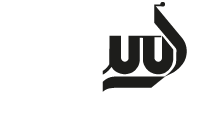
خط تولید عایق های قیری روکشدار
صنعت ساختمان و زیرساختهای عمرانی برای افزایش مقاومت سازهها در برابر عوامل محیطی به راهکارهای نوین و مؤثر نیاز دارد. یکی از این راهکارها، عایق های قیری روکشدار است که در حوزههای مختلف از جمله ایزولاسیون بام، دیوارها، تونلها و تأسیسات صنعتی کاربرد گستردهای دارد. کیفیت و دوام این عایقها به فناوری و تجهیزاتی که در خط تولید آنها به کار گرفته میشود، وابسته است. یک خط تولید پیشرفته میتواند تأثیر بسزایی در بهینهسازی فرایند تولید، افزایش کارایی محصول و کاهش هزینههای نگهداری در پروژههای ساختمانی و صنعتی داشته باشد.
در این مقاله، به بررسی عایق قیری روکشدار، ترکیب اصلی آن، تجهیزات مورد نیاز خط تولید، فرایند تولید، کاربردهای صنعتی و ساختمانی، اهمیت بهرهگیری از یک خط تولید حرفهای و تأثیر آن بر کیفیت و دوام محصول میپردازیم. همچنین، نقش نوع روکش در عملکرد نهایی عایق را بررسی خواهیم کرد.
- عایق قیری روکشدار چیست؟
- معرفی انواع عایق قیری روکشدار
- عایق قیری با روکش آلومینیومی
- عایق قیری با روکش سنگدانهای
- عایق قیری با روکش فویل مسی
- عایق قیری با روکش پلیاتیلن
- عایق قیری با روکش پلیپروپیلن
- عایق قیری با روکش فویل رنگی
- عایق قیری با روکش فویل طرحدار
- عایق قیری با روکش فویل شفاف
- عایق قیری با روکش فویل مات
- عایق قیری با روکش فویل براق
- عایق قیری با روکش مقاوم در برابر UV
- عایق قیری با روکش مقاوم در برابر حرارت
- عایق قیری با روکش مقاوم در برابر خوردگی
- عایق قیری با روکش مقاوم در برابر مواد شیمیایی
- تجهیزات مورد نیاز برای خط تولید عایق قیری روکشدار
- 1. میکسر نیدر (1800 لیتری)
- 2. دستگاه شیت رول
- 3. دستگاه لمینیشن
- 4. دستگاه امباس (Embossing)
- 5. نوار نقاله کولینگ و خشککن
- 6. هات ملت چسبزنی
- 7. دستگاه پینت (رنگپاشی)
- 8. درایر (خشککن نهایی)
- ۱۰. کاتر (برش نهایی)
- ۱۱. دایکات پرس آنلاین
- ۱۲. تابلو برق مرکزی با PLC
- جدول مشخصات فنی تجهیزات خط تولید عایق های قیری روکشدار
- فرآیند کلی تولید عایق های قیری روکشدار
- هزینههای سرمایهگذاری راهاندازی خط تولید عایق های قیری روکشدار
عایق قیری روکشدار چیست؟
عایق قیری روکشدار یکی از مهمترین محصولات مورد استفاده در صنعت ساختمان و زیرساختهای عمرانی است که برای جلوگیری از نفوذ آب و رطوبت به کار میرود. این عایق متشکل از قیری اصلاحشده بهعنوان بخش اصلی و یک روکش محافظ است که مقاومت آن را در برابر عوامل محیطی افزایش میدهد.
قیری که در این عایق استفاده میشود، معمولاً با مواد پلیمری یا الاستومری اصلاح شده تا چسبندگی، انعطافپذیری و مقاومت حرارتی آن بهبود یابد. روکش محافظ نیز میتواند از جنس فویل آلومینیومی، پلیاستر، الیاف شیشه یا مواد دیگر باشد که هرکدام تأثیر مستقیمی بر عملکرد نهایی عایق دارند.
کاربردهای صنعتی و ساختمانی عایق قیری روکشدار
عایق های قیری روکشدار به دلیل ویژگیهای مقاومتی خود، در بخشهای مختلفی مورد استفاده قرار میگیرند، از جمله:
- ایزولاسیون بامهای مسطح و شیبدار برای جلوگیری از نفوذ آب باران و برف
- عایقکاری دیوارهای زیرزمینی و پی ساختمانها برای محافظت از سازه در برابر رطوبت و نشست آب
- استفاده در تونلها، پلها و سازههای بتنی بهعنوان لایهای مقاوم در برابر رطوبت
- کاربرد در صنایع پتروشیمی و نفتی برای ایزولهسازی تجهیزات و جلوگیری از نشت مواد شیمیایی
معرفی انواع عایق قیری روکشدار
عایق های قیری روکشدار بر اساس نوع روکش و ویژگیهای آن در انواع مختلفی تولید میشوند که هرکدام کاربردهای خاصی در صنعت ساختمان و صنایع دیگر دارند. در این بخش، انواع عایق قیری روکشدار را با تمرکز بر ویژگیها و موارد استفاده بررسی خواهیم کرد.
عایق قیری با روکش آلومینیومی
این نوع عایق به دلیل مقاومت بالا در برابر اشعه UV و کاهش اثرات گرمایی یکی از بهترین گزینهها برای مناطق با تابش شدید خورشید است. فویل آلومینیومی، بهعنوان یک بازتابکننده حرارت عمل کرده و باعث کاهش جذب انرژی خورشیدی و کنترل دمای داخلی ساختمانها میشود. از این عایق معمولاً در سقفهای صنعتی، ساختمانهای تجاری و مکانهایی که در معرض نور مستقیم خورشید قرار دارند استفاده میشود.
عایق قیری با روکش سنگدانهای
این عایق با لایهای از سنگدانههای مقاوم پوشیده شده که استحکام مکانیکی آن را به میزان قابلتوجهی افزایش میدهد. روکش سنگدانهای باعث افزایش مقاومت در برابر سایش، ضربه و شرایط جوی نامساعد میشود. از این نوع عایق بیشتر در بامهای پرتردد، پارکینگهای طبقاتی و سطوحی که نیاز به محافظت مکانیکی بیشتری دارند استفاده میشود.
عایق قیری با روکش فویل مسی
این عایق دارای یک لایه نازک از فویل مسی است که به آن مقاومت بالا در برابر خوردگی، رطوبت و شرایط محیطی سخت میبخشد. مس یک ماده ضدزنگ و پایدار است که دوام عایق را در محیطهای مرطوب بهبود میبخشد. از این عایق عمدتاً در تأسیسات زیرزمینی، صنایع شیمیایی و محیطهایی با سطح بالای رطوبت و بخارات خورنده استفاده میشود.
عایق قیری با روکش پلیاتیلن
پلیاتیلن یک ماده ضدآب با انعطافپذیری بالا است که باعث افزایش قابلیت کشسانی و پایداری عایق قیری میشود. این نوع عایق در برابر ترکخوردگی و شکستگی مقاوم بوده و برای لولههای انتقال مایعات، سیستمهای آبیاری و تأسیسات زیرزمینی گزینهای ایدهآل محسوب میشود.
عایق قیری با روکش پلیپروپیلن
پلیپروپیلن باعث افزایش استحکام مکانیکی و مقاومت شیمیایی در عایق قیری میشود. این عایق در برابر مواد شیمیایی، حلالها و عوامل خورنده مقاوم است و در صنایع نفت و گاز، مخازن ذخیرهسازی و تأسیسات صنعتی مورد استفاده قرار میگیرد.
عایق قیری با روکش فویل رنگی
این نوع عایق علاوه بر مقاومت در برابر شرایط جوی، زیبایی بصری بیشتری نسبت به سایر انواع دارد. فویل رنگی امکان استفاده در طراحیهای معماری را فراهم کرده و در ساختمانهای نمایان، پروژههای دکوراتیو و مناطقی که ظاهر بصری اهمیت دارد بهکار میرود.
عایق قیری با روکش فویل طرحدار
این عایق با تنوع طرح و رنگ، علاوه بر ایجاد جلوه بصری، ویژگیهای فنی عایق قیری را حفظ میکند. انتخاب این نوع عایق در پروژههای ساختمانی خاص، نمای ساختمانها و دکوراسیون داخلی و خارجی متداول است.
عایق قیری با روکش فویل شفاف
فویل شفاف به این عایق امکان میدهد که تأثیر اشعه UV را کاهش داده و کنترل حرارتی بهتری ارائه دهد. این ویژگی باعث میشود که این نوع عایق در گلخانهها، سازههای خاص و ساختمانهایی که نیاز به نورپردازی کنترلشده دارند مورد استفاده قرار گیرد.
عایق قیری با روکش فویل مات
این عایق نور را کمتر منعکس کرده و میزان جذب حرارت را کاهش میدهد. از این رو، برای پروژههای خاص معماری و صنعتی که نیاز به کنترل دقیق دمای سطحی دارند مناسب است.
عایق قیری با روکش فویل براق
فویل براق با انعکاس نور بیشتر، میزان جذب گرما را کاهش داده و دمای سطحی عایق را پایین نگه میدارد. این ویژگی موجب میشود که از این عایق در سقفهای صنعتی و مناطق گرمسیری استفاده شود.
عایق قیری با روکش مقاوم در برابر UV
این عایق برای محافظت طولانیمدت در برابر اشعه خورشید طراحی شده است. مواد مقاوم در برابر UV باعث افزایش عمر مفید عایق و جلوگیری از تجزیه زودرس آن میشوند. این نوع عایق مناسب مناطق گرم و آفتابخیز است که در معرض تابش مستقیم خورشید قرار دارند.
عایق قیری با روکش مقاوم در برابر حرارت
این نوع عایق میتواند دمای بسیار بالا را تحمل کرده و عملکرد پایداری در شرایط سخت داشته باشد. ترکیبات مقاوم در برابر حرارت در این محصول باعث میشود که در صنایع پتروشیمی، پالایشگاهها و تأسیسات با دمای بالا به کار رود.
عایق قیری با روکش مقاوم در برابر خوردگی
این عایق دارای ویژگیهای ضدخوردگی بوده و در برابر اثرات مخرب مواد شیمیایی و رطوبت مقاوم است. استفاده از آن در خطوط لوله زیرزمینی، تأسیسات دریایی و صنایع شیمیایی رایج است.
عایق قیری با روکش مقاوم در برابر مواد شیمیایی
این عایق برای محافظت در برابر اسیدها، بازها و سایر مواد شیمیایی خورنده طراحی شده است. ترکیبات ویژهای که در ساخت آن استفاده شده، باعث میشود که برای مخازن شیمیایی، صنایع نفت و گاز و محیطهای صنعتی حساس بهترین انتخاب باشد.
انتخاب عایق قیری روکشدار مناسب به شرایط محیطی، نوع پروژه و نیازهای فنی بستگی دارد. استفاده از یک خط تولید پیشرفته و انتخاب روکش مناسب تأثیر مستقیمی بر دوام، عملکرد و بهرهوری عایقهای قیری خواهد داشت. در ادامه، به معرفی تجهیزات و بررسی فرآیند تولید این عایقها و تکنولوژیهای مورد استفاده در خط تولید خواهیم پرداخت.
تجهیزات مورد نیاز برای خط تولید عایق قیری روکشدار
برای تولید عایق های قیری روکشدار با کیفیت بالا و استاندارد، استفاده از دستگاههای پیشرفته و دقیق ضروری است. هر دستگاه در این خط تولید، نقش کلیدی در بهبود کیفیت، استحکام و دوام محصول نهایی دارد. در ادامه، تجهیزات مورد نیاز خط تولید معرفی شدهاند.
1. میکسر نیدر (1800 لیتری)
میکسر نیدر یکی از دستگاههای اصلی در فرآیند تولید عایق های قیری روکشدار است که وظیفه ترکیب و اصلاح قیر با پلیمرها و افزودنیهای خاص را بر عهده دارد. این فرآیند باعث افزایش انعطافپذیری، استحکام و مقاومت در برابر شرایط محیطی میشود. دستگاه دارای ظرفیت 1800 لیتر بوده و بدنه آن از فولاد مقاوم به حرارت ساخته شده است. کنترل دما تا 200 درجه سانتیگراد انجام میشود و از سیستم گرمایش روغن داغ برای پایداری حرارتی استفاده میکند.
2. دستگاه شیت رول
دستگاه شیت رول وظیفه تبدیل قیر اصلاحشده به ورقهای یکنواخت را دارد. این مرحله یکی از مهمترین بخشهای تولید عایق قیری است، زیرا ضخامت و یکپارچگی ورقها مستقیماً بر کیفیت نهایی محصول تأثیر میگذارد. این دستگاه میتواند ورقهایی با عرض 1.2 متر و ضخامت قابل تنظیم بین 2 تا 6 میلیمتر تولید کند. همچنین، با استفاده از غلطکهای فولادی مقاوم، یکنواختی ضخامت و کیفیت سطح ورق را تضمین میکند.
3. دستگاه لمینیشن
دستگاه لمینیشن برای اعمال روکشهای محافظ مانند فویل آلومینیوم، پلیاتیلن یا سنگدانهای روی ورقهای قیری استفاده میشود. این روکشها به افزایش مقاومت در برابر اشعه UV، رطوبت و ضربههای مکانیکی کمک میکنند. سرعت این دستگاه تا 25 متر در دقیقه است و فشار لمینیت بهصورت خودکار تنظیم میشود تا چسبندگی بین لایهها بهدرستی انجام شود.
4. دستگاه امباس (Embossing)
این دستگاه وظیفه ایجاد طرحهای برجسته روی سطح عایق را دارد. برجستهسازی باعث بهبود چسبندگی سطح، کاهش لغزندگی و افزایش استحکام مکانیکی عایق میشود. این دستگاه از غلطکهای فشار قوی با قابلیت تنظیم عمق برجستگی استفاده میکند و فشار اعمالی آن تا 60 بار قابل تنظیم است.
5. نوار نقاله کولینگ و خشککن
پس از اعمال روکش، عایق نیاز به خنککاری و تثبیت ساختاری دارد. این نوع نوار نقاله با استفاده از سیستم خنککننده آبی و هوایی، دمای ورقها را بهصورت یکنواخت کاهش داده و از تغییر شکل آنها جلوگیری میکند. طول این دستگاه معمولاً 10 متر است و برای ایجاد یکنواختی در کیفیت محصول، دقت بالایی در کنترل دما دارد.
6. هات ملت چسبزنی
دستگاه هات ملت چسبزنی برای اتصال لایههای مختلف عایق و چسباندن روکشهای محافظ مورد استفاده قرار میگیرد. این دستگاه قادر است چسب حرارتی را با دمای حداکثر 160 درجه سانتیگراد بهصورت یکنواخت روی سطح پخش کند تا اتصال قویتری بین لایههای عایق ایجاد شود.
7. دستگاه پینت (رنگپاشی)
دستگاه پینت برای اعمال رنگ و پوششهای مقاوم روی سطح عایق به کار میرود. این پوششها میتوانند مقاومت محصول را در برابر نور خورشید، مواد شیمیایی و شرایط جوی نامساعد افزایش دهند. این دستگاه دارای سیستم اسپری رنگ با فشار 4 بار است که میتواند میزان رنگ پاشیدهشده را بهصورت دقیق تنظیم کند.
8. درایر (خشککن نهایی)
پس از انجام فرآیندهای لمینیت و رنگپاشی، عایق باید بهطور کامل خشک و تثبیت شود. این دستگاه با استفاده از سیستم گردش هوای گرم و کنترل دمای دیجیتال، فرآیند خشکشدن را تسریع کرده و کیفیت نهایی عایق را تضمین میکند. دمای کاری این دستگاه بین 50 تا 130 درجه سانتیگراد قابل تنظیم است.
۱۰. کاتر (برش نهایی)
در مرحله آخر، ورقهای عایق باید به ابعاد مشخص و استاندارد برش داده شوند. این کار توسط دستگاه کاتر صنعتی انجام میشود که دارای دقت برش ±0.1 میلیمتر بوده و میتواند با سرعت 15 متر در دقیقه ورقها را برش دهد.
۱۱. دایکات پرس آنلاین
برخی عایقهای قیری نیاز به برش قالبی و تولید اشکال خاص دارند که این کار توسط دستگاه دایکات پرس آنلاین انجام میشود. این دستگاه دارای فشار پرس 100 تن است و میتواند برشهای بسیار دقیق و یکنواختی ایجاد کند.
۱۲. تابلو برق مرکزی با PLC
تمامی فرآیندهای خط تولید باید بهصورت هوشمند و اتوماتیک کنترل شوند. این کار توسط تابلو برق مرکزی با سیستم PLC صنعتی انجام میشود که امکان نظارت لحظهای و کاهش مصرف انرژی را فراهم میکند. این سیستم باعث میشود خط تولید با کمترین خطا و بالاترین بهرهوری کار کند.
خط تولید عایق های قیری روکشدار شامل تجهیزات پیشرفتهای برای آمادهسازی، تولید، روکشگذاری، خشککردن، برش و کنترل کیفیت است. هر یک از این دستگاهها، نقشی کلیدی در بهبود کیفیت و عملکرد نهایی محصول دارند. شرکت امید عمران سهند تمامی این تجهیزات را با بالاترین کیفیت طراحی، تولید و راهاندازی میکند.
جدول مشخصات فنی تجهیزات خط تولید عایق های قیری روکشدار
جدول زیر، ویژگیهای کلیدی، ظرفیت، جنس بدنه و سایر مشخصات فنی تجهیزات را نمایش میدهد تا دید جامعی از قابلیتهای این دستگاهها ارائه شود. این اطلاعات برای راهاندازی و مدیریت خط تولید، انتخاب تجهیزات مناسب و بهینهسازی فرآیند تولید بسیار کاربردی است.
نام دستگاه | کاربرد | ظرفیت | جنس بدنه | کنترل دما | ویژگیهای خاص |
---|---|---|---|---|---|
میکسر نیدر | ترکیب و اصلاح قیر، پلیمر و افزودنیها | 1800 لیتر | فولادی مقاوم | تا 200°C | سیستم گرمایش روغن داغ |
دستگاه شیت رول | تولید ورقهای قیری با ضخامت یکنواخت | عرض 1.2 متر | فولاد سختکاری شده | – | تنظیم ضخامت 2 تا 6 میلیمتر |
دستگاه لمینیشن | اعمال روکشهای محافظ | – | استیل صنعتی | تنظیم خودکار | سرعت لمینیت تا 25 متر در دقیقه |
دستگاه امباس | ایجاد برجستگیهای سطحی برای بهبود چسبندگی | – | فولاد سختکاری شده | تا 180°C | عمق برجستگی قابل تنظیم، فشار 60 بار |
دستگاه روکشگذاری | افزودن پوششهای مقاوم در برابر UV و رطوبت | – | استیل صنعتی | تنظیم خودکار | پاشش یکنواخت مواد |
کانوایر کولینگ و خشککن | خنککاری و تثبیت ورقهای قیری | طول 10 متر | فولاد صنعتی | – | سیستم خنککننده آبی و هوایی |
هات ملت چسبزنی | اتصال لایههای روکش با چسب حرارتی | مخزن 50 لیتر | استیل مقاوم | تا 160°C | توزیع یکنواخت چسب |
دستگاه پینت | رنگپاشی برای افزایش مقاومت سطحی | – | فولاد صنعتی | تا 90°C | فشار رنگپاشی 4 بار، تنظیم میزان رنگ |
درایر (خشککن نهایی) | خشککردن و تثبیت نهایی پوششها | – | استیل مقاوم | 50-130°C | کنترل دیجیتال دما |
کاتر (برش نهایی) | برش ورقهای عایق در اندازه استاندارد | – | فولاد صنعتی | – | دقت برش ±0.1 میلیمتر، سرعت 15 متر در دقیقه |
دایکات پرس آنلاین | برش قالبی برای تولید اشکال خاص | – | فولاد سختکاری شده | – | فشار پرس 100 تن، برش قالبی دقیق |
تابلو برق مرکزی با PLC | کنترل هوشمند خط تولید و نظارت | – | – | تنظیم اتوماتیک | سیستم PLC صنعتی، کاهش مصرف انرژی |
فرآیند کلی تولید عایق های قیری روکشدار
تولید عایق قیری با روکش یک فرآیند مهندسیشده و دقیق است که شامل مراحل متوالی از انتخاب مواد اولیه تا بستهبندی نهایی میشود. در این فرآیند، هر گام بهگونهای طراحی شده است که کیفیت، دوام و استانداردهای بینالمللی محصول حفظ شود. شرکت امید عمران سهند با بهینهسازی این فرآیند، توانسته است خط تولیدی با حداقل ضایعات، حداکثر بازدهی و محصولاتی با عملکرد عالی ارائه دهد.
در ادامه، مراحل تولید عایق های قیری روکشدار بهصورت گامبهگام و دقیق توضیح داده شده است.
۱. انتخاب مواد اولیه و آمادهسازی قیر
مواد اولیه باکیفیت، پایه و اساس تولید عایقهای قیری مقاوم و استاندارد هستند. در این مرحله، قیر مناسب با درجه نفوذ و گرانروی مشخص انتخاب میشود. قیر مورد استفاده معمولاً از نوع اصلاحشده یا پالایشگاهی است که دارای چسبندگی بالا و مقاومت حرارتی مناسب باشد. جهت کسب اطلاعات بیشتر در خصوص انواع قیر، مقاله قیر چیست؟ را مطالعه کنید.
پس از انتخاب قیر، فرآیند ذوب و آمادهسازی در میکسر نیدر صنعتی انجام میشود. این کار باعث میشود که ناخالصیهای موجود در قیر حذف شده و ویسکوزیته (غلظت) آن به سطح استاندارد برسد. در این مرحله، دما بین 150 تا 180 درجه سانتیگراد تنظیم میشود تا قیر بهصورت یکنواخت آماده ترکیب با افزودنیهای دیگر شود.
۲. افزودن اصلاحکنندهها و پایدارکنندهها
برای افزایش خواص مکانیکی و فیزیکی قیر، اصلاحکنندهها و پایدارکنندهها به آن اضافه میشوند. این مواد شامل ترکیبات پلیمری (مانند SBS، APP)، الاستومرها، آنتیاکسیدانها و پایدارکنندههای UV هستند که باعث افزایش مقاومت حرارتی، انعطافپذیری و دوام عایق میشوند.
میکسر نیدر با استفاده از سیستم همزنهای قدرتمند و کنترل دمای دیجیتال، این مواد را بهصورت یکنواخت در قیر توزیع میکند. این فرآیند معمولاً بین 30 تا 60 دقیقه طول میکشد و باعث میشود که قیر بهصورت کاملاً اصلاحشده و پایدار برای مراحل بعدی آماده شود.
۳. فرآیند گرمادهی و اعمال روکش موردنظر
پس از آمادهسازی قیر اصلاحشده، نوبت به فرمدهی و اعمال روکشهای محافظ میرسد. در این مرحله، مواد وارد دستگاه شیت رول میشوند تا به ورقهایی با ضخامت یکنواخت تبدیل شوند.
✅ در ادامه، ورقهای قیری از دستگاه لمینیشن عبور داده میشوند تا لایههای محافظ مانند فویل آلومینیومی، پلیاتیلن، الیاف شیشه یا سنگدانهای روی آنها اعمال شود. روکشها بسته به نوع کاربرد عایق، انتخاب شده و روی سطح عایق با دقت چسبانده میشوند.
✅ سپس، عایق وارد دستگاه امباس (Embossing) میشود تا بافت و الگوی برجستهای روی سطح آن ایجاد شود. این کار باعث افزایش چسبندگی، کاهش لغزندگی و بهبود مقاومت مکانیکی عایق میشود.
✅ برای افزایش دوام، برخی عایقها تحت پوششهای محافظ اضافی مانند پوششهای مقاوم در برابر UV یا رنگهای مخصوص صنعتی قرار میگیرند. این کار توسط دستگاه روکشگذاری و رنگپاشی صنعتی انجام میشود.
✅ در اخر نیز، عایقها از مسیر کانوایر کولینگ و خشککن عبور میکنند تا فرآیند خنککاری و تثبیت نهایی انجام شود. این مرحله باعث کاهش تنشهای داخلی عایق شده و از تغییر شکل آن جلوگیری میکند.
۴. کنترل کیفیت و تستهای فنی
پس از تکمیل فرآیند تولید عایق های قیری روکشدار، کنترل کیفیت یکی از مهمترین بخشها در تضمین استانداردهای محصول نهایی است. در این مرحله، نمونههایی از عایقها تحت آزمایشهای مختلف قرار میگیرند، از جمله:
- آزمون چسبندگی روکش: بررسی میزان چسبندگی لایههای محافظ به سطح قیری
- تست انعطافپذیری: بررسی مقاومت عایق در برابر تغییر شکل و خمشدگی
- آزمون مقاومت حرارتی: ارزیابی پایداری عایق در برابر دماهای بالا و تابش مستقیم آفتاب
- آزمون مقاومت در برابر نفوذ آب: اطمینان از ضدآب بودن و جلوگیری از نشت رطوبت
در صورتی که محصولی در این تستها موفق نباشد، به مرحله اصلاح و بازبینی برمیگردد.
۵. برش، بستهبندی و آمادهسازی برای عرضه به بازار
پس از تأیید کیفیت محصول، عایقها برش داده شده و بستهبندی میشوند. این مرحله با استفاده از دستگاههای کاتر صنعتی و دایکات پرس آنلاین انجام میشود که امکان برشهای دقیق و سفارشی را فراهم میکنند.
- ✅ عایقها بهصورت رول یا ورقهای برشخورده در ابعاد مختلف بستهبندی میشوند.
- ✅ برای جلوگیری از آسیبدیدگی، بستهبندیها شامل محافظ پلاستیکی یا لفافهای مخصوص صنعتی هستند.
- ✅ تمامی محصولات دارای برچسب مشخصات فنی، استانداردهای تولید و اطلاعات برند تولیدکننده هستند.
فرآیند تولید عایق قیری روکشدار شامل ۵ گام اساسی است:
- 1️⃣ انتخاب مواد اولیه و آمادهسازی قیر – استفاده از قیر اصلاحشده با ترکیبات پایدارکننده
- 2️⃣ افزودن اصلاحکنندهها و پایدارکنندهها – ترکیب قیر با پلیمرها برای بهبود خواص فیزیکی
- 3️⃣ فرآیند گرمادهی و اعمال روکش – لمینیت، امباس و تثبیت نهایی عایق
- 4️⃣ کنترل کیفیت و تستهای فنی – بررسی چسبندگی، مقاومت حرارتی، انعطافپذیری و نفوذ آب
- 5️⃣ برش، بستهبندی و آمادهسازی برای عرضه – ارائه محصول نهایی در ابعاد استاندارد
هزینههای سرمایهگذاری راهاندازی خط تولید عایق های قیری روکشدار
در این بخش، به بررسی هزینههای مورد نیاز برای راهاندازی خط تولید عایق های قیری روکشدار میپردازیم تا سرمایهگذاران دید واضحی از میزان سرمایه اولیه، هزینههای جاری و نکات کلیدی این کسبوکار داشته باشند. شناخت دقیق این هزینهها به تصمیمگیری بهتر و برنامهریزی مالی صحیح کمک میکند.
1. هزینه خرید و نصب ماشینآلات تولید عایق های قیری روکشدار
برای راهاندازی یک خط تولید عایق قیری با روکش استاندارد، نیاز به تجهیزات و ماشینآلات تخصصی است. هزینههای تقریبی برای خرید و نصب این تجهیزات به شرح زیر است:
این بخش شامل تمامی تجهیزات موردنیاز برای راهاندازی خط تولید است. دستگاههای تولید، لمینیشن، برش، خشککن و سیستمهای کنترلی بخش مهمی از این سرمایهگذاری را تشکیل میدهند.
نام دستگاه | تعداد | هزینه تقریبی (تومان) |
---|---|---|
میکسر نیدر (1800 لیتری) | 1 | ۱,۵۰۰,۰۰۰,۰۰۰ |
دستگاه شیت رول | 1 | ۱,۲۰۰,۰۰۰,۰۰۰ |
دستگاه لمینیشن | 1 | ۱,۰۰۰,۰۰۰,۰۰۰ |
دستگاه امباس | 1 | ۸۰۰,۰۰۰,۰۰۰ |
کانوایر کولینگ و خشککن | 1 | ۹۰۰,۰۰۰,۰۰۰ |
هات ملت چسبزنی | 1 | ۷۰۰,۰۰۰,۰۰۰ |
دستگاه پینت (رنگپاشی) | 1 | ۶۰۰,۰۰۰,۰۰۰ |
درایر (خشککن نهایی) | 1 | ۸۵۰,۰۰۰,۰۰۰ |
کاتر (برش نهایی) | 1 | ۵۵۰,۰۰۰,۰۰۰ |
دایکات پرس آنلاین | 1 | ۱,۰۰۰,۰۰۰,۰۰۰ |
تابلو برق مرکزی با PLC | 1 | ۴۵۰,۰۰۰,۰۰۰ |
مجموع هزینه ماشینآلات | – | ۹,۵۵۰,۰۰۰,۰۰۰ |
2. میزان مواد اولیه موردنیاز
مواد اولیه اصلی شامل قیر، پلیمرها، روکشهای محافظ و افزودنیهای شیمیایی است. هزینههای ماهیانه مواد اولیه بسته به ظرفیت تولید و قیمتهای بازار متغیر است، اما بهطور متوسط میتوان مبلغی در حدود ۵۰۰,۰۰۰,۰۰۰ تومان را در نظر گرفت.
نوع ماده اولیه | میزان مصرف ماهانه | هزینه تقریبی (تومان) |
---|---|---|
قیر اصلاحشده | ۵۰ تن | ۳۰۰,۰۰۰,۰۰۰ |
پلیمرهای اصلاحکننده | ۱۰ تن | ۱۰۰,۰۰۰,۰۰۰ |
روکشهای محافظ | ۲۰۰۰ مترمربع | ۵۰,۰۰۰,۰۰۰ |
سایر افزودنیها | ۵ تن | ۵۰,۰۰۰,۰۰۰ |
مجموع هزینه ماهانه | – | ۵۰۰,۰۰۰,۰۰۰ |
استفاده از مواد اولیه باکیفیت، تأثیر مستقیم بر دوام و عملکرد نهایی عایقهای قیری دارد.
3. نیروی انسانی و فضای کارگاهی
- نیروی انسانی: برای بهرهبرداری از خط تولید، نیاز به پرسنل متخصص و کارگران ماهر است. هزینههای حقوق و دستمزد ماهیانه برای یک تیم ۱۵ نفره حدود ۲۲۵,۰۰۰,۰۰۰ تومان برآورد میشود.
- فضای کارگاهی: اجاره یا خرید فضای مناسب برای کارخانه بسته به موقعیت جغرافیایی و متراژ موردنیاز متفاوت است. بهعنوان مثال، اجاره ماهیانه یک فضای ۱۰۰۰ مترمربعی در مناطق صنعتی ممکن است حدود ۱۰۰,۰۰۰,۰۰۰ تومان باشد.
بخش | مقدار/تعداد | هزینه ماهانه (تومان) |
---|---|---|
تعداد نیروی انسانی | ۱۵ نفر | ۲۲۵,۰۰۰,۰۰۰ |
اجاره فضای کارگاهی (۱۰۰۰ مترمربع) | – | ۱۰۰,۰۰۰,۰۰۰ |
مجموع هزینه ماهانه | – | ۳۲۵,۰۰۰,۰۰۰ |
بهرهگیری از نیروی انسانی متخصص و فضای کارگاهی مناسب، تأثیر زیادی در افزایش بهرهوری و کاهش هزینههای تولید دارد.
4. هزینههای نگهداری و بهرهبرداری
هزینههای جاری شامل نگهداری ماشینآلات، مصرف انرژی، آب، برق و سایر هزینههای عملیاتی است که ماهیانه حدود ۱۵۰,۰۰۰,۰۰۰ تومان تخمین زده میشود.
بخش هزینهای | هزینه ماهانه (تومان) |
---|---|
نگهداری ماشینآلات | ۵۰,۰۰۰,۰۰۰ |
هزینه برق و انرژی | ۷۰,۰۰۰,۰۰۰ |
هزینههای متفرقه | ۳۰,۰۰۰,۰۰۰ |
مجموع هزینه ماهانه | ۱۵۰,۰۰۰,۰۰۰ |
با استفاده از فناوریهای پیشرفته، مصرف انرژی و هزینههای نگهداری تا حد زیادی کاهش مییابد.
مزایای سرمایهگذاری در این صنعت
- ✔ بازار رو به رشد و تقاضای بالا: با توجه به توسعه ساختوساز و نیاز به عایقهای باکیفیت، تقاضا برای عایقهای قیری روکشدار در حال افزایش است. همچنین، کشورهای همسایه مانند عراق، افغانستان و ترکیه بازارهای مناسبی برای صادرات این محصول محسوب میشوند.
- ✔ دوره بازگشت سرمایه کوتاه: با در نظر گرفتن سود ناخالص ماهیانه حدود ۳۰۰,۰۰۰,۰۰۰ تومان، دوره بازگشت سرمایه اولیه تقریباً ۳ سال خواهد بود که نشاندهنده جذابیت اقتصادی این سرمایهگذاری است.
- ✔ امکان صادرات به کشورهای همسایه: کیفیت بالای محصولات تولیدی و نزدیکی جغرافیایی، فرصتهای مناسبی برای صادرات به کشورهای همسایه فراهم میکند که میتواند به افزایش درآمد و توسعه کسبوکار منجر شود.
شرکت امید عمران سهند با تجربه و تخصص در این حوزه، آماده ارائه راهکارهای مقرونبهصرفه و مشاورههای تخصصی برای سرمایهگذاران علاقهمند به راهاندازی خط تولید عایق قیری روکشدار است. جهت دریافت مشاوره و استعلام قیمت با شماره 09351967545 تماس بگیرید.