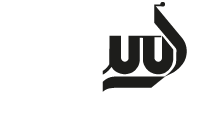
پلیمریزاسیون چیست؟ راهنمای جامع انواع، فرایندها و کاربردهای صنعتی
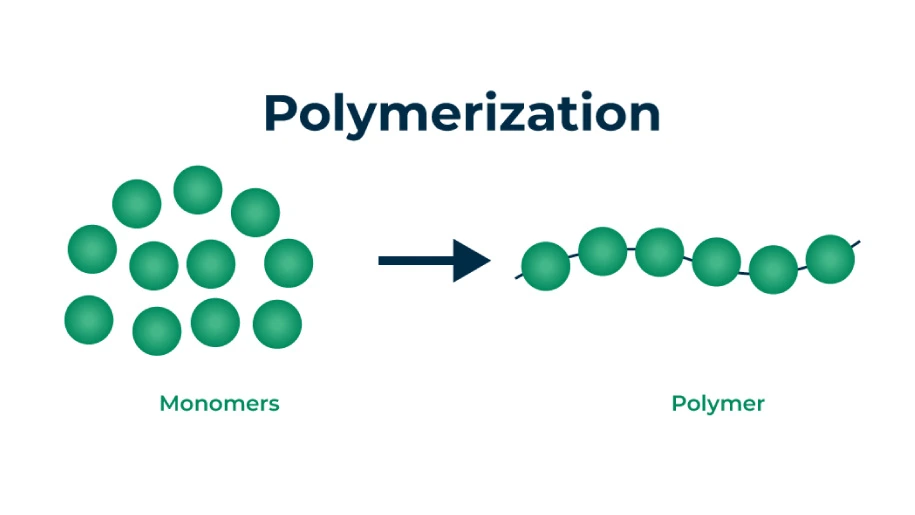
تولید صنعتی موادی مانند پلاستیکها، رزینها، پوششها و چسبها، مستقیماً به یک فرایند کلیدی به نام پلیمریزاسیون (Polymerization) وابسته است. در این فرایند، مواد اولیه (که در صنعت به آنها مونومر گفته میشود) تحت شرایط کنترلشده دما، فشار و کاتالیست، به محصول نهایی با خواص مشخص (یعنی پلیمر) تبدیل میشوند.
هدف اصلی در هر واحد تولیدی، کنترل دقیق این فرایند برای دستیابی به مشخصات فنی مورد نظر در محصول نهایی است. پارامترهایی مانند وزن مولکولی، ویسکوزیته، استحکام و پایداری حرارتی، همگی نتیجه مستقیم کیفیت اجرای فرایند پلیمریزاسیون هستند. بنابراین، تسلط بر این فرایند برای هر متخصص فنی در این صنایع، یک ضرورت است.
این راهنما یک دید کلی و کاربردی برای متخصصان فنی و صنعتی ارائه میدهد. در این متن، ما ابتدا به مکانیزمهای اصلی واکنش نگاهی میاندازیم، سپس روشهای مختلف اجرای این فرایند در صنعت را بررسی میکنیم. در ادامه، تجهیزات کلیدی یعنی انواع راکتورهای صنعتی را معرفی کرده و پارامترهای حیاتی برای کنترل فرایند و تضمین کیفیت محصول را شرح میدهیم.
مفاهیم بنیادی پلیمریزاسیون
پیش از ورود به جزئیات فرایندها و تجهیزات، لازم است تا تعاریف و واژگان کلیدی که در صنعت به صورت روزمره استفاده میشوند، به طور دقیق مشخص شوند. این مفاهیم، زبان مشترک میان تمام متخصصان این حوزه است.
تعریف مونومر، پلیمر، هموپلیمر و کوپلیمر
- مونومر: واحد سازنده یا ماده اولیه اصلی در فرایند پلیمریزاسیون است. در صنعت، موادی مانند اتیلن، پروپیلن، وینیل کلراید و استایرن، مثالهایی از مونومرهای پرکاربرد هستند که به عنوان خوراک وارد راکتور میشوند.
- پلیمر: محصول نهایی فرایند است که از اتصال تعداد زیادی واحد مونومری به یکدیگر تشکیل میشود. خواص نهایی محصولی مانند یک قطعه پلاستیکی، یک نوع چسب یا یک فیبر نساجی، مستقیماً به ساختار این زنجیرههای پلیمری بستگی دارد.
- هموپلیمر: پلیمری است که تنها از یک نوع واحد مونومری ساخته شده باشد. برای مثال، پلیپروپیلن (PP) یک هموپلیمر است، زیرا زنجیرههای آن صرفاً از اتصال مونومرهای پروپیلن به وجود آمدهاند.
- کوپلیمر: یک تکنیک بسیار مهم در صنعت برای دستیابی به خواص جدید است. کوپلیمر پلیمری است که از اتصال دو یا چند نوع مونومر مختلف ساخته میشود. هدف از این کار، ترکیب کردن خواص مطلوب چند ماده در یک محصول واحد است. برای مثال، در تولید لاستیک SBR، با ترکیب مونومرهای استایرن و بوتادین، محصولی همزمان مقاوم و انعطافپذیر به دست میآید.
درجه پلیمریزاسیون (DP) و ارتباط آن با وزن مولکولی
درجه پلیمریزاسیون (Degree of Polymerization, DP) یک پارامتر فنی است که متوسط تعداد واحدهای مونومری در یک زنجیره پلیمری را نشان میدهد. این عدد ارتباط مستقیمی با وزن مولکولی (Molecular Weight) پلیمر دارد. در محیط صنعتی، کنترل وزن مولکولی یکی از اهداف اصلی در طراحی فرایند است، زیرا این پارامتر مستقیماً بر خواص فیزیکی و مکانیکی محصول نهایی تأثیر میگذارد:
- وزن مولکولی بالاتر: منجر به افزایش استحکام کششی، مقاومت به ضربه و سختی میشود، اما ویسکوزیته پلیمر مذاب را نیز افزایش میدهد که این امر فرایند شکلدهی را دشوارتر میکند.
- وزن مولکولی پایینتر: باعث کاهش ویسکوزیته و تسهیل فرایندپذیری میشود اما به قیمت کاهش خواص مکانیکی تمام خواهد شد.
ساختارهای پلیمری: خطی، شاخهای و شبکهای
نحوه اتصال زنجیرههای پلیمری به یکدیگر، ساختار کلی آن را تعیین میکند:
- ساختار خطی: زنجیرهها به صورت ساده و پشت سر هم قرار گرفتهاند و منجر به تولید پلیمرهایی با چگالی بالاتر میشوند، مانند پلیاتیلن سنگین (HDPE).
- ساختار شاخهای: یک زنجیره اصلی با شاخههایی کوتاهتر وجود دارد که محصولی با چگالی کمتر و انعطافپذیری بیشتر تولید میکند، مانند پلیاتیلن سبک (LDPE).
- ساختار شبکهای: زنجیرهها از طریق پیوندهای شیمیایی دائمی به یکدیگر متصل شده و یک شبکه سهبعدی را تشکیل میدهają. این ساختار، اساس تولید ترموستها (Thermosets) مانند رزینهای اپوکسی است که پس از شکلگیری دیگر ذوب نمیشوند و مقاومت حرارتی و شیمیایی بالایی دارند. این مواد در مقابل ترموپلاستیکها (Thermoplastics) قرار میگیرند که قابلیت ذوب و شکلدهی مجدد دارند.
تحلیل مکانیزمهای واکنش پلیمریزاسیون
پس از آشنایی با واژگان پایه، قدم بعدی درک دو مسیر یا مکانیزم اصلی است که واکنشهای پلیمریزاسیون در سطح مولکولی طی میکنند. انتخاب هر یک از این مکانیزمها، تاثیر مستقیمی بر سینتیک واکنش، نحوه کنترل فرایند و ساختار نهایی پلیمر دارد.
پلیمریزاسیون زنجیرهای (افزایشی)
در این مکانیزم، واکنش از طریق یک “مرکز فعال” (مانند یک رادیکال آزاد یا یون) آغاز میشود. این مرکز فعال به سرعت و به صورت متوالی، هزاران واحد مونومر را یکی پس از دیگری به خود اضافه میکند و یک زنجیره بلند را در مدت زمان بسیار کوتاهی (اغلب در کسری از ثانیه تا چند ثانیه) به وجود میآورد. به همین دلیل، در هر لحظه از فرایند، مخلوط واکنش شامل مونومرهای مصرف نشده، تعداد کمی زنجیره در حال رشد و زنجیرههای کامل شده با وزن مولکولی بالا است. این مکانیزم اساس تولید بسیاری از پلیمرهای پرمصرف مانند پلیاتیلن، پلیپروپیلن و پلیوینیل کلراید است.
مراحل اصلی این واکنش عبارتند از:
- شروع: ایجاد مرکز فعال از طریق یک آغازگر.
- انتشار: رشد سریع زنجیره با اضافه شدن پیدرپی مونومرها.
- پایان: غیرفعال شدن مرکز فعال و توقف رشد زنجیره.
پلیمریزاسیون مرحلهای (تراکمی)
در مقابل مکانیزم زنجیرهای، در این روش هر مونومر یا هر قطعه از زنجیره میتواند با دیگری واکنش دهد. واکنش به صورت آرام و مرحله به مرحله پیش میرود. ابتدا مونومرها به هم متصل شده و قطعات کوچک دوتایی (دایمر) و سهتایی (ترایمر) را میسازند. سپس این قطعات کوچک با هم واکنش داده و زنجیرههای بزرگتر را به وجود میآورند.
یک تفاوت کلیدی و صنعتی در این مکانیزم این است که وزن مولکولی بالا تنها در مراحل پایانی واکنش (معمولاً در درصدهای تبدیل بالای ۹۹٪) حاصل میشود. همچنین در بسیاری از این واکنشها، به ازای هر پیوند جدید، یک مولکول کوچک مانند آب به عنوان محصول جانبی تولید میشود که باید از محیط واکنش خارج گردد. این مکانیزم برای تولید پلیمرهایی مانند پلیاسترها (Polyesters, PET)، پلیآمیدها (Polyamides, Nylon) و پلیکربناتها (Polycarbonates, PC) به کار میرود.
جدول مقایسه فنی دو مکانیزم
مشخصه فنی | پلیمریزاسیون زنجیرهای (افزایشی) | پلیمریزاسیون مرحلهای (تراکمی) |
سرعت رشد زنجیره | بسیار سریع | آرام و مرحله به مرحله |
مصرف مونومر | در ابتدای واکنش به سرعت مصرف میشود. | به تدریج در تمام طول واکنش مصرف میشود. |
دستیابی به وزن مولکولی بالا | از همان ابتدای واکنش حاصل میشود. | تنها در انتهای واکنش (درصد تبدیل بالا) |
محصول جانبی کوچک | معمولاً ندارد. | معمولاً دارد (مانند آب). |
مثالهای صنعتی | PE, PVC, PP, PS | PET, Nylon, PC, رزینهای اپوکسی |
طبقهبندی فرایندهای صنعتی پلیمریزاسیون
پس از درک مکانیزمهای شیمیایی، یک مهندس فرایند باید تصمیم بگیرد که واکنش را در چه محیطی و تحت چه شرایطی در مقیاس صنعتی اجرا کند. انتخاب روش یا فرایند صنعتی، یک تصمیم کلیدی است که بر اساس عواملی مانند نحوه انتقال حرارت، ویسکوزیته سیستم، هزینههای جداسازی و کاربرد نهایی محصول انجام میشود. در ادامه، چهار فرایند اصلی مورد استفاده در صنعت را بررسی میکنیم.
فرایند پلیمریزاسیون تودهای
در این روش، واکنش در خالصترین حالت ممکن انجام میشود؛ یعنی مخلوط واکنش فقط شامل مونومر و مقدار کمی آغازگر است و هیچگونه حلال یا واسطهای وجود ندارد. مزیت اصلی این روش، دستیابی به پلیمری با خلوص بسیار بالاست. با این حال، چالش فنی اصلی در این فرایند، کنترل حرارت است. واکنشهای پلیمریزاسیون به شدت گرمازا هستند و با پیشرفت واکنش، ویسکوزیته سیستم به شدت افزایش مییابد. این افزایش ویسکوزیته، انتقال حرارت از داخل توده واکنش به دیواره راکتور را بسیار دشوار میکند و میتواند منجر به ایجاد نقاط داغ (Hotspots) و حتی فرار واکنش (Runaway reaction) شود. این چالشها، طراحی راکتور را به یک موضوع بحرانی در این فرایند تبدیل میکند.
فرایند پلیمریزاسیون محلولی
برای غلبه بر مشکل کنترل دما و ویسکوزیته، در این روش مونومر در یک حلال مناسب که در واکنش شرکت نمیکند، حل میشود. حضور حلال باعث کاهش ویسکوزیته کلی سیستم شده و به عنوان یک جاذب حرارت، کنترل دما را بسیار آسانتر میکند. چالش اصلی این فرایند، جنبه اقتصادی و فنی جداسازی پلیمر از حلال در انتهای واکنش است. این مرحله نیازمند تجهیزات جانبی برای حذف و احتمالاً بازیافت حلال است که به پیچیدگی و هزینه کلی فرایند میافزاید.
فرایند پلیمریزاسیون سوسپانسیونی
در این فرایند که بر پایه آب است، قطرات کوچک مونومر (که در آب نامحلول هستند) با استفاده از یک عامل پایدارکننده، در محیط آبی به صورت سوسپانسیون معلق نگه داشته میشوند. واکنش پلیمریزاسیون در داخل هر یک از این قطرات مجزا رخ میدهد. آب به عنوان یک محیط انتقال حرارت عالی و ارزان، به طور موثری حرارت واکنش را دفع کرده و کنترل دما را بسیار ساده میکند. چالش مهندسی در این روش، حفظ پایداری سوسپانسیون و جلوگیری از به هم چسبیدن قطرات است. طراحی سیستم همزن (Agitation) و انتخاب پایدارکننده مناسب برای دستیابی به توزیع اندازه ذرات یکنواخت، از اهمیت بالایی برخوردار است.
فرایند پلیمریزاسیون امولسیونی
این روش نیز بر پایه آب است اما مکانیزم پیچیدهتری دارد. در اینجا، مونومر با استفاده از یک عامل فعال سطحی (سورفکتانت)، در آب به صورت یک امولسیون پایدار درمیآید و واکنش در ساختارهای بسیار ریزی به نام میسل (Micelle) انجام میشود. مزیت بزرگ این روش، دستیابی همزمان به سرعت واکنش بالا و وزن مولکولی بالا است که در سایر فرایندها به سختی ممکن است. کنترل دما نیز به دلیل حضور آب، بسیار مطلوب است. چالش اصلی، فرمولاسیون پیچیده سیستم و نیاز به جداسازی پلیمر نهایی از آب و سایر افزودنیها (مانند سورفکتانت) در انتهای فرایند است.
آشنایی با انواع راکتورهای صنعتی پلیمریزاسیون
انتخاب صحیح راکتور، مهمترین تصمیم فنی پس از مشخص شدن فرایند است. هر راکتور برای پاسخ به چالشهای مهندسی خاصی (مانند انتقال حرارت، مدیریت ویسکوزیته یا حذف محصولات جانبی) طراحی شده است. در ادامه، به معرفی دستهای از راکتورهای کلیدی که در صنعت پلیمریزاسیون کاربرد گسترده دارند، میپردازیم.
کانتینوز راکتور | تویین اسکرو راکتور | راکتیو اکستروژن
این تجهیز، یک سیستم پیشرفته و بدون حلال برای انجام پلیمریزاسیون است. در این راکتور، مواد اولیه به صورت پیوسته توسط دو مارپیچ درهمتنیده به جلو رانده شده و همزمان عملیات میکس، انتقال حرارت و واکنش روی آنها انجام میشود. این روش برای فرایندهای سریع و تولیداتی که نیاز به کنترل دقیق پروفایل دما و میکس شدید دارند، ایدهآل است.
کاربردهای صنعتی: تولید پلیمرهای مهندسی، کامپاندهای پلیمری و فرایندهای پلیمریزاسیون در فاز مذاب. [برای آشنایی با راهحلهای ما در این زمینه، با 09142178355 تماس بگیرید.]
راکتور تانکی | راکتور مخزنی
این نوع راکتور، پرکاربردترین و شناختهشدهترین تجهیز در صنایع شیمیایی است. این راکتورها اساساً یک تانک مجهز به سیستم همزن، سیستم کنترل دما (معمولاً یک ژاکت حرارتی) و ورودی و خروجیهای لازم هستند. به دلیل انعطافپذیری بالا، برای فرایندهای مختلفی از جمله سوسپانسیونی، امولسیونی و محلولی کاربرد دارند.
کاربردهای صنعتی: فرایندهای سوسپانسیونی، امولسیونی، محلولی و بسیاری از واکنشهای ناپیوسته (Batch). ما در امید عمران سهند، طیف گستردهای از این راکتورها را بر اساس نیاز شما طراحی و تولید میکنیم.
راکتور بالک | نیدر راکتور
این نوع راکتور برای چالشبرانگیزترین نوع پلیمریزاسیون، یعنی فرایندهای با ویسکوزیته بسیار بالا، طراحی شده است. زمانی که مخلوط واکنش به شکل یک توده خمیری یا مذاب بسیار غلیظ درمیآید، همزنهای معمولی کارایی خود را از دست میدهند. این راکتورها از بازوهای همزن بسیار قدرتمند برای ورز دادن و میکس کردن این تودههای ویسکوز و همزمان انتقال حرارت استفاده میکنند.
کاربردهای صنعتی: تولید چسبهای سیلیکونی، رزینهای با ویسکوزیته بالا و پلیمرهای خاص.
راکتور استریفیکاسیون
این راکتورها برای واکنشهای پلیمریزاسیون مرحلهای مانند تولید پلیاستر طراحی میشوند. ویژگی کلیدی آنها، توانایی کار در خلاء و دمای بالا برای خارج کردن محصولات جانبی از محیط واکنش است تا واکنش به سمت تولید پلیمر با وزن مولکولی بالا پیش برود. یکی دیگر از تخصصهای ما، طراحی راکتورهای استریفیکاسیون با سیستم خلاء و کنترل دمای دقیق است.
راکتور امولوسیونی
این راکتورها که معمولاً از نوع مخزنی هستند، برای فرایند امولسیون بهینهسازی شدهاند. سیستم همزن آنها باید بتواند امولسیون را پایدار نگه دارد بدون آنکه آن را بشکند و سیستم انتقال حرارت باید قادر به دفع سریع گرمای واکنش باشد.
راکتور اینورس امولسیونی
این راکتور برای پلیمریزاسیون مونومرهای محلول در آب در یک فاز پیوسته روغنی (برعکس امولسیون معمولی) به کار میرود. طراحی این راکتورها مشابه راکتورهای امولسیونی است اما انتخاب جنس بدنه و سیستم همزن با توجه به فاز روغنی متفاوت خواهد بود.
پارامترهای کلیدی کنترل فرایند در پلیمریزاسیون
یک راکتور با طراحی مناسب، تنها نیمی از راه برای رسیدن به یک محصول باکیفیت است. نیم دیگر، کنترل دقیق پارامترهای عملیاتی در حین واکنش است. این سیستمهای کنترلی هستند که تکرارپذیری تولید و یکنواختی محصول از یک بچ به بچ دیگر را تضمین میکنند. در ادامه، سه سیستم کنترلی حیاتی در راکتورهای پلیمریزاسیون را بررسی میکنیم.
سیستم کنترل دما و انتقال حرارت
بسیاری از واکنشهای پلیمریزاسیون به شدت گرمازا هستند، یعنی در حین واکنش، مقدار قابل توجهی گرما آزاد میشود. اگر این گرما به طور موثر از محیط واکنش خارج نشود، افزایش کنترلنشده دما میتواند منجر به نتایج صنعتی نامطلوبی شود، از جمله:
- کاهش وزن مولکولی پلیمر
- ایجاد واکنشهای جانبی و کاهش خلوص محصول
- تغییر رنگ و تخریب خواص پلیمر
- در موارد حاد، بروز پدیده فرار واکنش که یک خطر ایمنی جدی محسوب میشود.
برای مدیریت این چالش، راکتورهای صنعتی به سیستمهای انتقال حرارت مهندسیشده مجهز میشوند:
- ژاکتهای حرارتی: رایجترین روش برای افزودن یا خارج کردن گرما از دیواره راکتور.
- کویلهای داخلی : برای افزایش سطح انتقال حرارت و کنترل سریعتر دما در راکتورهای با حجم بالا.
- کندانسورهای برگشتی: در فرایندهای محلولی، با جوشاندن و میعان مجدد حلال، به طور موثری حرارت را از سیستم خارج میکنند.
سیستم همزن و مدیریت ویسکوزیته
سیستم همزن در یک راکتور دو وظیفه اصلی بر عهده دارد:
- یکنواختی غلظت و دما: با میکس کردن مداوم، از توزیع یکنواخت مونومر و آغازگر و همچنین جلوگیری از ایجاد نقاط داغ اطمینان حاصل میکند.
- تسهیل انتقال حرارت: با جابجا کردن مواد از مرکز راکتور به سمت دیوارههای خنکشونده، به فرآیند انتقال حرارت کمک میکند.
چالش اصلی در این بخش، افزایش شدید گرانروی با پیشرفت واکنش است. یک سیستم همزن که در ابتدای واکنش به خوبی کار میکند، ممکن است در ویسکوزیتههای بالا کارایی خود را از دست داده و قادر به میکس کردن کل محتوای راکتور نباشد. راهحل این مشکل در انتخاب مهندسیشده اجزای سیستم همزن است:
- انتخاب نوع ایمپلر (Impeller): بر اساس ویسکوزیته فرایند، از ایمپلرهای مختلفی استفاده میشود؛ از پرههای توربینی برای ویسکوزیته پایین گرفته تا ایمپلرهای لنگری (Anchor) و همزنهای نواری (Ribbon Agitators) برای مواد بسیار غلیظ و خمیری.
- بافلگذاری (Baffling): نصب صفحات بافل بر روی دیواره داخلی راکتور، از ایجاد گرداب (Vortex) جلوگیری کرده و الگوی جریان را بهبود میبخشد تا میکس عمودی و افقی به بهترین شکل انجام شود.
سیستم کنترل فشار و افزودن واکنشدهندهها
بسته به نوع فرایند، واکنش ممکن است تحت فشار مثبت (برای مونومرهای گازی) یا در شرایط خلاء (برای خروج محصولات جانبی در پلیمریزاسیون مرحلهای) انجام شود. کنترل دقیق این فشار برای پیشبرد صحیح واکنش و حفظ ایمنی ضروری است. راکتورهای مدرن مجهز به سیستمهای کنترل فشار اتوماتیک و شیرهای اطمینان برای جلوگیری از خطرات ناشی از افزایش فشار هستند.
علاوه بر این، در فرایندهایی مانند نیمهپیوسته (Semi-Batch)، نرخ واکنش از طریق کنترل نرخ افزودن مواد اولیه کنترل میشود. این کار نیازمند استفاده از پمپهای تزریق دقیق و نازلهای ورودی با طراحی مناسب است.
مثالهای صنعتی و کاربردهای پلیمرهای اصلی
در این بخش، مفاهیم فنی و فرایندهایی که تا اینجا بررسی کردیم را به محصولات واقعی و ملموس در دنیای صنعت متصل میکنیم. شناخت کاربرد نهایی پلیمرها به درک بهتر الزامات تولید و فرایند کمک شایانی میکند.
پلیمرهای پرمصرف
این گروه، شامل پلیمرهایی است که در حجم بسیار بالا تولید شده و در کاربردهای عمومی و روزمره مورد استفاده قرار میگیرند.
- پلیاتیلن (PE): پرمصرفترین پلاستیک در جهان که از طریق پلیمریزاسیون زنجیرهای مونومر اتیلن تولید میشود. دو گرید صنعتی اصلی آن عبارتند از:
- پلیاتیلن سنگین (HDPE): به دلیل ساختار خطی، دارای چگالی و سختی بالایی است و در ساخت انواع مخازن، لولهها، و بطریهای مقاوم به کار میرود.
- پلیاتیلن سبک (LDPE): ساختار شاخهای آن باعث انعطافپذیری و چگالی کمتر میشود و گزینهای ایدهآل برای تولید انواع فیلم، کیسههای پلاستیکی و بستهبندیهای انعطافپذیر است.
- پلیپروپیلن (PP): این پلیمر به دلیل مقاومت شیمیایی خوب، سختی مناسب و دمای ذوب بالاتر نسبت به پلیاتیلن، کاربردهای گستردهای دارد. از قطعات خودرو (سپر، داشبورد) گرفته تا ظروف نگهداری مواد غذایی، الیاف فرش و منسوجات، همگی از این پلیمر بهره میبرند.
- پلیوینیل کلراید (PVC): یکی از متنوعترین پلیمرها که به دو شکل اصلی سخت و انعطافپذیر استفاده میشود. نوع سخت آن (uPVC) در ساخت پروفیلهای در و پنجره و لولههای ساختمانی کاربرد دارد، در حالی که نوع انعطافپذیر آن با افزودن نرمکنندهها، در تولید روکش کابلهای برق، کفپوشها و چرم مصنوعی به کار میرود.
پلیمرهای مهندسی
این دسته از پلیمرها برای کاربردهایی انتخاب میشوند که نیاز به خواص مکانیکی و حرارتی بالاتری نسبت به پلیمرهای پرمصرف دارند.
- پلیآمیدها (PA) یا نایلونها: این پلیمرها که از طریق پلیمریزاسیون مرحلهای تولید میشوند، به استحکام، مقاومت به سایش و سختی بالا مشهور هستند. این ویژگیها آنها را برای ساخت قطعاتی مانند چرخدندهها، یاتاقانها، طنابهای صنعتی و الیاف مستحکم مناسب میسازد.
- پلیکربناتها (PC): ویژگی اصلی این پلیمرها، ترکیب منحصربهفردی از استحکام ضربهای بسیار بالا و شفافیت نوری عالی است. این خواص، پلیکربنات را به مادهای ایدهآل برای ساخت شیشههای ایمنی، عینکهای محافظ، دیسکهای فشرده (CD/DVD) و بدنهی تجهیزات الکترونیکی تبدیل کرده است.
پرسش و پاسخهای متداول در مورد پلیمریزاسیون (FAQ)
در این بخش به چند سوال کلیدی و پرتکرار که معمولاً برای متخصصان فنی در حوزه پلیمریزاسیون پیش میآید، به صورت مستقیم و خلاصه پاسخ میدهیم.