکانیزاسیون پلیکلروپرن
پلیکلروپرن یا نئوپرن، یک الاستومر کلردار مصنوعی است که به دلیل وجود کلر در ساختار زنجیرهاش، مقاومت بالایی در برابر مواد شیمیایی و حرارت دارد. فرآیند ولکانیزاسیون پلیکلروپرن میتواند با استفاده از گوگرد یا پراکسیدها انجام شود. پیوندهای عرضی ایجاد شده طی این فرآیند منجر به افزایش پایداری حرارتی، مقاومت در برابر تخریب ازن و بهبود خواص الاستومری میشود. کاربردهای اصلی پلیکلروپرن ولکانیزه شده شامل ساخت درزگیرها، تسمههای انتقال نیرو و لباسهای ضدآب صنعتی است.
ولکانیزاسیون سیلیکون
سیلیکونها گروهی از پلیمرهای غیرآلی-آلی بر پایه زنجیرههای Si-O هستند که پس از ولکانیزاسیون مقاومت بالایی در برابر حرارت، اکسیداسیون و شرایط محیطی سخت از خود نشان میدهند. ولکانیزاسیون سیلیکون معمولاً با استفاده از پراکسیدها یا کاتالیزورهای پلاتینیوم انجام میشود. این فرآیند باعث افزایش مقاومت حرارتی تا 300°C و بهبود خواص الاستیسیته و مقاومت در برابر تخریب ازن و UV میشود. سیلیکونهای ولکانیزه شده در تولید قطعات صنعتی، محصولات پزشکی، و درزگیرهای مقاوم به حرارت کاربرد دارند.
الاستومرهای ترموپلاستیک (TPE/TPV)
الاستومرهای ترموپلاستیک (TPE) و به طور خاص ترموپلاستیکهای ولکانیزه (TPV) ترکیبی از خواص پلاستیکها و لاستیکها را دارا هستند. این مواد طی فرآیند ولکانیزاسیون با پراکسیدها یا رزینها بهبود یافته و پیوندهای عرضی در فاز لاستیکی آنها ایجاد میشود. نتیجه این فرآیند موادی است که هم خواص الاستومری مانند انعطافپذیری و مقاومت به سایش دارند و هم به راحتی قالبگیری و فرآیندپذیری میشوند. TPVها به طور گسترده در قطعات خودرویی، قطعات مصرفی و تجهیزات صنعتی استفاده میشوند.
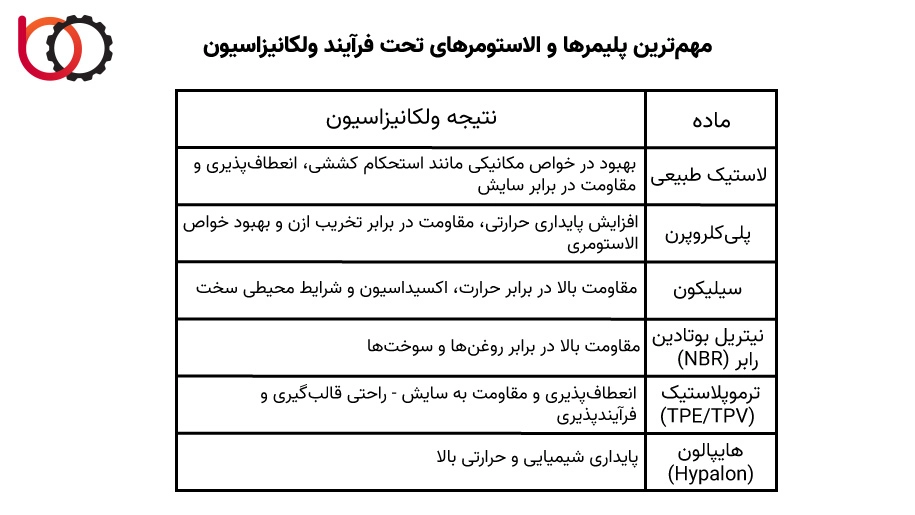
نیتریل بوتادین رابر (NBR)
نیتریل بوتادین رابر (NBR)، یک الاستومر سنتزی بر پایه بوتادین و آکریلونیتریل است که به دلیل مقاومت بالا در برابر روغنها و سوختها، از طریق ولکانیزاسیون بهبود مییابد. ولکانیزاسیون NBR معمولاً با استفاده از گوگرد یا پراکسید انجام میشود و منجر به افزایش مقاومت شیمیایی و مکانیکی آن میگردد. این ماده در تولید واشرها، لولههای انتقال سوخت و سایر قطعات مقاوم به مواد شیمیایی استفاده میشود.
ولکانیزاسیون پلیاتیلن کلردار (CPE)
پلیاتیلن کلردار (CPE) یک الاستومر با زنجیرههای پلیاتیلنی کلردار شده است که به دلیل داشتن گروههای کلر، به طور طبیعی مقاوم در برابر مواد شیمیایی، شعله و حرارت است. ولکانیزاسیون CPE با استفاده از عوامل پخت پراکسیدی یا گوگرد انجام میشود و موجب افزایش پایداری در برابر حرارت، اشعه UV و سایش میشود. CPE ولکانیزه شده به طور گسترده در تولید پوششهای مقاوم به مواد شیمیایی، کابلهای صنعتی و لولههای عایقبندی مورد استفاده قرار میگیرد.
ولکانیزاسیون پلییورتان
پلییورتانها دستهای از پلیمرهای آلی با پیوندهای یورتانی هستند که به دلیل انعطافپذیری و مقاومت به سایش در صنایع مختلف کاربرد دارند. برخی از پلییورتانها از طریق فرآیند ولکانیزاسیون بهبود یافته و پیوندهای عرضی بیشتری ایجاد میکنند که باعث افزایش استحکام مکانیکی، پایداری حرارتی و مقاومت شیمیایی آنها میشود. پلییورتان ولکانیزه شده در تولید قطعات مقاوم به سایش، چرخها و محصولات ورزشی استفاده میشود.
هایپالون (Hypalon)
هایپالون، یک الاستومر کلردار و سولفون کلردار است که به دلیل مقاومت فوقالعادهاش در برابر تخریب ازن، اشعه UV و مواد شیمیایی، از طریق ولکانیزاسیون بهبود مییابد. هایپالون ولکانیزه شده به دلیل پایداری شیمیایی و حرارتی بالا، به طور گسترده در تولید پوششهای محافظتی، عایقهای ضدشعله و محصولات مقاوم به عوامل محیطی شدید استفاده میشود.