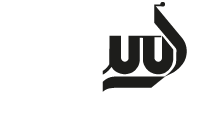
آلومینیوم
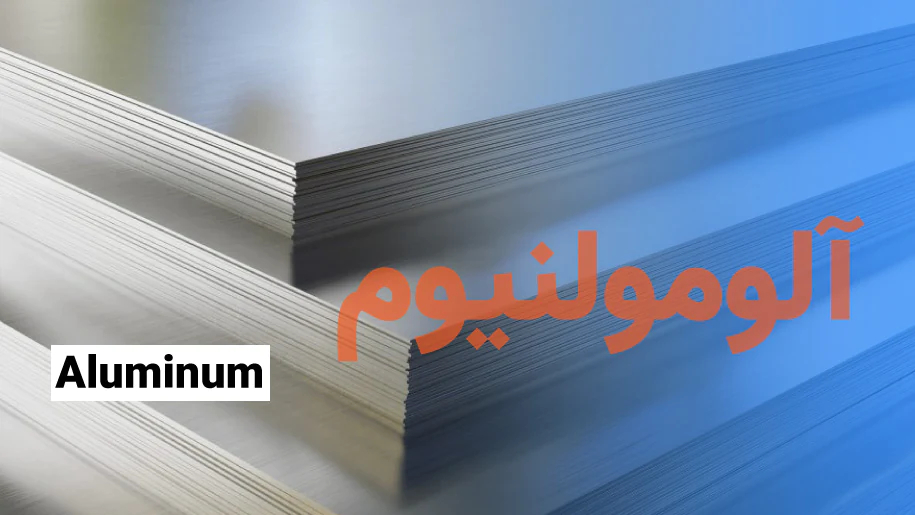
آلومینیوم (Al) فلزی با عدد اتمی 13 است که به دلیل ویژگیهای منحصر به فرد خود، از جمله چگالی پایین (حدود 2.7 گرم بر سانتیمتر مکعب)، رسانایی حرارتی و الکتریکی خوب، چکشخواری بالا، و مقاومت عالی در برابر خوردگی به یکی از پرکاربردترین فلزات صنعتی تبدیل شده است. این عنصر در گروه 13 جدول تناوبی قرار دارد و ساختار بلوری آن مکعبی فشرده (FCC) است که موجب انعطافپذیری و چکشخواری بالای آن میشود.
آلومینیوم به طور عمده از سنگ معدنی بوکسیت استخراج میشود و برای تولید آن از فرایند الکترولیز هال-هرولت استفاده میشود. این فلز به دلیل تشکیل لایه اکسید محافظتی بر سطح خود، در برابر خوردگی به خوبی محافظت میشود که این ویژگی آن را به مادهای مناسب برای کاربرد در صنایع ساختمانی، خودروسازی، و بستهبندی تبدیل کرده است.
تاریخچه فلز آلومینیوم
آلومینیوم، به عنوان یکی از فلزات جوان، برای نخستینبار توسط هانس کریستین ارستد در سال ۱۸۲۵ به صورت آزمایشی استخراج شد. این عنصر در سال ۱۸۲۷ توسط فریدریش وهلر خالصتر شد و اهمیت بیشتری پیدا کرد. تا اواخر قرن نوزدهم، آلومینیوم به دلیل فرآیند پیچیده و پرهزینه استخراج، گرانتر از طلا بود.
تحولی بزرگ در سال ۱۸۸۶ رخ داد، زمانی که شارل هال و پاول هرو به طور همزمان فرآیند الکترولیز را برای تولید صنعتی آلومینیوم توسعه دادند، که به فرآیند هال-هرو معروف شد. پس از آن، کارل بایر در سال ۱۸۸۸ فرآیند بایر را معرفی کرد که تولید آلومینیوم از سنگ معدن بوکسیت را مقرونبهصرفه کرد.
پس از جنگ جهانی دوم، مصرف آلومینیوم به سرعت افزایش یافت و این فلز به دلیل ویژگیهای سبک و مقاوم به خوردگی، به یک عنصر کلیدی در صنایع هوافضا، خودروسازی و ساختمان تبدیل شد. این ویژگیها سبب شد که آلومینیوم به یکی از فلزات مهم صنعتی و اقتصادی در قرن بیستم و بیستویکم تبدیل شود.
عدد اتمی فلز آلومینیوم
عدد اتمی آلومینیوم ۱۳ است، که نشاندهنده تعداد پروتونهای موجود در هسته و نیز تعداد الکترونهای موجود در لایههای الکترونی آن در حالت خنثی میباشد. این عدد جایگاه آلومینیوم را در گروه ۱۳ و دوره سوم جدول تناوبی مشخص میکند. آلومینیوم با این عدد اتمی، دارای ساختار الکترونی [Ne] 3s² 3p¹ است که به آن ویژگیهای فلزی خاصی همچون رسانایی الکتریکی و حرارتی و همچنین واکنشپذیری بالا به دلیل وجود سه الکترون والانس در لایه خارجی میبخشد.
نقطه جوش فلز آلومینیوم
نقطه جوش فلز آلومینیوم برابر با ۲,۴۷۰ درجه سلسیوس (معادل ۴,۴۷۸ درجه فارنهایت) است. این دما نشاندهنده انرژی لازم برای شکستن پیوندهای فلزی قوی بین اتمهای آلومینیوم در ساختار بلوری مکعبی فشرده (FCC) آن میباشد، که در آن اتمها به طور محکم در کنار هم قرار گرفتهاند. نقطه جوش بالای آلومینیوم ناشی از وجود پیوندهای قوی میان اتمهای فلزی در شبکه بلوری است و این خاصیت به آن اجازه میدهد تا در فرآیندهای حرارتی صنعتی و کاربردهایی که دمای بالا و پایداری حرارتی مورد نیاز است، به عنوان فلزی کارآمد به کار رود.
نقطه ذوب آلومینیوم چقدر است؟
نقطه ذوب فلز آلومینیوم برابر با ۶۶۰.۳ درجه سلسیوس (معادل ۱۲۲۰.۵۴ درجه فارنهایت) است. این دما نشاندهنده انرژی لازم برای گسستن پیوندهای فلزی قوی بین اتمهای آلومینیوم در ساختار بلوری مکعبی فشرده (FCC) است که منجر به تبدیل آن از حالت جامد به حالت مایع میشود. ساختار بلوری آلومینیوم و چگالی نسبتاً پایین آن، همراه با این نقطه ذوب خاص، سبب شده است که آلومینیوم به عنوان فلزی چکشخوار و قابلریختهگری شناخته شود. این ویژگیها آن را به یکی از فلزات کلیدی برای فرآیندهای صنعتی حرارتی، به ویژه در ریختهگری آلیاژهای سبک و صنایع هوافضا، تبدیل کرده است.
ساختار اتمی فلز آلومینیوم
فلز آلومینیوم با عدد اتمی ۱۳ دارای ۱۳ پروتون در هسته و ۱۳ الکترون در اطراف هسته است که در لایههای مختلف انرژی توزیع شدهاند. پیکربندی الکترونی آلومینیوم به صورت [Ne] 3s² 3p¹ است که نشان میدهد این عنصر دارای سه الکترون در لایه والانس خود است. از این تعداد، دو الکترون در اوربیتال 3s و یک الکترون در اوربیتال 3p قرار دارد. این پیکربندی به آلومینیوم خواصی مانند رسانایی الکتریکی و حرارتی بالا میبخشد، زیرا الکترونهای لایه والانس به راحتی میتوانند از فلز جدا شوند و در تشکیل پیوندهای فلزی مشارکت کنند.
آلومینیوم در حالت جامد دارای ساختار بلوری مکعبی فشرده (FCC) است که در آن اتمها به صورت نزدیک به هم و با یک چیدمان متقارن قرار دارند. این نوع ساختار باعث میشود آلومینیوم خواص مکانیکی برجستهای نظیر چکشخواری، شکلپذیری، و مقاومت به خستگی فلز داشته باشد. ساختار FCC، که در آن هر اتم با ۱۲ اتم همسایه در تماس است، به آلومینیوم چگالی نسبتاً پایین و استحکام مکانیکی مناسب میدهد، که این ویژگیها آن را به یکی از فلزات کلیدی در صنایع هوافضا، خودروسازی، و ساختمانی تبدیل کرده است.
همچنین، الکترونهای آزاد در ساختار بلوری آلومینیوم، منجر به تشکیل پیوندهای فلزی قوی میشوند که باعث رسانایی حرارتی و الکتریکی بالا در این فلز میگردد. این پیوندها به دلیل وجود الکترونهای والانس، آلومینیوم را به عنصری با خواص استثنایی از جمله مقاومت به خوردگی تبدیل کرده است، که آن را برای استفاده در شرایط محیطی خورنده بسیار مناسب میسازد.
چگالی آلومینیوم چقدر است؟
چگالی فلز آلومینیوم در دمای اتاق برابر با ۲.۷۰ گرم بر سانتیمتر مکعب است. این چگالی نسبتاً پایین ناشی از ساختار FCC آلومینیوم و جرم اتمی نسبتاً پایین (۲۶.۹۸ گرم بر مول) میباشد. در ساختار FCC، هر اتم آلومینیوم با ۱۲ اتم همسایه در تماس است که این چیدمان منظم و فشرده به فلز ویژگیهای چکشخواری و شکلپذیری بالا را میدهد.
چگالی پایین آلومینیوم یکی از دلایل اصلی استفاده گسترده آن در صنایع هوافضا، خودروسازی، و ساختمانی است، جایی که کاهش وزن و در عین حال حفظ استحکام مکانیکی اهمیت دارد. پیوندهای فلزی قوی میان اتمها در این ساختار بلوری باعث میشود که آلومینیوم خواصی همچون مقاومت به خستگی، استحکام مناسب و رسانایی حرارتی و الکتریکی مطلوب داشته باشد. این ترکیب ویژگیها، آلومینیوم را به یکی از فلزات کلیدی و استراتژیک در بسیاری از صنایع تبدیل کرده است.
معرفی انواع آلیاژهای آلومینیوم
آلیاژهای آلومینیوم به دلیل انعطافپذیری بالا در ترکیب با سایر فلزات و امکان تقویت خواص آن، در بسیاری از صنایع نقش کلیدی دارند. افزودن عناصر مختلف به آلومینیوم، باعث بهبود ویژگیهایی مانند مقاومت به خوردگی، استحکام مکانیکی، چکشخواری، و رسانایی الکتریکی و حرارتی میشود. این آلیاژها به واسطه وزن سبک و کارایی بالا، در صنایعی نظیر هوافضا، خودرو، و ساخت و ساز از اهمیت زیادی برخوردارند. در ادامه، به بررسی تخصصی و معرفی مهمترین آلیاژهای آلومینیوم و خصوصیات برجسته آنها پرداخته میشود:
آلیاژ آلومینیوم-مس (Series 2000)
این آلیاژها با افزودن مس به آلومینیوم، استحکام مکانیکی و مقاومت به حرارت فوقالعادهای پیدا میکنند. به دلیل سختی بالا و تحمل فشارهای شدید، بهویژه در دماهای بالا، این آلیاژها در صنایع هوافضا و هواپیماسازی بهطور گستردهای استفاده میشوند. البته به دلیل کاهش مقاومت به خوردگی، معمولاً با پوششدهی محافظتی استفاده میشوند.
آلیاژ آلومینیوم-منیزیم (Series 5000)
این آلیاژها که با اضافه کردن منیزیم تقویت شدهاند، بهخاطر وزن سبک و مقاومت استثنایی به خوردگی در محیطهای دریایی و مرطوب شهرت دارند. این ویژگیها آنها را به گزینهای ایدهآل برای ساخت سازههای دریایی، بدنه کشتیها، مخازن ذخیرهسازی و تجهیزات دریایی تبدیل کرده است. استحکام متوسط و قابلیت شکلپذیری بالا نیز از دیگر ویژگیهای این آلیاژها است.
آلیاژ آلومینیوم-منیزیم-سیلیکون (Series 6000)
این گروه از آلیاژها با داشتن سیلیکون و منیزیم، توازنی عالی بین استحکام، شکلپذیری و مقاومت به خوردگی ایجاد میکنند. این آلیاژها به دلیل قابلیت جوشکاری و اکستروژن عالی، در تولید پروفیلهای ساختمانی، فریمهای در و پنجره، و قطعات خودرو بهطور گسترده استفاده میشوند. سیلیکون در این آلیاژها باعث کاهش میزان انقباض در حین فرآیند ریختهگری میشود.
آلیاژ آلومینیوم-روی-منیزیم (Series 7000)
این آلیاژها که معمولاً با ترکیب روی و منیزیم تقویت میشوند، به دلیل استحکام بسیار بالا و سختی عالی، در کاربردهای نیازمند مقاومت شدید به بارهای مکانیکی، مانند قطعات ساختاری هواپیماها و فریمهای خودروهای مسابقهای مورد استفاده قرار میگیرند. با این حال، این آلیاژها نسبت به خوردگی حساستر هستند و نیاز به پوششهای محافظ دارند.
آلیاژ آلومینیوم-سیلیکون (Al-Si)
آلیاژهای آلومینیوم-سیلیکون بهواسطه نقطه ذوب پایین و قابلیت ریختهگری عالی، بهویژه در تولید قطعات پیچیده با دقت بالا، کاربرد دارند. حضور سیلیکون در این آلیاژها باعث بهبود خواص روانکاری و کاهش خوردگی میشود. از این آلیاژها بهطور گسترده در ساخت پیستونها، بلوکهای موتور و قطعات خودرویی که نیازمند مقاومت در برابر حرارت و فشار بالا هستند، استفاده میشود.
آلیاژ آلومینیوم-لیتیم (Al-Li)
این آلیاژها به دلیل وزن بسیار کم و استحکام بالا، بهویژه در صنایعی مانند هوافضا و نظامی که به کاهش وزن و افزایش استحکام نیاز دارند، محبوبیت دارند. لیتیم در این ترکیب علاوه بر کاهش وزن مخصوص، موجب افزایش سختی و استحکام نیز میشود، که این آلیاژها را برای استفاده در ساختارهای فضایی، اجزای هواپیماها و ماهوارهها ایدهآل میسازد.
کاربردهای صنعتی فلز آلومینیوم
فلز آلومینیوم به دلیل خواص منحصر به فرد خود نظیر سبکوزنی، مقاومت به خوردگی، هدایت حرارتی و الکتریکی بالا و قابلیت آلیاژسازی با سایر فلزات، در بسیاری از صنایع به عنوان یک فلز استراتژیک و چندمنظوره مورد استفاده قرار میگیرد. در ادامه برخی از مهمترین کاربردهای صنعتی عبارتند از:
- صنعت هوافضا: در این صنعت، آلومینیوم به دلیل نسبت استحکام به وزن بالا و مقاومت در برابر خوردگی، یکی از اجزای کلیدی در ساخت بدنه و قطعات هواپیماها، موشکها و فضاپیماها است. استفاده از آلیاژهای آلومینیوم بهویژه در بخشهایی که نیاز به تحمل تنشهای مکانیکی و دماهای بالا وجود دارد، نظیر پوستههای خارجی و اجزای سازهای حیاتی، ضروری است. آلیاژهای سری 7000 که ترکیبی از آلومینیوم و روی هستند، بهطور ویژه برای این صنعت توسعه داده شدهاند.
- صنعت خودروسازی: در حوزه خودروسازی، آلومینیوم بهدلیل کاهش وزن خودروها و بهبود مصرف سوخت، به یکی از مواد اولیه مهم تبدیل شده است. آلیاژهای آلومینیوم در ساخت بدنه، موتور، سیستمهای انتقال قدرت و چرخها استفاده میشوند. بهخصوص در خودروهای الکتریکی و هیبریدی، آلومینیوم بهدلیل کاهش وزن کل خودرو، عملکرد بهتر باتریها و افزایش برد خودرو نقش کلیدی دارد.
- صنعت ساختمانی: در صنعت ساختمانسازی، آلومینیوم بهدلیل مقاومت عالی در برابر خوردگی، سبکی و دوام طولانی، در ساخت پنجرهها، نمای ساختمانها، دربها و سازههای سبک مورد استفاده قرار میگیرد. آلیاژهای آلومینیوم، بهویژه آلیاژهای سری 6000 که شامل آلومینیوم و منیزیم هستند، بهدلیل قابلیت جوشکاری و مقاومت به خوردگی بالا، در سازههای فلزی و ساختمانهای بلند بهکار میروند.
- صنایع بستهبندی: آلومینیوم در بستهبندی مواد غذایی، دارویی و محصولات صنعتی بهدلیل ویژگیهای غیرقابل نفوذ و مقاومت در برابر اکسیداسیون، کاربرد فراوانی دارد. آلومینیوم فویل یکی از پرکاربردترین محصولات در این صنعت است که بهطور عمده در بستهبندیهای مواد غذایی حساس به نور و هوا مورد استفاده قرار میگیرد. خاصیت بازیافتپذیری بالا و کاهش هزینههای تولید از دلایل اصلی استفاده گسترده از آلومینیوم در بستهبندیها است.
- صنایع الکتریکی و الکترونیک: هدایت الکتریکی و حرارتی آلومینیوم باعث شده که در کابلهای انتقال برق، تجهیزات الکترونیکی و سیستمهای خنککننده بهطور گسترده بهکار رود. همچنین، در هیتسینکها و قطعات خنککننده در تجهیزات الکترونیکی، به دلیل وزن سبک و قابلیت انتقال حرارت بالا، آلومینیوم بهعنوان یک انتخاب اصلی شناخته میشود.
- صنعت دریایی: آلومینیوم در محیطهای دریایی بهدلیل مقاومت به خوردگی بالا و سبکی، در ساخت بدنه قایقها، کشتیها و تجهیزات دریایی مورد استفاده قرار میگیرد. استفاده از آلومینیوم به کاهش وزن سازهها و افزایش کارایی آنها در برابر حملات نمکی محیطهای دریایی کمک میکند.
- صنعت حمل و نقل ریلی: آلومینیوم به دلیل کاهش وزن و بهبود بازده انرژی، در ساخت قطعات قطارها، متروها و سایر وسایل نقلیه ریلی بهکار میرود. آلیاژهای آلومینیوم در این صنعت به کاهش مصرف انرژی و بهبود سرعت و عملکرد این وسایل نقلیه کمک میکنند.
روشهای استخراج و تولید آلومینیوم
آلومینیوم بهطور طبیعی بهصورت خالص یافت نمیشود و معمولاً بهعنوان ترکیبی از اکسیدها در سنگ معدنی بوکسیت موجود است. فرآیند تولید آلومینیوم از بوکسیت، یک فرآیند دو مرحلهای پیچیده شامل تولید آلومینا (Al₂O₃) و الکترولیز آلومینا برای استخراج آلومینیوم خالص است. در ادامه به بررسی دقیقتر هر مرحله میپردازیم:
1. استخراج آلومینا از بوکسیت (فرآیند بایر)
بوکسیت که غنی از هیدروکسیدهای آلومینیوم است، ابتدا باید برای تولید آلومینا، تصفیه شود. این فرآیند که به نام فرآیند بایر شناخته میشود، شامل مراحل زیر است:
- انحلال بوکسیت: در این مرحله، بوکسیت در محلول هیدروکسید سدیم (NaOH) تحت فشار و دمای بالا حل میشود تا هیدروکسیدهای آلومینیوم بهصورت محلول در بیایند و ناخالصیها مانند سیلیکا و اکسیدهای آهن جدا شوند.
- تهنشینی آلومینا: پس از انحلال، محلول بهصورت کنترلشده خنک میشود و طی این فرآیند، هیدروکسید آلومینیوم بهصورت کریستالهای جامد تهنشین میشود.
- کلسینه کردن: هیدروکسید آلومینیوم جامد حاصل، در دماهای بالا (معمولاً بالای 1000 درجه سانتیگراد) تحت عملیات کلسیناسیون قرار میگیرد تا آب موجود از آن جدا شود و آلومینا (Al₂O₃) خالص به دست آید.
2. تبدیل آلومینا به آلومینیوم (فرآیند هال-هرولت)
پس از تولید آلومینا، برای استخراج آلومینیوم خالص باید از فرآیند الکترولیز استفاده شود. فرآیند هال-هرولت اصلیترین روش صنعتی برای این منظور است. در این روش:
- حل شدن آلومینا: آلومینا در دمای بالا در داخل یک حمام الکترولیتی از کریولیت مذاب (Na₃AlF₆) حل میشود. کریولیت دمای ذوب آلومینا را به میزان قابل توجهی کاهش میدهد و محیط مناسب برای الکترولیز را فراهم میکند.
- واکنشهای الکترولیتی: جریان الکتریکی قوی به حمام الکترولیتی اعمال میشود. در این فرآیند، یونهای آلومینیوم (+Al³) در کاتد کاهش مییابند و به آلومینیوم فلزی تبدیل میشوند، درحالیکه اکسیژن در آند اکسید شده و بهصورت گاز O₂ آزاد میشود.
- تشکیل آلومینیوم خالص: آلومینیوم تولید شده در کاتد به دلیل چگالی بالاتر در کف سلول الکترولیتی تهنشین شده و بهصورت مایع جمعآوری میشود. این فلز مایع پس از جمعآوری و خنک شدن به شمشهای آلومینیوم تبدیل میشود.
3. تصفیه و قالبگیری
آلومینیوم خام به دست آمده از فرآیند هال-هرولت به دلیل وجود ناخالصیهای مختلف مانند آهن و سیلیکون، نیاز به تصفیه دارد. این تصفیه معمولاً از طریق فرآیند تصفیه حرارتی یا فیلترهای سرامیکی انجام میشود تا آلومینیوم با خلوص بالا (بیش از 99.9%) به دست آید.
پس از تصفیه، آلومینیوم به صورت شمشهای استاندارد ریختهگری میشود. این شمشها میتوانند به روشهای مختلف نورد، اکستروژن یا ریختهگری به محصولات نیمهتمام مانند ورقها، میلهها و پروفیلها تبدیل شوند.
4. تولید آلیاژهای آلومینیوم
برای کاربردهای صنعتی خاص، آلومینیوم خالص اغلب با سایر عناصر مانند مس، منیزیم، سیلیکون و منگنز آلیاژ میشود. این آلیاژها با تغییر خواص مکانیکی، مقاومت به خوردگی، و قابلیت شکلدهی به نیازهای مختلف صنعتی مانند هوافضا، خودروسازی و صنایع ساختمانی پاسخ میدهند.
5. بازیافت آلومینیوم
آلومینیوم یکی از فلزاتی است که بهصورت کامل قابل بازیافت است و فرآیند بازیافت آن نیاز به مصرف انرژی بسیار کمتری نسبت به تولید اولیه دارد. در بازیافت آلومینیوم، فلزات ضایعاتی ذوب شده و پس از تصفیه، مجدداً به محصولات قابل استفاده تبدیل میشوند. بازیافت آلومینیوم نهتنها باعث صرفهجویی در انرژی میشود بلکه به حفظ منابع طبیعی نیز کمک میکند.
این فرآیندها بیانگر روشهای پیچیده و انرژیبر تولید آلومینیوم از بوکسیت تا محصول نهایی است که در صنایع پیشرفته بهطور گسترده استفاده میشود.
منابع و ذخایر بوکسیت در ایران
آلومینیوم، همانطور که میدانید، از سنگ معدنی بوکسیت استخراج میشود که مهمترین منبع آلومینیوم در جهان است. ایران به دلیل موقعیت جغرافیایی و شرایط زمینشناسی خاص خود، دارای منابع قابل توجهی از بوکسیت است، اما این ذخایر به اندازه برخی از کشورهای بزرگ تولیدکننده آلومینیوم گسترده نیستند.
در ایران، مهمترین معادن بوکسیت در مناطق زیر قرار دارند:
- معدن بوکسیت جاجرم (استان خراسان شمالی): بزرگترین و مهمترین معدن بوکسیت در ایران است. این معدن نقش حیاتی در تأمین مواد اولیه برای تولید آلومینا در ایران دارد. از بوکسیت جاجرم برای تأمین کارخانه آلومینای جاجرم استفاده میشود که تولیدکننده اصلی آلومینا در کشور است.
- معدن بوکسیت سراب (استان آذربایجان شرقی): این معدن نیز از دیگر منابع مهم بوکسیت در ایران محسوب میشود، اما حجم تولید آن در مقایسه با معدن جاجرم کمتر است.
- معدن بوکسیت آبخورک (استان چهارمحال و بختیاری): این معدن یکی از معادن کوچکتر بوکسیت در ایران است و بیشتر در جهت تأمین نیازهای داخلی کاربرد دارد.
با وجود این منابع، ذخایر بوکسیت ایران محدود بوده و پاسخگوی تمامی نیازهای تولید آلومینیوم در کشور نیست. به همین دلیل، ایران برای تأمین بخشی از مواد اولیه خود به واردات بوکسیت از کشورهای دیگر متکی است.
تولید آلومینیوم در ایران
تولید آلومینیوم در ایران به دو صورت انجام میشود:
- تولید آلومینا: آلومینا که ماده اولیه برای تولید آلومینیوم است، از فرآوری بوکسیت در کارخانههایی مانند کارخانه آلومینای جاجرم تولید میشود.
- تولید آلومینیوم اولیه: ایران با وجود ذخایر محدود بوکسیت، از لحاظ تولید آلومینیوم در منطقه نقش مهمی ایفا میکند. شرکتهایی مانند ایرالکو (شرکت آلومینیوم ایران)، سالکو (شرکت آلومینیوم جنوب) و المهدی، از مهمترین تولیدکنندگان آلومینیوم اولیه در ایران هستند.
وضعیت آلومینیوم در جهان
در سطح جهانی، کشورهای دارای بیشترین ذخایر بوکسیت و تولید آلومینیوم شامل موارد زیر هستند:
- استرالیا: بزرگترین تولیدکننده بوکسیت و آلومینا در جهان. این کشور دارای معادن بسیار غنی از بوکسیت است و از این نظر در رتبه اول جهانی قرار دارد.
- چین: با وجود اینکه چین ذخایر داخلی بوکسیت محدودی دارد، اما بهعنوان بزرگترین تولیدکننده آلومینیوم اولیه در جهان شناخته میشود. چین بخشی از بوکسیت مورد نیاز خود را از کشورهای دیگر وارد میکند.
- گینه: این کشور آفریقایی دارای یکی از بزرگترین ذخایر بوکسیت در جهان است و بهعنوان تأمینکننده اصلی مواد اولیه برای کشورهای تولیدکننده آلومینیوم محسوب میشود.
- برزیل: یکی دیگر از کشورهای بزرگ تولیدکننده بوکسیت و آلومینیوم است که در صنعت جهانی نقش مهمی ایفا میکند.
با توجه به افزایش تقاضا برای آلومینیوم در صنایع مختلف مانند خودروسازی، ساختمانسازی، و بستهبندی، ایران نیز به دنبال توسعه ظرفیتهای تولید خود است. طرحهای توسعهای در بخش تولید آلومینا و آلومینیوم اولیه با تأکید بر افزایش بهرهوری و کاهش وابستگی به واردات مواد اولیه، از جمله برنامههای استراتژیک دولت و شرکتهای بزرگ در ایران است.