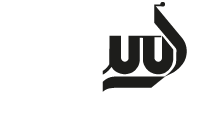
EP تسمه نقاله چیست؟
در نگاه اول، EP (منجید) فقط یک ترکیب دوحرفی ساده در برچسب مشخصات یک نوار صنعتی بهنظر میرسد؛ اما همین دو حرف، نشانگر یک ساختار تقویتکننده کلیدی در تسمههای لاستیکی است که مستقیماً عملکرد، دوام و سازگاری نوار با محیط کار را تعیین میکند. بسیاری از مهندسان و مسئولان خرید با واژه EP تسمه نقاله مواجه میشوند، اما شناخت فنی آن چیزیست که در تصمیمگیری نهایی تفاوت ایجاد میکند.
اگر میخواهید بدانید EP تسمه نقاله دقیقاً از چه جنسی است، چه وظیفهای در ساختار تسمه نقاله دارد، چگونه گریدبندی میشود و بر چه اساسی باید آن را انتخاب کرد، ادامه این مقاله پاسخی دقیق، فنی و کاربردی برایتان خواهد داشت.
EP در تسمه نقاله چیست؟
در ساخت تسمههای لاستیکی صنعتی، منجید یا EP تسمه نقاله نقش اصلی در پایداری مکانیکی، تحمل بار و طول عمر نوار دارد. ساختاری که با حروف EP شناخته میشود، یکی از رایجترین و کارآمدترین انواع منجید است که در تسمههای چندلایه مورد استفاده قرار میگیرد. این ساختار از الیاف پلیاستر در جهت طولی (تار) و پلیآمید در جهت عرضی (پود) تشکیل شده و ترکیب این دو جنس، ویژگیهای مکانیکی خاصی را به نوار منتقل میکند.
پلیاستر در راستای طولی باعث میشود نوار در برابر کششهای پیوسته پایداری بیشتری داشته باشد و فرم هندسی خود را حفظ کند. از سوی دیگر، پلیآمید با جذب انرژی ناشی از تنشهای متناوب، به انعطاف نوار در عرض کمک میکند. این توازن بین استحکام و انعطافپذیری، منجید EP را برای کاربردهایی مناسب کرده که در آنها هم فشار مکانیکی بالا وجود دارد و هم شرایط کاری متغیر است.
در مقایسه با منجید NN که در هر دو جهت از نایلون استفاده میکند، EP رفتار پایدارتری در برابر تغییر طول نشان میدهد و دقت ابعادی بهتری در شرایط کاری سنگین دارد. از طرف دیگر، ساختار ST یا همان کابل فولادی که در تسمههای با طول مسیر بالا یا بارهای شدید استفاده میشود، هرچند از نظر کششی قویتر است، اما در بسیاری از پروژهها بهدلیل وزن، هزینه و محدودیت در نصب، انتخاب اول نیست.
در بسیاری از خطوط انتقال مواد فله در صنایع سیمان، معدن، فولاد و پتروشیمی، EP بهعنوان منجیدی استاندارد انتخاب میشود، چرا که در کنار دوام مکانیکی، امکان ترمیم و نصب سریعتری هم نسبت به گزینههای فلزی فراهم میکند. این ساختار طی سالها در پروژههای صنعتی مختلف، بهخوبی از نظر عملکرد و اقتصادی بودن، خود را اثبات کرده است.
ساختار داخلی تسمه نقاله EP
در هر تسمه صنعتی که با منجید EP ساخته میشود، سه لایه اصلی وجود دارد که با دقت و تناسب طراحی میشوند تا نوار در برابر کشش، خمش، سایش و شرایط محیطی عملکرد پایداری داشته باشد. شناخت نقش هر کدام از این لایهها برای انتخاب صحیح ساختار، ضروریست.
در این نوع تسمهها:
- روکش بالا (Top Cover) اولین سطح تماس با ماده انتقالی است. بسته به نوع بار و شرایط خط، ممکن است ضدسایش، مقاوم به حرارت، یا مقاوم در برابر روغن باشد.
- منجید EP (لایه میانی) اسکلت اصلی تسمه است. از چند لایه پارچهای با ترکیب پلیاستر در تار و پلیآمید در پود ساخته میشود. این لایه مسئول مقاومت کششی و پایداری ابعادی نوار است.
- روکش پایین (Bottom Cover) با اجزای مکانیکی مانند رولیکها در تماس است و باید در برابر سایش و ارتعاش مداوم مقاوم باشد.
وقتی از تسمه EP200 یا EP315 صحبت میکنیم، این اعداد به مقاومت کششی منجید در هر لایه (بر حسب نیوتن بر میلیمتر عرض) اشاره دارند. بهطور خلاصه:
گرید منجید | مقاومت کششی هر لایه (N/mm) | کاربرد معمول | ویژگیها |
---|---|---|---|
EP100 | 100 | خطوط سبک، بستهبندی | سبک، انعطافپذیر، مناسب مسیرهای کوتاه |
EP200 | 200 | صنایع معدنی، سیمان | تعادل میان مقاومت و انعطاف، کاربرد عمومی |
EP250 | 250 | بارهای متوسط، شیبدار | مناسب برای مسیرهایی با طول متوسط و فشار نسبی بالا |
EP315 | 315 | فولاد، معدن، پتروشیمی | استحکام بالا، کاهش خزش، مناسب محیطهای سنگین |
EP400 به بالا | 400+ | خطوط فشار بالا یا مسیرهای طولانی | نیازمند طراحی دقیق، روکش مقاومتر، هزینه نصب بالاتر |
تعداد لایهها نیز اهمیت زیادی دارد. مثلاً تسمهای با مشخصات EP200/3 دارای سه لایه منجید با مقاومت کششی ۲۰۰ نیوتن در هر لایه است که مجموع آن، استحکام نهایی نوار را مشخص میکند.
علاوه بر این، کیفیت و تراکم بافت منجید، قطر الیاف و یکنواختی ضخامت آن از عوامل کلیدی در عملکرد تسمه هستند. منجیدی که با بافت دقیق و تراکم بالا تولید شود، کمتر دچار پارگی عرضی میشود و در برابر ضربه و ارتعاش دوام بیشتری دارد. اینجا تنها عدد EP مهم نیست، بلکه کیفیت ساخت آن تعیین میکند که تسمه در شرایط واقعی چقدر قابل اعتماد خواهد بود.
در تولید صنعتی، انتخاب گرید EP تنها یک عدد روی کاغذ نیست؛ این انتخاب باید بر اساس واقعیتهای فنی خط انتقال، نوع بار، شیب مسیر و شرایط محیطی انجام شود. اینجاست که تجربه، آزمون عملی و تحلیل مهندسی اهمیت پیدا میکند.
انواع تسمه نقاله EP
منجید EP در نگاه بسیاری از فعالان صنعتی، صرفاً بهعنوان یک ساختار تقویتی واحد شناخته میشود، اما واقعیت این است که منجید EP خود در انواع متنوعی طراحی و تولید میشود که هرکدام ویژگیهای مکانیکی و عملکردی خاصی دارند. این تفاوتها فقط به مقاومت کششی یا تعداد لایهها محدود نیست و به ترکیب EP با روکشهای تخصصی مقاوم در برابر عوامل محیطی نیز مربوط میشود.
در ادامه، به بررسی دقیقتر انواع تسمه نقاله EP از نظر ساختار داخلی منجید و ویژگیهای لاستیک پوششی میپردازم؛ دستهبندیهایی که شناخت آنها برای انتخاب درست نوار در پروژههای مهندسی ضروری است.
۱. تسمه نقاله EP با روکش مقاوم به شرایط خاص
در تولید صنعتی، منجید EP معمولاً با یکی از سه نوع پوشش اصلی ترکیب میشود، تا برای شرایط محیطی مختلف بهینه شود:
- مقاوم به سایش: این نوع از تسمه نقاله EP برای حمل بارهای خشن، زبر یا دارای لبههای تیز طراحی میشود. لاستیک رویه دارای سختی بالا و فرمول ضدسایش است.
- مقاوم به روغن: مناسب برای انتقال موادی مثل خوراک دام، غلات روغنی یا قطعات آغشته به روانکار. پوشش لاستیکی در این مدل، نسبت به روغنهای معدنی و گیاهی مقاوم است.
- مقاوم به حرارت: در خطوطی که دمای مواد حملشونده به ۱۲۰ درجه یا بیشتر میرسد، EP با روکش مقاوم به حرارت مورد استفاده قرار میگیرد. این تسمهها تغییر شکل نمیدهند و ترک نمیخورند.
در همهی این مدلها، منجید EP ثابت است، اما نوع لاستیک روکش بالا و پایین، بر اساس شرایط محیطی و ماهیت بار تغییر میکند.
۲. EP تکلایه، دولایه و چندلایه
ساختار داخلی تسمه نقاله EP بر اساس تعداد لایههای منجید نیز دستهبندی میشود. این مورد مستقیماً به مقاومت کششی کل نوار و شرایط بارگذاری آن بستگی دارد:
- EP تکلایه (مانند EP160/1): برای بارهای سبک و خطوط با مسیر کوتاه. انعطافپذیرتر و سبکتر است.
- EP دولایه یا سهلایه (مثل EP200/2 یا EP315/3): در بسیاری از صنایع بهعنوان گزینهی عمومی استفاده میشود. مقاومت مناسب در برابر کشش و پارگی دارد.
- EP چندلایه (چهار یا پنج لایه): مخصوص کاربردهای سنگین و مسیرهای شیبدار. در این تسمهها، هر لایه منجید بهدقت با لایه لاستیکی میانی ترکیب شده تا چسبندگی بین لایهها حفظ شود.
انتخاب بین این ساختارها باید با توجه به فشار وارد بر تسمه، نوع مواد حملشده و مشخصات خط انتقال انجام شود. در خطوطی که تسمه تحت کشش بالا یا بارهای مقطعی سنگین قرار دارد، استفاده از EP چندلایه، از نظر ایمنی و دوام توصیه میشود.
در عمل، پاسخ به این سؤال که “EP تسمه نقاله چیست؟” فقط به تعریف منجید محدود نمیشود؛ بلکه باید آن را در ترکیب با پوشش لاستیکی و طراحی لایهای دید. همین هماهنگی میان اجزا، است که تعیین میکند تسمه در خط تولید چطور رفتار کند و چند سال بدون توقف کار کند.
کاربرد EP در صنایع مختلف
انتخاب منجید EP بهعنوان ساختار اصلی در تولید تسمههای لاستیکی، بهدلیل توازن بین استحکام کششی، انعطافپذیری و مقاومت محیطی، باعث شده تا تسمه نقاله EP بهعنوان گزینهی استاندارد در طیف وسیعی از صنایع مورد استفاده قرار گیرد. در بسیاری از پروژههای طراحی و ساخت سیستمهای انتقال، این نوع تسمه نهفقط بهخاطر ویژگیهای فیزیکی، بلکه بهدلیل قابلیت سفارشیسازی در گرید منجید و نوع روکش، انتخاب اول کارشناسان فنی است.
کاربردهای رایج تسمه نقاله EP عبارتند از:
۱. معدن و کارخانههای سیمان
در محیطهایی با بار سنگین، گرد و غبار زیاد و تنشهای ضربهای بالا، استفاده از تسمهای با منجید EP باعث میشود تسمه فرم خود را در طول مسیر حفظ کند و در برابر سایش مداوم مقاومت بالایی از خود نشان دهد. مقاومت کششی منجید و چسبندگی مناسب لایهها از جداشدگی و پارگی عرضی جلوگیری میکند.
۲. صنایع فولاد و پتروشیمی
در خطوطی که تسمه در مجاورت گرمای بالا، بخارات شیمیایی یا ذرات خورنده قرار دارد، تسمه نقاله EP با روکش مقاوم به حرارت یا اسید میتواند عملکردی پایدار و طولانیمدت ارائه دهد. منجید EP بهدلیل پایداری ابعادی، در این صنایع دچار خزش یا افت کشش نمیشود.
۳. بستهبندی و صنایع غذایی
در این حوزهها، انعطاف تسمه و یکنواختی حرکت اهمیت بالایی دارد. تسمههایی که با منجید EP ساخته میشوند، بهدلیل قابلیت تولید در ضخامتهای متنوع و امکان استفاده از روکشهای بهداشتی، برای انتقال محصولات بستهبندیشده، جعبهها و مواد غذایی خشک، گزینهای مناسب بهشمار میروند.
راهنمای انتخاب تسمه نقاله EP
برای انتخاب دقیق تسمه نقاله EP، تنها شناخت گرید منجید یا ضخامت روکش کافی نیست. هر خط انتقال ویژگیهای فنی خاص خود را دارد و انتخاب صحیح باید بر پایهی مجموعهای از پارامترهای مهندسی انجام شود. در پروژههایی که طراحی و ساخت سیستم انتقال بهصورت سفارشی انجام میشود، چند عامل کلیدی تعیینکنندهی ساختار نهایی تسمه هستند:
عوامل مؤثر در انتخاب نوع ep
- ظرفیت حمل (T/H یا kg/h): حجم یا جرم مادهی منتقلشونده در واحد زمان، بهطور مستقیم روی انتخاب تعداد لایههای منجید و مقاومت کششی مؤثر است.
- نوع ماده حملشونده: مواد تیز، ساینده، چرب یا داغ نیاز به انتخاب روکش مناسب و در مواردی افزایش تعداد لایههای منجید EP دارند.
- زاویه شیب مسیر: در مسیرهای با شیب بالا، نیاز به تسمهای با چسبندگی بهتر و مقاومت عرضی بیشتر احساس میشود. در این موارد، ضخامت پوشش پایین و گرید EP بالاتر پیشنهاد میشود.
- طول خط و تعداد رولیک: هرچه مسیر طولانیتر باشد، فشار توزیعشده روی تسمه بیشتر خواهد شد. انتخاب تسمهی بلند باید با دقت در ساختار منجید و فرمول لاستیک انجام شود.
چکلیست پیشنهادی برای انتخاب صحیح
- بررسی دقیق ظرفیت حمل مواد در ساعت
- تعیین نوع مادهی منتقلشونده (زبر، داغ، روغنی، سنگین)
- اندازهگیری طول خط و تعداد نقاط بارگیری
- مشخصکردن زاویه شیب مسیر
- انتخاب گرید منجید EP متناسب با کشش خط
- انتخاب روکش مقاوم به سایش، روغن یا حرارت بر اساس شرایط کاری
- تعیین تعداد لایههای مورد نیاز با توجه به فشار و انعطاف
- بررسی برند و کیفیت ساخت تسمه از نظر یکنواختی منجید و چسبندگی لایهها
در کارگاه ما، قبل از تولید هر سفارش، این چکلیست بهصورت دقیق بررسی میشود تا تسمهای که تولید میشود، دقیقاً منطبق با نیاز خط و عمر مورد انتظار آن باشد.
تفاوت EP100، EP200، EP315 و سایر گریدها
اعدادی مانند EP100، EP200 یا EP315، بهطور دقیق به مقاومت کششی لایه منجید در هر میلیمتر از عرض تسمه اشاره دارند. این اعداد صرفاً کد نیستند، بلکه شاخصی از میزان فشار مکانیکی قابل تحمل توسط ساختار منجید EP هستند. در عمل، این تفاوت عددی، به معنای تفاوت در رفتار تسمه در شرایط بارگذاری واقعی است.
در پروژههایی با حجم بالای انتقال یا طول خط زیاد، معمولاً از گریدهای بالاتر استفاده میشود. بهعنوان مثال، در خطوط معدن یا صنایع سنگین، جایی که بار پیوسته و ضربهای به نوار وارد میشود، EP315 یا EP400 پایداری بیشتری ایجاد میکند و خزش تسمه به حداقل میرسد. در مقابل، برای مسیرهای کوتاه یا سیستمهای سبک مانند خطوط بستهبندی، استفاده از گرید EP100 یا EP125 کاملاً منطقی است؛ هم از نظر عملکرد و هم از نظر هزینه.
نکتهی کلیدی در انتخاب این گریدها، صرفاً عدد درجشده نیست، بلکه تطابق آن با تعداد لایهها، ضخامت روکش، و نحوه اتصال دو سر تسمه است. بارها دیدهایم که انتخاب گرید بالا بدون توجه به این عوامل، نهتنها به عملکرد بهتر منجر نشده، بلکه باعث افزایش غیرضروری هزینه و سختی در نصب شده است.
هر گرید، رفتار خاصی در برابر کشش، خمش و شرایط دینامیک دارد. شناخت این رفتار، نیازمند تجربه عملی در کنار تحلیل فنی است؛ چیزی که فقط از طریق کار مستمر با مواد، تست در شرایط واقعی، و بازخورد از خطوط نصبشده بهدست میآید.
قیمت تسمه نقاله EP و عوامل مؤثر بر آن
قیمت تسمه نقاله EP تنها به متراژ یا عرض نوار بستگی ندارد؛ بلکه تحتتأثیر مجموعهای از پارامترهای فنی و اقتصادی است که هریک میتوانند قیمت نهایی را بهطور محسوس تغییر دهند. در پروژههای صنعتی، درک دقیق این عوامل برای ارزیابی واقعی هزینهها و مذاکره با تأمینکننده ضروری است.
عوامل مؤثر بر قیمت تسمه منجیددار
- نوع منجید EP و گرید کششی: تسمههای با گرید بالاتر (مثلاً EP315 بهجای EP100) نیاز به الیاف مقاومتر و چسبندگی بالاتر بین لایهها دارند. همین موضوع موجب افزایش قیمت واحد میشود.
- تعداد لایهها: تسمهی EP200/4 (چهار لایه) بهمراتب گرانتر از EP200/2 خواهد بود؛ زیرا مواد اولیه بیشتر و فرآیند پرس سنگینتری نیاز دارد.
- ضخامت روکشها: تسمه با روکش ضخیمتر یا با خواص خاص (مثلاً مقاوم به روغن یا حرارت) به دلیل مصرف بیشتر لاستیک و فرمولاسیون متفاوت، قیمت بالاتری دارد.
- مقاومت ویژه: مقاومت در برابر شعله، مواد اسیدی یا UV باعث تغییر در فرمول لاستیک شده و مستقیماً در هزینه نهایی تأثیرگذار است.
- برند و روش تولید: تسمههای تولیدی با تجهیزات اتوماتیک، قالبگیری یکنواخت و چسبندگی کنترلشده، قیمت بالاتری دارند ولی در خطوط صنعتی پرت کمتری خواهند داشت.
قیمت تقریبی تسمه نقاله EP در ۱۴۰۴
ساختار تسمه | عرض نوار | قیمت هر متر (تخمینی، تومان) |
---|---|---|
EP200/3 با روکش معمولی | ۶۰ سانتیمتر | حدود ۷۵۰٬۰۰۰ تومان |
EP315/4 مقاوم به سایش | ۸۰ سانتیمتر | حدود ۱٬۰۰۰٬۰۰۰ تومان |
EP400/4 مقاوم به حرارت بالا | ۱۰۰ سانتیمتر | ۱٬۳۰۰٬۰۰۰ تا ۱٬۵۰۰٬۰۰۰ تومان |
EP250/2 سبک صنعتی | ۵۰ سانتیمتر | حدود ۶۰۰٬۰۰۰ تومان |
نکته: قیمتها بر اساس دادههای بازار داخلی در اردیبهشت ۱۴۰۴ و بدون احتساب مالیات یا هزینه حمل محاسبه شدهاند. برای دریافت نرخ دقیق، با شماره 09351967545 تماس بگیرید.