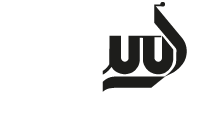
اجزای تشکیل دهنده نوار نقاله
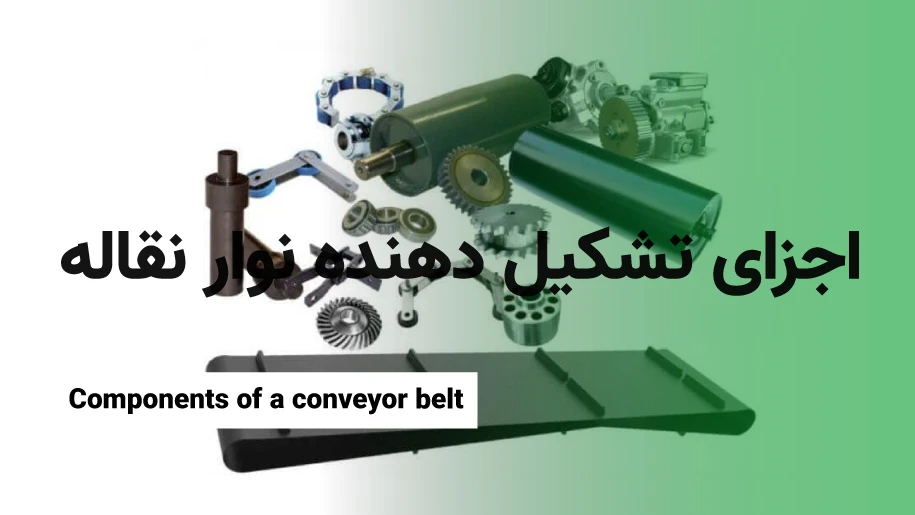
در هر سیستم انتقال مواد، اجزای تشکیلدهنده نقش حیاتی در عملکرد بهینه و کارآمد آن دارند. این مقاله با بررسی دقیق تمامی اجزا، از اصلیترین قطعات مانند تسمه، رولیک و موتور گرفته تا کوچکترین بخشها مانند یاتاقانها و سیستمهای تنظیم کشش، به شناخت بهتر عملکرد و ساختار نوار نقالهها میپردازد. هدف این است که با ارائهی توضیحات تخصصی، تفاوتها، ویژگیها و اهمیت هر قطعه در بهبود بهرهوری و افزایش طول عمر تجهیزات بررسی شود.
اجزای کلیدی در سیستمهای انتقال مواد
در نوار نقالهها، هماهنگی میان اجزا تعیینکنندهی بازدهی، طول عمر و عملکرد کلی تجهیزات است. اجزای تشکیلدهنده نوار نقاله بهعنوان مجموعهای از قطعات مکانیکی و الکترومکانیکی، هرکدام نقشی خاص در حرکت روان و پایدار مواد دارند. بررسی دقیق این اجزا و درک عملکرد آنها، انتخاب، طراحی و نگهداری بهینه را تسهیل میکند.
تأثیر اجزا در عملکرد کلی سیستم
عملکرد صحیح سیستمهای انتقال مواد به ترکیب هماهنگ قطعاتی چون تسمه، رولیکها، غلطکها، موتور و سیستمهای کنترل کشش وابسته است. هرگونه نقص در یکی از این بخشها میتواند باعث افزایش استهلاک، کاهش بازده و توقف عملیات تولیدی شود. برای مثال، تنظیم نادرست کشش تسمههای لاستیکی یا PVC میتواند منجر به لغزش یا پارگی شود، در حالی که استفاده از یاتاقانهای بیکیفیت در رولیکهای هرزگرد باعث افزایش اصطکاک و کاهش عمر مفید تجهیزات خواهد شد.
تقسیمبندی اجزای کلیدی
اجزای اصلی را میتوان در سه دستهی کلی تقسیمبندی کرد:
- اجزای حرکتی و هدایتکننده: شامل تسمه، رولیکهای ثابت و ضربهگیر، غلطکهای هدایتکننده که مسئول حرکت یکنواخت و جلوگیری از انحراف مسیر هستند.
- اجزای تأمین نیرو و انتقال قدرت: شامل الکتروموتور، گیربکس، پولی و تسمههای انتقال قدرت که نیروی لازم برای حرکت را فراهم میکنند.
- سازهها و اجزای پشتیبان: فریمهای نگهدارنده، یاتاقانها، بوشها و سیستمهای ایمنی که باعث استحکام، کاهش اصطکاک و افزایش ایمنی در حین عملیات میشوند.
در ادامه، هر یک از این اجزا بهصورت دقیق بررسی خواهند شد تا نقش آنها در عملکرد بهینهی سیستمهای انتقال مواد بهطور کامل مشخص شود.
تسمهها و مواد سازنده
در میان اجزای تشکیلدهنده نوار نقاله، تسمه نقاله مهمترین بخش محسوب میشود، زیرا وظیفهی جابجایی مواد را بر عهده دارد. انتخاب جنس، ساختار و لایههای داخلی تسمه تأثیر مستقیمی بر دوام، استهلاک و کارایی سیستمهای انتقال مواد دارد. تسمهها بر اساس جنس به انواع مختلفی تقسیم میشوند که هرکدام برای شرایط خاصی طراحی شدهاند.
انواع تسمه بر اساس جنس
انتخاب متریال تسمه، تأثیر مستقیمی بر عملکرد و طول عمر سیستمهای انتقال مواد دارد. هر محیط صنعتی، بسته به نوع مواد جابهجا شونده، شرایط دمایی و سطح اصطکاک، به تسمهای با ویژگیهای خاص نیاز دارد. از تسمههای لاستیکی که در صنایع سنگین کاربرد دارند تا مدلهای PVC و PU که به دلیل ویژگیهای بهداشتی در صنایع غذایی و دارویی مورد استفاده قرار میگیرند، هر نوع تسمه مزایا و محدودیتهای مخصوص خود را دارد. در ادامه، انواع تسمهها بر اساس جنس و ویژگیهای آنها بررسی میشود تا بتوان مناسبترین گزینه را برای هر کاربرد انتخاب کرد.
1. تسمه لاستیکی
تسمههای لاستیکی یکی از رایجترین انواع هستند که به دلیل انعطافپذیری بالا، مقاومت در برابر سایش و قابلیت تحمل ضربه، در صنایع سنگین، معادن و خطوط تولید به کار میروند. برخی از ویژگیهای کلیدی آنها شامل:
- ✔ تحمل بار زیاد بدون تغییر شکل دائمی
- ✔ مقاومت بالا در برابر ساییدگی و ضربه
- ✔ قابلیت استفاده در دماهای مختلف
2. تسمه PVC (پلی وینیل کلراید)
تسمههای PVC به دلیل وزن کم، قابلیت شستوشو و مقاومت شیمیایی بالا، انتخابی مناسب برای صنایع غذایی، دارویی و بستهبندی هستند. این نوع تسمه در برابر روغن، اسیدها و رطوبت مقاوم بوده و قابلیت تولید در ضخامتهای مختلف را دارد.
3. PU (پلی اورتان)
تسمههای PU به دلیل مقاومت بالاتر در برابر پارگی و طول عمر بیشتر نسبت به PVC، در صنایع با شرایط سختتر به کار میروند. ویژگیهای برجسته آنها:
- ✔ مقاومت عالی در برابر مواد خورنده و چربیها
- ✔ سطح بهداشتی برای صنایع غذایی و دارویی
- ✔ مقاومت بالا در برابر دمای بالا و پایین
4. تفلون (PTFE)
تسمههای تفلونی به دلیل مقاومت شیمیایی بسیار بالا و خاصیت نچسب بودن، در فرآیندهایی که نیاز به دمای بالا یا تماس با مواد شیمیایی دارند، کاربرد دارند. کاربردهای رایج آن شامل خطوط تولید با دمای بالا مانند صنایع نساجی و چاپ است.
5. تسمه مدولار (پلاستیکی)
تسمههای مدولار از جنس پلیاتیلن، پلیپروپیلن یا پلیآمید ساخته شدهاند و در سیستمهایی که نیاز به انعطافپذیری بالا و سهولت تعمیر دارند، استفاده میشوند. از جمله ویژگیهای آنها:
- ✔ مقاومت در برابر خوردگی و زنگزدگی
- ✔ امکان تعویض قطعات شکسته بدون نیاز به تعویض کل تسمه
- ✔ مناسب برای حمل مواد بستهبندی و صنایع غذایی
6. تسمه فلزی
تسمههای فلزی از استیل ضدزنگ یا فولاد ساخته شده و برای حمل مواد داغ یا سنگین مانند قطعات فلزی، شیشه و سرامیک در خطوط تولید استفاده میشوند. این تسمهها دارای ویژگیهایی از جمله:
- ✔ مقاومت عالی در برابر دمای بالا
- ✔ تحمل وزنهای سنگین بدون تغییر شکل
- ✔ دوام و طول عمر بالا در شرایط صنعتی سخت
7. تسمه سیمی یا توری (Mesh Belt)
این نوع تسمه از سیمهای فولادی یا استیل ضدزنگ بهصورت مشبک ساخته میشود که به آنها تسمه توری نیز میگویند و معمولاً در صنایع پخت، خشککردن و خنکسازی مورد استفاده قرار میگیرد. ویژگیهای کلیدی:
- ✔ قابلیت عبور جریان هوا و حرارت برای فرآیندهای گرمایشی
- ✔ مقاومت بالا در برابر خوردگی و زنگزدگی
- ✔ دوام بالا در محیطهای مرطوب و شیمیایی
چنانچه قصد خرید تسمه مناسب برای سیستمهای انتقال مواد را دارید، میتوانید به بخش انواع تسمه نقاله مراجعه کرده و مدلهای مختلف را مشاهده کنید. با بررسی مشخصات فنی و ویژگیهای هر نوع، میتوانید گزینهای را انتخاب کنید که متناسب با نیازهای صنعتی شما باشد.
ویژگیهای فنی تسمهها
انتخاب تسمه مناسب به پارامترهای فنی متعددی وابسته است. برخی از مهمترین ویژگیهای فنی که در انتخاب تأثیر دارند، عبارتند از:
- ✔ مقاومت در برابر کشش: توانایی تسمه در حفظ یکپارچگی و جلوگیری از تغییر شکل در برابر بارهای مکانیکی.
- ✔ مقاومت سایشی: افزایش طول عمر تسمه در تماس مداوم با سطوح مختلف.
- ✔ مقاومت حرارتی: قابلیت تحمل دماهای بالا یا پایین در محیطهای کاری خاص.
- ✔ مقاومت در برابر مواد شیمیایی: حفظ خواص فیزیکی در برابر اسیدها، روغنها و حلالها.
- ✔ ضدالکتریسیته ساکن: جلوگیری از تجمع بار الکتریکی برای جلوگیری از خطرات احتمالی.
لایههای داخلی تسمهها
هر تسمه از لایههای داخلی تقویتکننده تشکیل شده است که باعث افزایش استحکام و طول عمر آن میشود. رایجترین ترکیبات این لایهها شامل:
- ✔ منجید: ترکیبی از نخهای پلیاستر یا نایلون که مقاومت کششی تسمه را افزایش میدهد.
- ✔ الیاف پلیاستر: وزن کم، انعطافپذیری بالا و مقاومت در برابر رطوبت.
- ✔ سیمهای فولادی: برای افزایش استحکام در تسمههای سنگین صنعتی.
اجزای تشکیلدهنده نوار نقاله نقش مهمی در عملکرد صحیح سیستمهای انتقال مواد دارند و انتخاب تسمه مناسب بر اساس شرایط کاری، نوع مواد حملشده و محیط عملیاتی، اهمیت بالایی دارد. در بخشهای بعدی، سایر اجزا مانند رولیکها و غلطکهای هدایتکننده بهصورت دقیق بررسی خواهند شد.
رولیکها (غلطکهای هرزگرد)
در میان اجزای تشکیلدهنده نوار نقاله، رولیکها یکی از بخشهای حیاتی هستند که وظیفه هدایت، پشتیبانی و کاهش اصطکاک تسمه را بر عهده دارند. این قطعات استوانهای که در فواصل مشخصی روی ساختار نگهدارنده نصب میشوند، در انواع مختلفی طراحی شدهاند تا متناسب با نوع بار، سرعت حرکت و شرایط عملیاتی بهترین عملکرد را ارائه دهند. انتخاب صحیح رولیکهای ثابت، متحرک، ضربهگیر و برگشتی تأثیر مستقیمی بر طول عمر سیستم و کاهش استهلاک سایر قطعات دارد.
رولیکهای ثابت و متحرک: نقش در هدایت و حمایت تسمه
رولیکهای ثابت نقش اساسی در حفظ تعادل و جلوگیری از انحراف مسیر تسمه دارند. این نوع رولیکها معمولاً در نقاط مستقیم مسیر نصب شده و وظیفهی توزیع یکنواخت فشار تسمه را بر عهده دارند. در مقابل، رولیکهای متحرک که معمولاً در بخشهایی با تغییر زاویه یا در سیستمهای تنظیم کشش به کار میروند، قابلیت تنظیم موقعیت را دارند تا در صورت تغییر در بار یا فشار، از افزایش تنش در تسمه جلوگیری کنند.
- ✔ رولیکهای ثابت: مناسب برای مسیرهای مستقیم و پایدار.
- ✔ رولیکهای متحرک: استفاده در نقاطی که تنظیم کشش یا تغییر مسیر ضروری است.
رولیک ضربهگیر: جذب انرژی و کاهش فشار ناشی از بار ورودی
در نقاطی که بارگذاری مواد روی تسمه انجام میشود، فشار زیادی به ساختار سیستم وارد میشود. برای جلوگیری از آسیب به تسمه و افزایش استهلاک، رولیکهای ضربهگیر در این مناطق نصب میشوند. این نوع رولیکها از لایههای لاستیکی یا پلییورتانی ساخته شدهاند که قابلیت جذب ضربه و جلوگیری از تمرکز فشار در یک نقطه را دارند.
- ✔ حفظ کیفیت تسمه و جلوگیری از ترکخوردگی در نقاط بارگذاری.
- ✔ کاهش تنشهای ناگهانی و جلوگیری از آسیب به سایر اجزا.
رولیک برگشتی: هدایت بخش برگشتی تسمه برای کاهش اصطکاک
در سیستمهای انتقال مواد، تسمه پس از عبور از مسیر حمل بار، باید دوباره به نقطه ابتدایی برگردد. رولیکهای برگشتی وظیفه هدایت بخش برگشتی تسمه را بر عهده دارند تا اصطکاک آن با بخشهای فلزی سازه به حداقل برسد و از افزایش مصرف انرژی و استهلاک بیرویه جلوگیری شود. این نوع رولیکها معمولاً دارای سطح صاف یا مشبک هستند تا از چسبیدن ذرات مواد باقیمانده به تسمه جلوگیری کنند.
- ✔ کاهش اصطکاک بین تسمه و ساختار نگهدارنده.
- ✔ جلوگیری از آسیبهای ناشی از اصطکاک مداوم.
یاتاقانهای رولیک: کاهش اصطکاک و افزایش طول عمر
هر رولیک برای چرخش روان نیاز به یک سیستم یاتاقانبندی دارد. یاتاقانهای رولیک وظیفه کاهش اصطکاک بین محور رولیک و بدنهی آن را بر عهده دارند، که تأثیر مستقیمی بر کاهش مصرف انرژی و افزایش طول عمر قطعات دارد.
- ✔ یاتاقانهای غلتشی: کاهش چشمگیر اصطکاک و افزایش سرعت عملکرد.
- ✔ یاتاقانهای لغزشی: استفاده در شرایطی که نیاز به تحمل بارهای سنگینتر است.
رولیکها، علاوه بر هدایت تسمه، نقش مهمی در کاهش استهلاک و افزایش کارایی سیستم انتقال مواد دارند. انتخاب مناسب رولیک ثابت، متحرک، ضربهگیر و برگشتی همراه با یاتاقانهای باکیفیت، موجب بهینهسازی عملکرد و کاهش هزینههای نگهداری خواهد شد. در ادامه، سایر اجزای سیستم مانند غلطکهای کشنده و هدایتکننده بهصورت دقیق بررسی خواهند شد.
غلطکهای کشنده و هدایتکننده (درامها)
در میان اجزای تشکیلدهنده نوار نقاله، غلطکهای کشنده و هدایتکننده نقش کلیدی در انتقال نیرو، تنظیم کشش تسمه و جلوگیری از لغزش آن دارند. این غلطکها که معمولاً با نام درامهای محرک و انتهایی شناخته میشوند، در موقعیتهای مشخصی از سیستم نصب شده و باعث حرکت و هدایت تسمه میشوند. بدون عملکرد صحیح این بخش، استفاده از سایر اجزای تشکیلدهنده نوار نقاله کارایی لازم را نخواهد داشت، چرا که درامها کنترل اصلی حرکت را بر عهده دارند.
غلطک محرک: انتقال قدرت از موتور به تسمه
درام محرک (Drive Pulley) وظیفهی انتقال نیرو از موتور به تسمه را دارد و یکی از اصلیترین اجزای تشکیلدهنده نوار نقاله محسوب میشود. این غلطک معمولاً با استفاده از الکتروموتور، گیربکس و کوپلینگها به سیستم انتقال قدرت متصل شده و انرژی لازم را برای حرکت تسمه تأمین میکند.
- ✔ افزایش اصطکاک برای جلوگیری از لغزش تسمه در حین حرکت.
- ✔ توزیع یکنواخت نیرو برای عملکرد بهتر سایر اجزای تشکیلدهنده نوار نقاله.
- ✔ بهبود کارایی سیستم با استفاده از طراحیهای مقاوم و پوششهای مناسب.
غلطک انتهایی: تنظیم کشش تسمه در انتهای مسیر
درام انتهایی (Tail Pulley) در مقابل درام محرک قرار دارد و با تنظیم کشش تسمه، به هدایت صحیح آن در بازگشت به مسیر اولیه کمک میکند. این غلطک از جمله اجزای تشکیلدهنده نوار نقاله است که در عملکرد پایدار سیستم نقش دارد و در سیستمهای طولانیتر، امکان افزایش یا کاهش کشش تسمه را فراهم میکند.
- ✔ حفظ کشش یکنواخت در طول سیستم انتقال مواد.
- ✔ افزایش طول عمر تسمه با توزیع متناسب فشار.
- ✔ جلوگیری از انحراف تسمه و کاهش فشار بر روی رولیکهای هرزگرد.
غلطکهای تنظیمی (Tension Pulley): جلوگیری از لغزش تسمه
در هر سیستم انتقال مواد، کشش تسمه باید در حد استاندارد باشد، در غیر این صورت عملکرد صحیح دیگر اجزای تشکیلدهنده نوار نقاله دچار مشکل خواهد شد. اگر کشش کم باشد، تسمه دچار لغزش شده و انتقال مواد به درستی انجام نمیشود، اما اگر کشش بیشازحد باشد، میتواند باعث آسیب به یاتاقانها، رولیکها و حتی تسمه شود. غلطکهای تنظیمی با کنترل کشش، مانع بروز چنین مشکلاتی میشوند.
- ✔ کنترل دقیق کشش برای افزایش طول عمر تسمه.
- ✔ حفظ پایداری در طول مسیر و جلوگیری از انحراف تسمه.
- ✔ کاهش فشار اضافی روی موتور و اجزای مکانیکی سیستم.
پوشش غلطک: لاستیکی، سرامیکی، آجدار برای افزایش اصطکاک
پوشش سطح غلطکها نقش مهمی در افزایش اصطکاک و جلوگیری از لغزش تسمه دارد. استفاده از متریالهای مقاوم باعث میشود که دیگر اجزای تشکیلدهنده نوار نقاله دچار استهلاک زودهنگام نشوند. متداولترین انواع پوشش غلطکها عبارتند از:
- ✔ پوشش لاستیکی: جلوگیری از لغزش تسمه، افزایش استحکام و کاهش ارتعاشات.
- ✔ پوشش سرامیکی: مقاوم در برابر خوردگی و دماهای بالا.
- ✔ پوشش آجدار: بهبود چسبندگی تسمه در محیطهای مرطوب یا آلوده.
غلطکهای کشنده و هدایتکننده، از مهمترین اجزای تشکیلدهنده نوار نقاله محسوب میشوند که بدون عملکرد صحیح آنها، دیگر بخشهای سیستم کارایی لازم را نخواهند داشت. تنظیم کشش، انتقال نیرو و جلوگیری از لغزش، سه عامل کلیدی در عملکرد صحیح این قطعات است. در ادامه، سایر اجزای تشکیلدهنده نوار نقاله مانند موتور و سیستمهای انتقال قدرت بررسی خواهند شد.
موتور و سیستمهای انتقال قدرت
در میان اجزای تشکیلدهنده نوار نقاله، موتور و سیستمهای انتقال قدرت نقشی کلیدی در تأمین انرژی حرکتی تسمه و کنترل سرعت انتقال مواد دارند. عملکرد صحیح این بخش تأثیر مستقیمی بر بهرهوری، کاهش مصرف انرژی و افزایش طول عمر سایر قطعات مکانیکی دارد. انتخاب نوع الکتروموتور، گیربکس و کوپلینگها باید متناسب با شرایط عملیاتی، وزن مواد حملشده و نوع تسمه انجام شود تا بیشترین کارایی را ارائه دهد.
انواع الکتروموتور: AC، DC و گیربکسی
موتورهای الکتریکی، تأمینکننده نیروی حرکتی موردنیاز تسمه هستند و بسته به نیاز سیستم، در مدلهای مختلف استفاده میشوند.
- ✔ الکتروموتورهای AC (جریان متناوب): رایجترین نوع موتورهای صنعتی که بازدهی بالا، هزینه نگهداری کم و طول عمر طولانی دارند. مناسب برای سیستمهای انتقال مواد در صنایع سنگین.
- ✔ الکتروموتورهای DC (جریان مستقیم): دارای کنترل دقیقتر سرعت و گشتاور، مناسب برای کاربردهایی که نیاز به تغییرات سرعتی نرم و پیوسته دارند.
- ✔ موتورهای گیربکسی: ترکیبی از موتور الکتریکی و گیربکس داخلی که بدون نیاز به سیستمهای انتقال قدرت اضافه، سرعت و گشتاور خروجی را بهینهسازی میکند.
انتخاب نوع موتور، تأثیر مستقیمی بر عملکرد سایر اجزای تشکیلدهنده نوار نقاله دارد و تنظیم نامناسب آن میتواند باعث افزایش استهلاک، کاهش بازدهی و حتی توقف ناگهانی سیستم شود.
گیربکسها: حلزونی، خورشیدی و هلیکال
گیربکسها در سیستمهای انتقال قدرت وظیفه کاهش سرعت موتور و افزایش گشتاور را بر عهده دارند. این قطعات باعث بهینهسازی عملکرد تسمه شده و از آسیبهای احتمالی به اجزای تشکیلدهنده نوار نقاله جلوگیری میکنند.
- ✔ گیربکس حلزونی: دارای طراحی فشرده و مناسب برای کاهش سرعت با زاویه ۹۰ درجه، اما راندمان کمتری نسبت به مدلهای دیگر دارد.
- ✔ گیربکس خورشیدی: راندمان بالا، استحکام زیاد و توزیع یکنواخت نیرو، مناسب برای سیستمهایی که به انتقال نیروی مداوم و بدون ضربه نیاز دارند.
- ✔ گیربکس هلیکال: انتقال قدرت نرمتر، کاهش لرزش و استهلاک کمتر، مناسب برای سیستمهایی با دورهای بالا و بار سنگین.
انتخاب گیربکس مناسب، تأثیر مستقیمی بر طول عمر تسمه و بهینهسازی مصرف انرژی در سیستمهای انتقال مواد دارد.
کوپلینگها و اتصالات: برای انتقال یکنواخت نیرو
کوپلینگها قطعاتی هستند که نیروی موتور را بدون ایجاد ضربه به گیربکس یا سایر بخشهای انتقال قدرت منتقل میکنند. استفاده از کوپلینگهای مناسب در میان اجزای تشکیلدهنده نوار نقاله، باعث افزایش طول عمر سایر قطعات و کاهش استهلاک میشود.
- ✔ کوپلینگ انعطافپذیر: کاهش لرزشها و ضربات ناگهانی، مناسب برای جلوگیری از شکستگی در شفت موتور.
- ✔ کوپلینگ صلب: مناسب برای سیستمهایی که نیاز به انتقال نیرو بدون تغییر زاویه دارند.
- ✔ کوپلینگ هیدرولیکی: استفاده در سیستمهایی که نیاز به تنظیم سرعت متغیر دارند.
انتخاب نادرست کوپلینگ میتواند باعث انتقال نامناسب نیرو و کاهش کارایی سایر اجزای تشکیلدهنده نوار نقاله شود.
پولی و تسمه انتقال قدرت: کاهش بار موتور و تنظیم سرعت
پولی و تسمههای انتقال قدرت نقش مهمی در انتقال نیرو از موتور به سایر اجزا دارند و معمولاً در سیستمهای کاهش دور و تنظیم سرعت استفاده میشوند. برخلاف درامها (Drum Pulley) که در تماس مستقیم با تسمهی نقاله قرار دارند و باعث هدایت آن میشوند، پولیها در بخش انتقال قدرت موتور به گیربکس یا دیگر بخشهای مکانیکی کاربرد دارند. این تفاوت باعث میشود که پولی و تسمههای انتقال قدرت بهعنوان اجزای کمکی در بهینهسازی سرعت و کاهش بار روی الکتروموتور استفاده شوند.
- ✔ پولیهای انتقال قدرت معمولاً روی محور موتور یا گیربکس نصب شده و نیرو را به تسمههای V شکل یا دندانهدار منتقل میکنند.
- ✔ تسمههای انتقال قدرت از جنس لاستیک تقویتشده، پلییورتان یا نئوپرن ساخته میشوند تا دوام و استحکام کافی را داشته باشند.
- ✔ این سیستم باعث کاهش بار اضافی روی موتور و افزایش بازدهی سیستم انتقال قدرت میشود.
در حالی که درامها مستقیماً درگیر حرکت تسمه نقاله هستند، پولیها بخش کمکی انتقال نیرو محسوب میشوند که امکان تنظیم سرعت و کنترل بار موتور را فراهم میکنند.
زنجیر و چرخزنجیر: در سیستمهای انتقال زنجیری
در برخی از سیستمهای انتقال مواد، بهجای تسمه از زنجیر و چرخزنجیر استفاده میشود. این روش برای جابجایی بارهای سنگین و محیطهای سخت صنعتی که نیاز به استحکام بالا دارند، گزینهای مناسب است.
✔ چرخزنجیر از جنس فولاد مقاوم ساخته شده و دارای دندانههایی برای درگیری با زنجیر است.
✔ زنجیرها از جنس فولاد آلیاژی یا استیل ضدزنگ تولید میشوند و در برابر سایش مقاوم هستند.
✔ این سیستم، در محیطهای پر از گردوغبار، چرب یا دارای تغییرات دمایی زیاد، عملکرد بهتری نسبت به تسمهها دارد.
سیستم زنجیر و چرخزنجیر به دلیل استحکام بالا، یکی از اجزای تشکیلدهنده نوار نقاله در صنایع سنگین مانند معادن و فولادسازی محسوب میشود.
موتور و سیستمهای انتقال قدرت، یکی از مهمترین اجزای تشکیلدهنده نوار نقاله محسوب میشوند که عملکرد صحیح آنها تأثیر مستقیمی بر افزایش بهرهوری، کاهش مصرف انرژی و جلوگیری از خرابی قطعات دیگر دارد. در این بخش، انواع الکتروموتور، گیربکس، کوپلینگ، پولی، تسمه انتقال قدرت و زنجیر و چرخزنجیر بررسی شدند. در ادامه، سایر اجزای تشکیلدهنده نوار نقاله شامل سازهها و قطعات پشتیبان مورد بررسی قرار خواهند گرفت.
سازه و فریمهای نگهدارنده
در میان اجزای تشکیلدهنده نوار نقاله، سازه و فریمهای نگهدارنده نقش اساسی در استحکام، ثبات و کاهش لرزشهای سیستم انتقال مواد دارند. فریمها نهتنها از تجهیزات مکانیکی مانند رولیکها، غلطکها و موتور پشتیبانی میکنند، بلکه بر نحوه نصب و نگهداری سیستم تأثیر مستقیم دارند. طراحی سازهای بهینه، علاوه بر افزایش عمر مفید سایر قطعات، باعث کاهش هزینههای تعمیر و نگهداری نیز خواهد شد.
متریالهای استفادهشده در ساخت سازه
انتخاب متریال در فریمهای نگهدارنده بر اساس نوع بار، شرایط محیطی و نیاز به مقاومت در برابر خوردگی و ضربه انجام میشود. رایجترین متریالها شامل:
- ✔ فولاد ST37: پرکاربردترین گزینه برای سازههای صنعتی به دلیل استحکام بالا و قیمت مناسب.
- ✔ استیل ضدزنگ (Stainless Steel): مناسب برای محیطهای مرطوب، خورنده و صنایع غذایی به دلیل مقاومت در برابر زنگزدگی.
- ✔ آلومینیوم: دارای وزن کم و مقاومت قابلقبول، مناسب برای سیستمهایی که نیاز به جابجایی و نصب آسانتر دارند.
انتخاب جنس مناسب برای سازه باعث افزایش استحکام کلی سیستم و کاهش هزینههای نگهداری در بلندمدت میشود.
طراحی فریم بسته و باز: تأثیر در استحکام و نگهداری
فریمهای نگهدارنده در دو نوع کلی بسته و باز طراحی میشوند که هرکدام تأثیر مستقیمی بر استحکام سازه و سهولت در نگهداری دارند:
- ✔ فریم بسته: این نوع طراحی، دوام و مقاومت بالاتری دارد و در سیستمهایی که نیاز به تحمل بار سنگین و جلوگیری از نفوذ گردوغبار و رطوبت دارند، استفاده میشود.
- ✔ فریم باز: این طراحی باعث سهولت در دسترسی به قطعات داخلی مانند رولیکها و موتور میشود و در سیستمهایی که نیاز به تعمیرات مکرر دارند، گزینهی بهتری محسوب میشود.
انتخاب نوع فریم بسته یا باز بستگی به شرایط عملیاتی و نیاز به تعمیرات دورهای دارد.
پایهها و ضربهگیرها: جلوگیری از لرزش و افزایش پایداری
یکی از چالشهای رایج در سیستمهای انتقال مواد، لرزش بیشازحد و عدم ثبات سازهای است که میتواند باعث افزایش استهلاک قطعات و کاهش راندمان سیستم شود. برای جلوگیری از این مشکلات، پایههای مقاوم و ضربهگیرهای صنعتی در فریمهای نگهدارنده استفاده میشوند.
- ✔ پایههای قابل تنظیم: این پایهها امکان تنظیم ارتفاع و ایجاد تعادل روی سطوح ناصاف را فراهم میکنند.
- ✔ ضربهگیرهای لاستیکی یا پلییورتانی: جذب لرزشهای ناشی از حرکت تسمه و ضربات مکانیکی، کاهش نویز و افزایش طول عمر قطعات.
- ✔ استفاده از پیچ و مهرههای ضدلرزش: جلوگیری از باز شدن اتصالات در اثر ارتعاشات پیوسته.
طراحی و استفاده صحیح از پایهها و ضربهگیرها در کنار سایر اجزای تشکیلدهنده نوار نقاله، باعث افزایش پایداری و کاهش استهلاک قطعات سیستم خواهد شد.
سازه و فریمهای نگهدارنده، علاوه بر تحمل وزن سایر اجزای تشکیلدهنده نوار نقاله، نقش مهمی در افزایش استحکام، کاهش لرزش و تسهیل نگهداری سیستم دارند. انتخاب متریال مناسب، طراحی بهینه فریم و استفاده از پایهها و ضربهگیرهای استاندارد، تأثیر مستقیمی بر کارایی و طول عمر سیستمهای انتقال مواد خواهد داشت. در ادامه، سایر اجزای تشکیلدهنده نوار نقاله شامل سیستمهای تنظیم کشش و جلوگیری از لغزش تسمه بررسی خواهند شد.
سیستمهای تنظیم کشش و جلوگیری از لغزش
در میان اجزای تشکیلدهنده نوار نقاله، سیستمهای تنظیم کشش و جلوگیری از لغزش نقش کلیدی در عملکرد پایدار و کاهش استهلاک تسمه دارند. تنظیم صحیح کشش تسمه اهمیت زیادی دارد، زیرا اگر کشش بیش از حد باشد، فشار اضافی بر موتور، رولیکها و یاتاقانها وارد شده و استهلاک قطعات افزایش مییابد. از سوی دیگر، اگر کشش کم باشد، تسمه دچار لغزش شده و انتقال مواد بهدرستی انجام نخواهد شد. بنابراین، استفاده از سیستمهای مکانیکی و خودتنظیم برای کنترل کشش و جلوگیری از لغزش تسمه ضروری است.
پیچهای تنظیم کشش: اعمال کشش مناسب به تسمه
یکی از روشهای رایج برای تنظیم کشش تسمه در سیستمهای انتقال مواد، استفاده از پیچهای تنظیم کشش است. این پیچها معمولاً در دو طرف غلطک انتهایی نصب شده و با تنظیم آنها، میزان کشش تسمه قابلاصلاح است.
✔ امکان تنظیم کشش تسمه بر اساس نیاز عملیاتی.
✔ کاهش خطر پارگی یا شلشدن تسمه در طول مسیر.
✔ افزایش طول عمر دیگر اجزای تشکیلدهنده نوار نقاله با کاهش فشارهای اضافی.
در سیستمهایی که نیاز به کنترل دقیق کشش و تنظیم دستی دارند، پیچهای تنظیم یکی از سادهترین و مؤثرترین راهکارها محسوب میشوند.
سیستمهای خودتنظیم: استفاده از وزنه یا فنر برای حفظ کشش مطلوب
در بسیاری از سیستمهای انتقال مواد، نیاز به تنظیم خودکار کشش تسمه وجود دارد تا از کاهش کارایی در اثر تغییرات بار یا طول تسمه جلوگیری شود. برای این منظور، از سیستمهای خودتنظیم با مکانیزم وزنه یا فنر استفاده میشود که بهصورت دینامیکی کشش تسمه را متعادل نگه میدارند.
- ✔ سیستم وزنهای: در این روش، یک وزنه به غلطک انتهایی متصل شده و با جابهجایی آن، کشش تسمه بهصورت خودکار تنظیم میشود. این روش در سیستمهای انتقال مواد سنگین و مسیرهای طولانی بسیار کاربردی است.
- ✔ سیستم فنری: در این روش، فنرهای صنعتی برای جبران تغییرات کشش در اثر انبساط یا انقباض تسمه استفاده میشوند. این مکانیزم در سیستمهای سبکتر و کاربردهای با تغییرات بار کمتر استفاده میشود.
این سیستمها با تنظیم خودکار کشش، مانع از لغزش تسمه شده و باعث افزایش بهرهوری و کاهش نیاز به تعمیرات دستی میشوند.
روکشهای ضدلغزش: پوششهای لاستیکی، آجدار و چسبی
لغزش تسمه روی غلطکها میتواند منجر به کاهش کارایی و آسیبهای جدی در سیستمهای انتقال مواد شود. برای جلوگیری از این مشکل، از روکشهای ضدلغزش روی غلطکهای محرک و هدایتکننده استفاده میشود. این پوششها علاوه بر جلوگیری از لغزش، باعث افزایش اصطکاک بین تسمه و غلطکها شده و بازدهی سیستم را بهبود میبخشند.
- ✔ پوشش لاستیکی: مناسب برای افزایش اصطکاک در محیطهای خشک و مرطوب.
- ✔ پوشش آجدار: طراحی شده برای جلوگیری از لغزش در شرایطی که بار سنگین و سرعت بالا وجود دارد.
- ✔ پوشش چسبی: گزینهای برای شرایطی که نیاز به افزایش اصطکاک در کوتاهمدت بدون تغییر در طراحی غلطکها وجود دارد.
استفاده از این روکشها یکی از راهکارهای مؤثر برای کاهش استهلاک تسمه و بهبود عملکرد سایر اجزای تشکیلدهنده نوار نقاله است.
سیستمهای تنظیم کشش و جلوگیری از لغزش، از بخشهای حیاتی در عملکرد صحیح اجزای تشکیلدهنده نوار نقاله محسوب میشوند. استفاده از پیچهای تنظیم، سیستمهای خودتنظیم با وزنه یا فنر و روکشهای ضدلغزش، باعث کاهش استهلاک، جلوگیری از خرابی و افزایش بازدهی سیستمهای انتقال مواد خواهد شد. در ادامه، سایر اجزای تشکیلدهنده نوار نقاله شامل سیستمهای ایمنی و کنترل بررسی خواهند شد.
سیستمهای ایمنی و کنترل
در میان اجزای تشکیلدهنده نوار نقاله، سیستمهای ایمنی و کنترل نقش اساسی در جلوگیری از بروز حوادث، کاهش آسیبهای احتمالی و افزایش طول عمر تجهیزات دارند. عملکرد صحیح این سیستمها نهتنها از خرابی قطعات مکانیکی جلوگیری میکند، بلکه باعث بهبود بهرهوری و ایمنی کلی محیط صنعتی نیز میشود. کنترل سرعت، جلوگیری از اضافهبار و امکان توقف اضطراری از جمله ویژگیهای ضروری در سیستمهای پیشرفته انتقال مواد است.
سنسورهای توقف اضطراری: قطع خودکار در مواقع خطر
یکی از مهمترین ویژگیهای ایمنی در سیستمهای انتقال مواد، وجود سنسورهای توقف اضطراری است که در مواقع خطر، سیستم را بهسرعت متوقف میکنند. این سنسورها معمولاً در طول مسیر تسمه نصب شده و در صورت بروز شرایط خطرناک مانند گیرکردن مواد، افزایش ناگهانی فشار یا برخورد کارگران با تسمه، فرمان قطع سریع را صادر میکنند.
✔ سنسورهای لیزری و فتوالکتریک: تشخیص سریع موانع و توقف فوری سیستم.
✔ کلیدهای قطع اضطراری (Emergency Stop Switches): امکان توقف دستی در مواقع اضطراری.
✔ سیستمهای هوشمند کنترل از راه دور: کاهش زمان واکنش و افزایش ایمنی در خطوط اتوماسیون.
این سنسورها از آسیب به سایر اجزای تشکیلدهنده نوار نقاله جلوگیری کرده و باعث افزایش سطح ایمنی در محیطهای صنعتی میشوند.
سیستمهای تشخیص بار اضافی: جلوگیری از آسیب به موتور و تسمه
اضافهبار یکی از رایجترین مشکلات در سیستمهای انتقال مواد است که میتواند باعث افزایش فشار روی موتور، تسمه و دیگر قطعات مکانیکی شود. برای جلوگیری از این آسیبها، سیستمهای تشخیص بار اضافی بهکار گرفته میشوند که در صورت افزایش بیش از حد بار، سیستم را متوقف کرده یا توان موتور را کاهش میدهند.
- ✔ سیستمهای حسگر وزن: استفاده از سنسورهای توزین برای تشخیص بار بیش از حد مجاز.
- ✔ کنترل جریان موتور: کاهش ولتاژ ورودی برای جلوگیری از فشار بیش از حد روی تجهیزات الکتریکی.
- ✔ سیستمهای هشداردهنده: اعلام اضافهبار برای جلوگیری از خرابی قطعات مکانیکی.
استفاده از این سیستمها باعث افزایش بهرهوری، کاهش هزینههای تعمیرات و جلوگیری از توقفهای ناگهانی در سیستمهای انتقال مواد میشود.
سیستمهای ترمز اضطراری: توقف سریع در مواقع ضروری
در برخی از کاربردهای صنعتی، توقف سریع تسمه یک ضرورت است، بهویژه زمانی که مواد حساس یا خطرناک در حال انتقال باشند. برای این منظور، سیستمهای ترمز اضطراری طراحی شدهاند که در صورت قطع برق، افزایش ناگهانی سرعت یا شناسایی خطرات، بهطور خودکار وارد عمل شده و حرکت تسمه را متوقف میکنند.
✔ ترمزهای الکترومغناطیسی: واکنش سریع به فرمان قطع و جلوگیری از حرکت ناگهانی تسمه.
✔ سیستمهای ترمز مکانیکی: استفاده از دیسک و کالیپر برای توقف کنترلشده.
✔ ترمزهای بادی (پنوماتیکی): ایجاد نیروی توقف قوی برای تسمههای با سرعت بالا.
این سیستمها از آسیب به اجزای تشکیلدهنده نوار نقاله جلوگیری کرده و ایمنی محیط کاری را افزایش میدهند.
کلیدهای کنترل سرعت: تنظیم سرعت متناسب با نیاز
کنترل سرعت تسمه در بسیاری از سیستمهای انتقال مواد اهمیت زیادی دارد، زیرا سرعت نامناسب میتواند باعث استهلاک زودرس، افزایش مصرف انرژی و کاهش دقت در فرآیندهای تولیدی شود. برای تنظیم بهینه سرعت، کلیدهای کنترل سرعت بهکار گرفته میشوند که امکان تغییر سرعت تسمه متناسب با نوع مواد، شرایط محیطی و ظرفیت سیستم را فراهم میکنند.
- ✔ درایوهای کنترل سرعت (VFD – Variable Frequency Drive): تغییر دور موتور بر اساس نیاز عملیاتی.
- ✔ کلیدهای تنظیم دور موتور: تنظیم سرعت دستی برای هماهنگی با شرایط کاری.
- ✔ سیستمهای اتوماتیک تنظیم سرعت: هماهنگی سرعت تسمه با ورودی و خروجی مواد.
این سیستمها به بهینهسازی مصرف انرژی، کاهش استهلاک و افزایش طول عمر سایر اجزای تشکیلدهنده نوار نقاله کمک میکنند.
سیستمهای ایمنی و کنترل، از اجزای ضروری در طراحی و عملکرد صحیح سیستمهای انتقال مواد هستند که باعث جلوگیری از آسیبهای احتمالی، افزایش بهرهوری و کاهش هزینههای تعمیرات میشوند. استفاده از سنسورهای توقف اضطراری، سیستمهای تشخیص بار اضافی، ترمزهای اضطراری و کلیدهای کنترل سرعت، امکان مدیریت بهینه سیستم را فراهم کرده و به افزایش ایمنی در محیطهای صنعتی کمک میکند. در ادامه، سایر اجزای تشکیلدهنده نوار نقاله شامل یاتاقانها و بوشهای نگهدارنده بررسی خواهند شد.
یاتاقانها و بوشهای نگهدارنده
در میان اجزای تشکیلدهنده نوار نقاله، یاتاقانها و بوشهای نگهدارنده نقشی اساسی در کاهش اصطکاک، افزایش طول عمر قطعات متحرک و بهینهسازی عملکرد سیستم دارند. این قطعات که معمولاً در محل اتصال غلطکها، رولیکها و سیستمهای انتقال قدرت به کار میروند، با ایجاد یک سطح لغزشی یا غلتشی، از اصطکاک غیرضروری جلوگیری کرده و موجب کاهش مصرف انرژی و استهلاک تجهیزات میشوند. انتخاب صحیح نوع یاتاقان و بوش، تأثیر مستقیمی بر بازدهی و دوام سایر اجزای تشکیلدهنده نوار نقاله دارد.
یاتاقانهای غلتشی و لغزشی: کاهش اصطکاک در غلطکها و رولیکها
یاتاقانها یکی از مهمترین اجزای حرکتی در سیستمهای انتقال مواد هستند که وظیفهی کاهش اصطکاک بین قطعات دوار را بر عهده دارند. در سیستمهای صنعتی معمولاً از دو نوع یاتاقان غلتشی و لغزشی استفاده میشود که هرکدام دارای ویژگیهای مخصوص به خود هستند:
✔ یاتاقانهای غلتشی: در این نوع یاتاقانها، توپیهای فلزی یا غلتکهای استوانهای بین دو سطح متحرک قرار دارند و باعث کاهش چشمگیر اصطکاک و افزایش سرعت چرخش غلطکها و رولیکها میشوند.
✔ یاتاقانهای لغزشی: در این نوع، سطوح مستقیماً روی هم حرکت میکنند و معمولاً در قطعاتی که نیاز به تحمل بار سنگین دارند به کار میروند. این نوع یاتاقانها اگرچه اصطکاک بیشتری نسبت به مدلهای غلتشی دارند، اما در شرایط خاص دوام بالاتری ارائه میدهند.
استفاده از یاتاقانهای مناسب در رولیکها و غلطکها باعث کاهش فشار بر روی سایر اجزای تشکیلدهنده نوار نقاله شده و از افزایش مصرف انرژی و آسیبهای احتمالی جلوگیری میکند.
بوشهای پلاستیکی و فلزی: افزایش دوام و کاهش سایش
بوشها قطعاتی هستند که بین دو سطح متحرک قرار گرفته و وظیفه کاهش اصطکاک و افزایش مقاومت در برابر سایش را بر عهده دارند. این قطعات در رولیکها، محورهای غلطکها و سایر بخشهای متحرک سیستمهای انتقال مواد استفاده میشوند و بسته به شرایط عملیاتی، از جنس پلاستیکی یا فلزی ساخته میشوند.
بوشهای پلاستیکی:
- ساختهشده از موادی مانند نایلون، تفلون (PTFE) یا پلییورتان، که اصطکاک کمی دارند و در محیطهای کمبار و خشک استفاده میشوند.
- مقاومت در برابر خوردگی و عدم نیاز به روغنکاری مداوم.
- کاهش نویز و لرزش در حین عملکرد سیستم
بوشهای فلزی:
- از جنس برنج، فولاد آلیاژی یا استیل ضدزنگ ساخته شده و تحمل بار و فشار بیشتری نسبت به مدلهای پلاستیکی دارند.
- مناسب برای محیطهای با دما و فشار بالا.
- نیاز به روغنکاری منظم برای جلوگیری از افزایش اصطکاک.
انتخاب صحیح بوشها، نقش کلیدی در افزایش دوام و کاهش سایش سایر اجزای تشکیلدهنده نوار نقاله دارد. در سیستمهایی که نیاز به حرکت نرم، کاهش نویز و جلوگیری از خوردگی وجود دارد، بوشهای پلاستیکی گزینهی بهتری هستند، درحالیکه در شرایطی که تحمل بار و استحکام بالا ضروری است، بوشهای فلزی استفاده میشوند.
یاتاقانها و بوشهای نگهدارنده از مهمترین اجزای تشکیلدهنده نوار نقاله هستند که با کاهش اصطکاک و جلوگیری از سایش قطعات متحرک، موجب افزایش بهرهوری و کاهش هزینههای نگهداری میشوند. استفاده از یاتاقانهای غلتشی و لغزشی در رولیکها و غلطکها و انتخاب بوشهای پلاستیکی یا فلزی متناسب با شرایط عملیاتی، تأثیر مستقیمی بر کارایی سیستمهای انتقال مواد دارد. در ادامه، سایر اجزای تشکیلدهنده نوار نقاله شامل لوازم جانبی و تکمیلی بررسی خواهند شد.
لوازم جانبی و تکمیلی
در میان اجزای تشکیلدهنده نوار نقاله، لوازم جانبی و تکمیلی نقش مهمی در بهینهسازی عملکرد، افزایش ایمنی و کاهش استهلاک قطعات دارند. این اجزا اگرچه ممکن است مستقیماً در انتقال نیرو یا حرکت تسمه تأثیر نداشته باشند، اما با فراهم کردن شرایط کاری مطلوب، باعث افزایش طول عمر تجهیزات و کاهش هزینههای تعمیر و نگهداری میشوند. روغنکاری سیستمهای متحرک، محافظت از اجزا و جمعآوری مواد ریزشی از جمله مهمترین بخشهای این سیستمهای کمکی هستند.
روغنکاری و سیستمهای روانکاری خودکار: افزایش طول عمر قطعات متحرک
در تمامی سیستمهای انتقال مواد، اصطکاک بین قطعات متحرک میتواند باعث افزایش استهلاک و کاهش بازدهی شود. برای جلوگیری از این مشکل، استفاده از سیستمهای روانکاری دستی یا خودکار ضروری است.
- ✔ روغنکاری دستی: استفاده از گریس یا روغن صنعتی بهصورت دورهای برای کاهش اصطکاک در یاتاقانها، رولیکها و بوشها.
- ✔ سیستمهای روانکاری خودکار: تجهیزاتی که روغن یا گریس را بهصورت خودکار و کنترلشده به نقاط حساس انتقال میدهند و از کمبود یا تجمع بیشازحد روانکار جلوگیری میکنند.
- ✔ کاهش نیاز به تعمیرات مکرر و افزایش طول عمر سایر اجزای تشکیلدهنده نوار نقاله.
انتخاب روش مناسب روانکاری، تأثیر مستقیمی بر عملکرد پایدار سیستم و کاهش مصرف انرژی دارد.
محافظهای کناری و درپوشها: جلوگیری از آسیب به تسمه و قطعات داخلی
در بسیاری از سیستمهای انتقال مواد، ضربات ناگهانی یا ورود اجسام خارجی میتواند باعث آسیب به تسمه و سایر قطعات شود. برای جلوگیری از این مشکلات، از محافظهای کناری و درپوشهای مخصوص استفاده میشود.
محافظهای کناری:
جلوگیری از خروج مواد از روی تسمه و افزایش ایمنی در انتقال بار.
کاهش خطر تماس کارگران با قطعات متحرک و افزایش ایمنی صنعتی.
درپوشها و کاورها:
حفاظت از قطعات داخلی مانند رولیکها، یاتاقانها و غلطکها در برابر گردوغبار، رطوبت و ضربه.
جلوگیری از ورود مواد زائد به بخشهای حساس سیستم.
این محافظها نهتنها از آسیب به اجزای تشکیلدهنده نوار نقاله جلوگیری میکنند، بلکه باعث افزایش ایمنی در محیطهای صنعتی میشوند.
سینی جمعآوری مواد ریزشیافته: جمعآوری گرد و غبار و ذرات مواد حملشده
در بسیاری از کاربردهای صنعتی، مواد در حین انتقال دچار ریزش شده و تجمع این مواد در زیر تسمه میتواند باعث آلودگی محیط، افزایش استهلاک قطعات و کاهش بهرهوری سیستم شود. برای حل این مشکل، سینیهای جمعآوری مواد ریزشیافته در قسمتهای مختلف سیستم نصب میشوند.
- ✔ جلوگیری از تجمع مواد و افزایش تمیزی محیط کاری.
- ✔ کاهش خطر آسیب به رولیکها و سایر اجزای تشکیلدهنده نوار نقاله.
- ✔ امکان بازیافت و استفاده مجدد از مواد ریزشیافته در برخی کاربردهای صنعتی.
این سینیها علاوه بر افزایش کارایی سیستم، باعث کاهش هزینههای نظافت و نگهداری میشوند.
امیدواریم این مقاله برای شما مفید بوده باشد و اطلاعات لازم را در اختیار شما قرار داده باشد. شرکت امید عمران سهند تمامی اجزای تشکیلدهنده نوار نقاله را بهصورت جزئی و کلی با بالاترین کیفیت و استانداردهای صنعتی به فروش میرساند. اگر نیاز به تهیه هر نوع قطعهای از سیستمهای انتقال مواد یا قصد خرید نوار نقاله دارید، میتوانید با کارشناسان ما تماس گرفته و از مشاوره رایگان بهرهمند شوید. جهت دریافت اطلاعات بیشتر و خرید، با شماره 09351967545 تماس بگیرید.